Ladle is an important thermal equipment in steel mills, mainly composed of cladding, refractory lining and SN mechanism. With the continuous development of metallurgical technology, the smelting temperature and continuous casting ratio have increased, and the residence time of molten steel in the ladle has been extended. The use of ladle lining directly affects the case production and logistics of steelmaking. Therefore, Find Refractory Materials Network believes that the pursuit of continuous improvement of ladle life, reduction of refractory steel consumption and cost per ton, and improvement of heat turnover rate are the key considerations of the refractory industry under the premise of ensuring safe use.
Design of Refractory Combination for Ladle Lining
The ladle lining can be divided into a working layer and a permanent layer. Different material systems and construction methods are used depending on the difference in the corrosion mechanism of the ladle bottom and the ladle wall.
When selecting the permanent layer material, two factors should be considered: thermal insulation and resistance to molten steel penetration. High-aluminum castables are used as permanent layers. They have high high-temperature strength, good thermal stability, strong resistance to molten steel penetration, and moderate thermal insulation. In order to enhance its thermal insulation performance, a layer of 18mm mullite lightweight bricks is built between the high-aluminum castable and the steel shell. The shell temperature during the ladle turnover process is between 220 and 400°C. This not only reduces the probability of steel leakage, but also reduces the heat loss of molten steel during the entire refining and pouring process, which is conducive to low-temperature steelmaking and reduced energy consumption.
The refractory materials in different parts of the ladle bottom working layer have different damage mechanisms. The ladle bottom is subjected to the impact of molten steel and large static pressure, and requires high-load soft, low creep and thermally stable refractory materials. Corundum castables are selected. In order to improve the anti-scouring performance, large prefabricated blocks are placed in the impact area; in order to facilitate dismantling and reserve certain expansion joints, magnesia carbon bricks are built around the air-permeable seat bricks and nozzle seat bricks.
The ladle wall working layer is subject to carbon absorption, rolling scouring and slag erosion by molten steel during refining. The refractory materials in this part should have good scouring resistance, erosion resistance and oxidation resistance, and require a low thermal expansion rate to keep the ladle wall crack-free. Corundum castables (integrally cast ladle) or prefabricated blocks (brick-built ladle) are selected. Magnesium carbon bricks are built in the slag line. The slag line is subject to slag erosion and arc burning and decarburization, requiring the refractory materials to have strong anti-oxidation and anti-erosion capabilities.
Damage mechanism of ladle lining
1.Permanent layer damage
Taking Baosteel’s ladle as an example, the service life of Baosteel’s permanent layer is generally 600-800 furnaces, that is, four overhaul cycles.
During the overhaul, it was found that there were many criss-crossing cracks in the permanent layer of the ladle wall, and the cracks widened and deepened with the increase in the number of overhauls. Sometimes the cold steel pouring into the working layer would also penetrate into the cracks of the permanent layer, affecting the safety of the ladle. Common causes of cracks include: the volume shrinkage of the low-strength fiberboard after being squeezed creates conditions for the expansion of the permanent layer; the permanent layer castable itself has a certain shrinkage during use, and the casting thickness of the permanent layer of the ladle wall is thin and uneven; the ladle shell undergoes high-temperature deformation, and the mechanical vibration when removing the magnesia carbon bricks during the replacement of the slag line during the overhaul will also accelerate the development of cracks in the permanent layer.
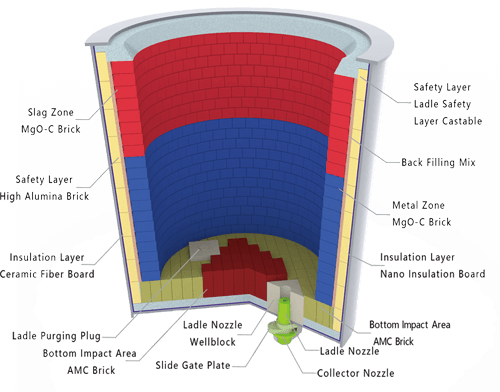
2.Damage to the working layer
During the refining process, desulfurization, deoxidation, decarburization, degassing, alloy composition fine-tuning, removal of non-metallic impurities, inclusion modification, molten steel temperature control and other operations are required in the ladle. The damage process of the working layer of the ladle is different for different refining methods. The main forms of damage are as follows:
Slag line: erosion (main reason), spalling, scouring, hydration (secondary reason)
Ladle wall: erosion (main reason), scouring, hydration (secondary reason)
Ladle bottom: scouring (main reason), erosion, hydration (secondary reason)
Gate system: scouring (main reason), spalling, erosion (secondary reason)
Argon blowing system: spalling (main reason), scouring (secondary reason)
1) Erosion
There are two main types of erosion for the lining of the working layer of the ladle: chemical erosion and oxidative erosion.
Chemical erosion: Acidic substances in iron oxide or slag (such as silicon dioxide) react with the refractory lining. There are chemical reactions between iron oxide, silicon dioxide, calcium oxide, and magnesium oxide. These reactions turn the ladle lining into slag, causing damage to the refractory material.
FeO+MgO=FeOMgO
SiO2+2MgO=2MgOSiO2
CaO+SiO2+MgO=CaOMgOSiO2
Oxidation reaction: Oxidation erosion is a special form of ladle refractory lining, generally refers to the erosion caused by the reaction between carbon in refractory bricks and iron oxide or oxygen in the air. The iron oxide in the slag reacts with the graphite or resin on the hot surface of the bricks, and the oxygen corrodes the graphite or carbon binder on the surface of the brick lining. In these two cases, the internal structure of the refractory bricks becomes loose, the strength is reduced, and eventually the refractory brick lining is eroded by molten slag or molten steel. This erosion phenomenon occurs in all parts of the refractory material in the ladle, and is most serious at the slag line.
FeO+C=Fe+CO
O2+2C=2CO
2) Scouring
Scrubbing is the physical wear or scouring of the lining caused by molten steel or slag flowing over the surface of the refractory material. For ladles using eccentric bottom tapping, the molten steel has a greater impact on the molten steel impact area at the bottom of the ladle, the nozzle slide, and the air-permeable bricks above the bottom of the ladle. For ladles treated with LF and CAS, the strong stirring effect of the argon blowing process at the bottom of the ladle intensifies the scouring effect of the molten steel on the local parts of the ladle wall.
3) Spalling
Spalling is caused by stress in the refractory lining caused by rapid cooling and heating. When the stress exceeds the strength of the refractory, cracks will form inside the refractory. As these cracks expand, intersect and penetrate, fragments of the refractory will partially or completely peel off. This phenomenon often occurs on nozzle seat bricks and air permeable seat bricks.
4) Hydration
The ladle working lining is constructed by wet masonry with fireclay, and the permanent lining is knotted with castables. Before and during baking, moisture or water vapor reacts with MgO in the magnesia carbon bricks to hydrate. The hydrated refractory material has poor permeability to steel slag and molten steel, and its physical and chemical properties are weakened, and it will accelerate the erosion of the ladle lining.
MgO+H2O=Mg(OH)2
Through the above analysis of the damage mechanism of the ladle lining, it is not difficult to find that the damage mechanism of the refractory materials in various parts of the ladle working layer is different, so it is necessary to manage the entire process of the ladle lining, from material selection, masonry construction, baking, operation, and detection and maintenance after the problem is found. When the ladle needs to be repaired after a certain number of uses, carefully check the residual thickness of each part of the lining, analyze the damage, and conduct a careful analysis combined with the data during the use of the ladle, so as to understand the damage law of the refractory materials in various parts of the ladle lining.
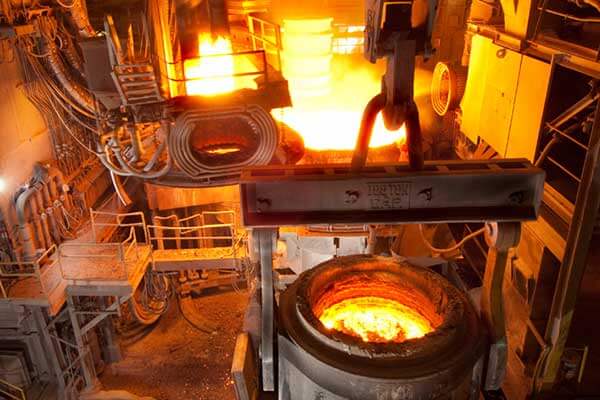
Ladle Furnace