With the continuous improvement of variety and product quality in metallurgical industry, all steel companies are increasing their investment and research on extra-furnace refining. A steel company is equipped with three LF furnaces, one VD furnace refining equipment, and the key to its process is the refining ladle bottom blowing purging plug permeability. Refining ladle bottom blowing principle is through the bottom of the ladle breathable element to the ladle blowing inert gas to stir the steel, in order to promote inclusions floating, uniform steel composition and temperature purposes.
Bottom blowing argon is used to prevent the leakage of steel institutions split external mounted purging plug, since the commissioning of the use of the actual production of refining ladle bottom blowing ladle purging plug but not gas or low flow caused by the inverted package of production accidents, a serious impact on the quality of varieties of steel, production of smooth and production costs. To improve the refining ladle bottom blowing breathable brick blowing rate, need to analyse the impact of bottom blowing purging plug without gas of various factors, and develop corresponding improvement measures to eliminate the occurrence of such accidents.
Analysis of the causes of refining ladle bottom blowing purging plug without outgassing
Through the statistics of 211 cases of ladle bottom blowing without air or low flow caused by the collapse of the ladle accident, the main reasons are shown in Figure 1.
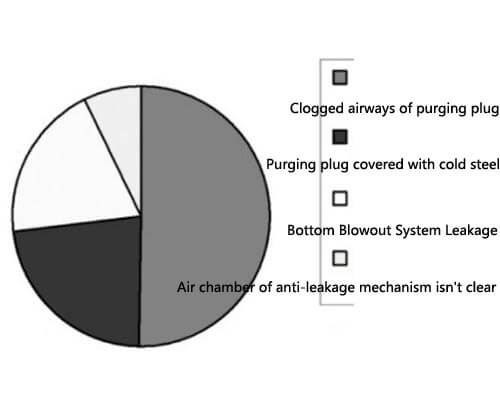
1.Blockage of airways in slit-type purging plug
By analysing the clogged purging plug residue, there are several main factors.
1.1Purging plug slit infiltration
From the residue after use to take down the clamping steel piece, after measuring the length of steel piece in 30 ~ 50mm, the thickness of the existence of two phenomena: one is the clamping steel thickness of the steel piece is more uniform, close to ladle permeable brick slit size of 0.25mm; the second is the clamping steel thickness of the steel piece more than the size of the slit, the thickest place up to 0.4mm. this kind of steel penetration accounted for about 62% of the permeable brick airway blockage. Analysis of its causes:
From the residue after use to take down the clamping steel piece, after measuring the length of steel piece in 30 ~ 50mm, the thickness of the existence of two phenomena: one is the clamping steel thickness of the steel piece is more uniform, close to the purging plug slit size of 0.25mm; the second is the clamping steel thickness of the steel piece more than the size of the slit, the thickest place up to 0.4mm. this kind of steel penetration accounted for about 62% of the purging plug airway blockage. Analysis of its causes:
(1) Ladle purging plug slit parameter design of the gap is too large;.
(2) Argon piping system is not installed exhaust branch, the end of the operation, the purging plug itself will be due to the inverted suction pipe, making the liquid steel back into the breathable brick slit;
(3) The thermal stability of the purging plug is poor, after contact with high-temperature molten steel, its surface is subjected to thermal stress to change the dimensions, and the molten steel is easy to infiltrate.
1.2Cracks in bottom-blown breathable bricks, steel seepage from bricks and airways
Longitudinal analysis from the residue after use, purging plug cracks are divided into longitudinal and transverse two kinds, sometimes alone, sometimes at the same time. Longitudinal cracks caused by steel from the longitudinal cracks infiltrated and extended to the air channel, the formation of longitudinal steel penetration; transverse cracks appear in the purging plug body to the steel surface within 30mm, steel infiltration into the transverse cracks to form a layer of about 0.35mm thick steel sheet. Produce cracks cause:
(1) the thermal stability of the purging plug is not stable before the steel ladle temperature of 800 ~ 900 ℃, converter steel temperature of 1640 ~ 1660 ℃, the purging plug upper due to the temperature difference between the thermal stress, causing cracks and fall off. In addition, the low temperature and high speed of the inert gas so that the purging plug slit area temperature is lower than other parts, so that the purging plug inside a larger temperature difference, resulting in purging plug cracking, transverse break.
(2) non-resistant material reasons for the transverse fracture converter blowing argon switch is set under the furnace, open gas time is not easy to control, resulting in purging plug overtime air blowing; shutdown maintenance, the ladle parking time is too long, subject to the limitations of the baking device, resulting in some ladle baking time is short, the bottom of the package temperature is extremely low. When the steel out of the non-normal purging plug transverse fracture phenomenon.
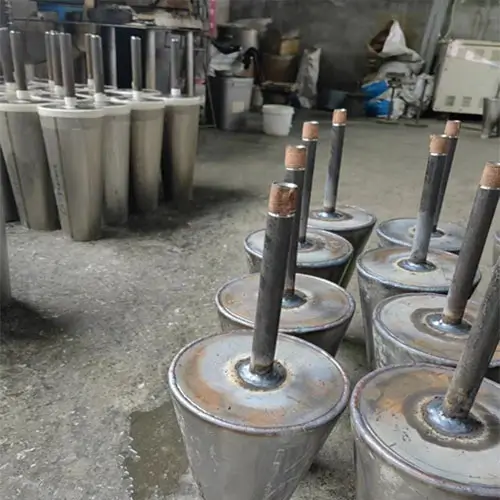
1.3 Steel penetration through permeable bricks clogging the air chamber of the leakage prevention mechanism
Operator’s judgement on the use of gas purging plug error, gas purging plug residual thickness is thin, in the process of blowing argon caused steel penetration, flow into the leakage prevention mechanism will be the mechanism of the gas chamber blockage, interrupt the inflow of gas.
2.Ladle purging plug covered with thick cold steel
2.1 Formation of air-permeable brick pits creates conditions for accumulating cold steel
(1) The bottom blowing seat brick is unstable in resistance to steel scouring, gas impact and slag erosion, and the bottom blowing seat brick flared erosion is serious and accelerates the erosion of ladle permeable bricks. As a result, deeper pits are formed.
(2) hot repair material bonding and anti-washout performance is poor, the use of a few furnaces will be completely detached from the pit repair can not play an effective effect.
2.2 Cold steel accumulation caused by the ladle without bottom blowing argon operation
Individual furnaces in the steel process does not carry out the bottom of the ladle blowing argon operation, in the high temperature of steel and static pressure caused by the new seepage of steel clogging, affecting the refining station in the argon blowing operation. From the inverted package situation tends to have a thin layer of cold steel at the bottom of the ladle.
2.3 Cold steel accumulation caused by steel quality, production rhythm, etc.
Low steel temperature and poor fluidity, production rhythm and accidents caused by individual ladle in the non-blowing argon bit stay too long, ladle baking is not in place, etc. will increase the chances of ladle purging plug surface area of cold steel and affect the bottom of the ladle blowing breathable performance. From the inverted packet situation, there is often a thick layer of cold steel at the bottom of the ladle.
3.Bottom Blowout System Leakage
There are two kinds of phenomena of bottom blowing system leakage, one is very obvious piping system leakage, including quick connector butt, metal hose and pipeline welding points; the second is that the leakage occurs at the outer edge of the upper platen, mainly due to the bolts are not tightened in place; less installation of sealing gaskets; the fire clay applied is too thin, and in the drying process, it will form a large crack space, which makes the gas blowing into the presence of static pressure of the steel water leads to the gas backflow, along the gap from the seat brick and breathable brick between the overflow to the outside.
4.The air chamber of the anti-leakage mechanism is not clear
4.1 Foreign matter in the filter
The foreign matter comes mainly from dust, which reduces the amount of gas passing through.
4.2 Arc sintering at the end of the conduit after permeable bricks
The end of the conduit is sintered after the breathable brick, blocking the inflow of gas. Insulation tube one is poor resistance to high temperature, heat is easy to burn; Second, the material is brittle and easy to rupture. Insulation tube damage after the loss of insulation effect, in the steel refining treatment arc sintering.
4.3 Foreign matter in the tube after the breathable brick core
Blowing argon hose by high temperature baking carbonisation, argon blowing process carbide concentration in the purging plug core after the tube caused by clogging.
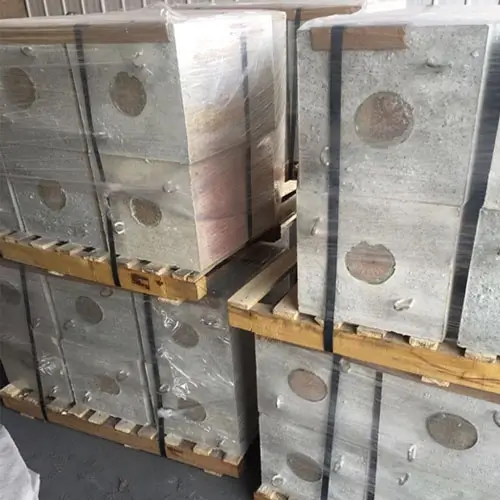