The tamping process of neutral furnace lining is a relatively complicated process, and the knotting process is a very important link, which can affect the service life of the furnace. So, what should we pay attention to during the knotting process to ensure that the service life of the stove is not affected?
- The more basic thing is of course the standardized operation process, but in addition, there are many things to pay attention to during the knotting process of intermediate frequency furnace ramming materials. For example, before tying the knot, ensuring that the power supply and water supply system are complete, it is also necessary to make preparations in advance through the staff of each project. Of course, this also includes that staff are prohibited from bringing any flammable objects to the work site, including mobile phones, keys and other items.
- Adding sand to the intermediate frequency furnace charge is a relatively strict process. For example, the sand must be added in full at one time. Do not add it in batches. Of course, when adding sand, make sure that the sand is spread flat on the bottom of the furnace and cannot be piled up. into a pile, otherwise it will cause the particle size of the sand to separate.
- When knotting the neutral furnace lining material, we must operate it by shaking first and then vibrating. And pay attention to the technique to ensure that you are gentle first and then heavy during the operation. And the rocker should be inserted to the bottom in one go, and every time the rocker is inserted, shake it eight to ten times.
- After beating the furnace bottom, be sure to put the dry pot into the pot stably. Only in this way can the forming be ensured to be relatively standardized, which will generally be a standardized annular triangular ring. Of course, there are many things that require attention during the entire knotting process. And every process cannot be ignored.
There are two methods of knotting the lining of intermediate frequency thermal induction furnace: wet knotting and dry knotting. Both methods can be used for knotting acidic intermediate frequency furnace lining, neutral ramming mass and alkaline furnace lining.
Wet knotting of neutral furnace lining materials refers to knotting by adding water, water glass, brine and other adhesives to the furnace lining knotting materials. Since the knotted material contains a certain amount of moisture, there is less dust during construction and good formability.
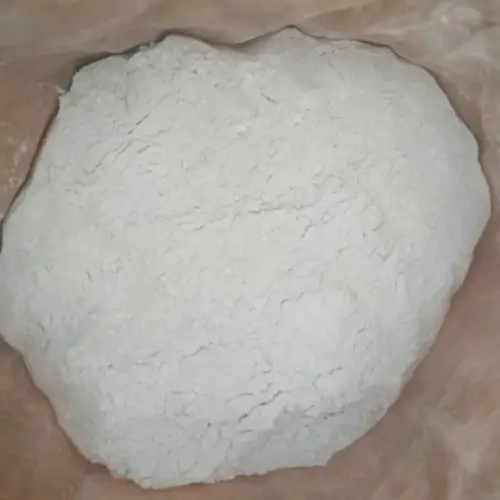
FAQ:
What is neutral lining ramming mass?
Neutral ramming masses are a unique, chemically neutral foundry solution that form joint-less linings. The in-situ spinels synthesise at high temperatures inside the refractory lining, creating a unique 3-layer structure.
What is a ramming mass?
Ramming mass is a pre-blended Dry vibratables refractory made from a selected mix of SILICA GRAINS. This blend of grains along with a binder, BORIC ACID forms the working lining in an Induction furnace used for melting steel.
What is the neutral lining of the induction furnace?
Alumina (Al2O3) is the most fashionable material for producing neutral linings of induction furnaces used in steel industry. This type of lining has very high melting temperature, high strength, high hardness, and relatively high resistance to slag attack.
What is the difference between neutral ramming mass and silica ramming mass?
Neutral ramming mass is neutral and does not chemically react with molten metal in the furnace to avoid metal pollution. The silica ramming mass is an acidic material, which will react when it encounters alkaline substances, so it cannot be used to treat alkaline substances such as iron and steel.
What is the lining material for induction furnace?
Refractory linings used in induction furnace are commonly made of acidic (Silica) or basic (Magnesia) compounds. Choosing the right refractory material for a given melting or holding application is important.
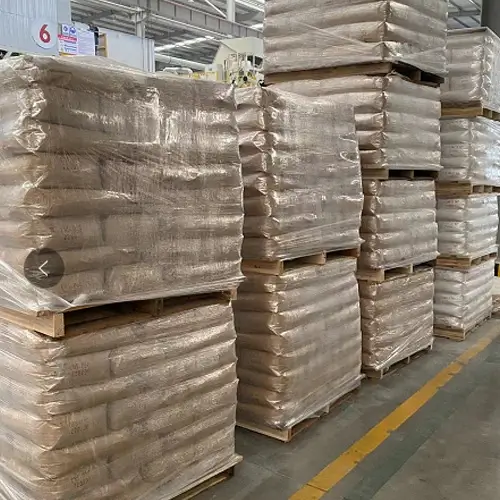