The methods of slag blocking are as follows:
Blocking slag once by slag blocking cap method; Secondary slag removal is blocked by slag ball method, floating plug method, pneumatic slag monoblock stopper method, pneumatic slag blowing method, etc.
(1) Slag cap.
A conical slag cap made of steel plate is blocked outside the tapping hole to block the primary slag when tapping begins.
(2) Slag ball.
The density of the slag ball is between molten steel and slag, and it is put into the furnace near the tap hole near the end of tapping. With the decrease of the liquid level of molten steel, the slag ball sinks to block the tap hole, so as to prevent the slag from entering the ladle. The reasonable density of slag ball is 4.2 ~ 4.59/cm3. The slag retaining ball has a spherical structure, and its center is made of cast iron block, raw iron chip pressing block or small waste steel billet, and its exterior is covered with refractory clay. High alumina refractory concrete or magnesia refractory clay with high alumina refractory concrete or refractory brick powder as admixture can be used. The diameter of the slag ball should be slightly larger than the diameter of the tapping hole to play the role of slag blocking. Slag-blocking balls are usually put into use between 2/3 and 3/4 of the steel output, and the hit rate of slag-blocking is high. The slag is too sticky, which affects the slag blocking effect. The slag viscosity is high, so the slag blocking ball can be put in early to improve the hit rate of slag blocking.
(3) Floating plug.
Floating plug can effectively prevent slag from entering steel flow. The structure of floating plug is composed of monoblock stopper rod and stopper, and its material is the same as that of slag ball, and its density can be the same as or slightly lower than that of slag ball. The upper part of the stopper rod is a steel rod for clamping and positioning, and the lower part is wrapped with refractory material. At the end of tapping, strictly align according to the tapping angle of converter, and insert the stopper rod into the tapping hole by mechanical device. At the end of tapping, the tap hole is sealed by the plug. There is a groove on the stopper, through which the remaining molten steel in the furnace can flow out, and the steel slag is blocked in the furnace. Because floating plug has better slag blocking effect than slag ball, it is widely used at present.
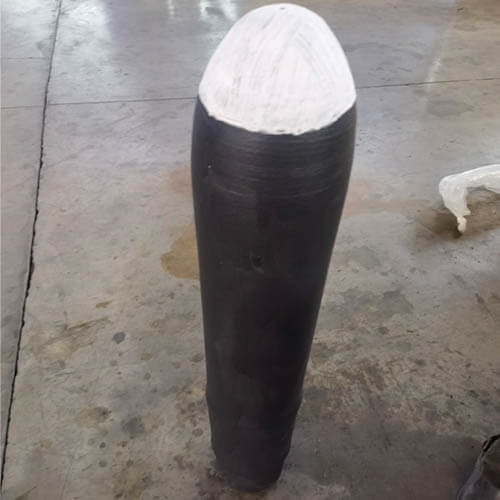
(4) Pneumatic slag stopper.
At the end of tapping, a mechanical device blows air from the outside of the converter into the tapping hole with a slag stopper nozzle to prevent the slag from flowing out. This method has strict requirements on the shape and position of the tapping hole, and requires the nozzle to be aligned with the center line of the tapping hole.
(5) Pneumatic slag blowing method.
It is the most difficult to block the vortex in the late tapping period, and once the vortex is generated, it is easy to mix slag and steel. Therefore, in order to prevent eddy current from occurring in the late tapping period, or even if eddy current occurs, the method of blocking slag on the surface of eddy current molten steel is also the most effective method, that is, pneumatic slag blowing method. High-pressure gas is used to blow away and block the steel slag on the upper steel surface of the tapping hole, so as to achieve the purpose of slag removal. This method can make the thickness of ladle slag layer reach 15 ~ 55 mm.
From the perspective of the development trend of the slag retaining method, foreign countries are gradually developing from the visible slag retaining method to the invisible slag retaining method. Because the slag retaining ball and other tangible slag retaining objects are used to block the slag, the material consumption is high, and the slag blocking effect is not ideal. Many foreign steel mills have adopted the invisible slag blocking method, and equipped with slag detection devices to implement automatic control of slag blocking.
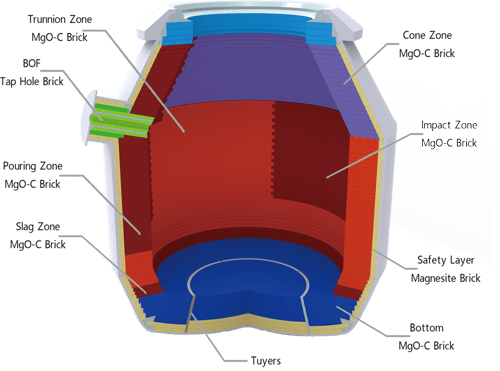