The converter plays the functions of decarburization, dephosphorization, desulfurization, alloying, heating, removal of inclusions, etc. In smelting, the converter does not need external heat and relies on the exothermic reaction of oxidation in the steel. In the converter, the furnace lining, steel outlet, breathable bricks, etc. are composed of refractory materials. Since its development in the 1970s, magnesium-carbon bricks have been widely used because their comprehensive performance is significantly better than that of dolomite-carbon bricks. Magnesia carbon bricks are composed of magnesia aggregate, graphite, antioxidant, binding agent, etc. They have the advantages of high corrosion resistance, spalling resistance, slag resistance and thermal shock resistance. By changing the particle size composition of magnesium sand aggregate and graphite, or changing the amount of antioxidant added, the strength, erosion resistance and oxidation resistance of magnesium carbon bricks can be significantly changed. In actual production, according to the melt loss characteristics of each part of the converter, the composition of magnesium carbon bricks can be fine-tuned to improve the life of the converter and reduce the comprehensive cost.
With the implementation of China’s “double carbon” policy, the carbon consumption of refractories cannot be ignored. Under the new converter smelting technology, the application of refractory materials used in various parts of the converter also faces new challenges. Traditional magnesium-carbon refractories have high carbon content and high thermal conductivity, which will increase energy consumption and refractory erosion. Especially in the smelting of low carbon steel and ultra-low carbon steel, it will increase carbon to the steel, reducing the quality of steel products. Therefore, the decarbonization of magnesium carbonaceous refractories and the innovation of related technology will become a new development direction.
1.Damage mechanism of magnesium carbonaceous refractories in converters
(1)Melting loss
In the smelting cycle of the converter, the following two kinds of melting losses mainly occur in the converter lining. First, the impurities in the magnesium sand component SiO2 and CaO, and magnesium sand reaction to generate low melting point material. Secondly, FeO in the converter slag reacts with MgO in the refractory material to form MgO-FeO solid solution, which lowers the melting point. The above two melting loss phenomena occur simultaneously, resulting in the melting loss of magnesium carbon bricks. The dissolution of magnesium sand has a great influence on the melting loss of magnesium carbon bricks, so the application of high purity raw materials and magnesium sand raw materials with few crystal boundaries to magnesium carbon bricks in the serious area of melting loss and the appropriate increase in the content of MgO in the slag can improve the melting loss condition of magnesium carbon bricks.
(2)Oxidize
Oxidation of magnesium-carbon bricks is unavoidable during smelting, and the carbon in magnesium-carbon bricks (graphite and carbonaceous binding agent) is oxidized by oxidizing gases and oxides in the slag. The oxidation of magnesium-carbon bricks is divided into the direct oxidation of carbon and oxygen and the indirect oxidation of carbon and oxides, with the reaction formulae (1) and (2) and (3), respectively. The oxidation of the converter outlet, furnace mouth, furnace cap and slag line is more obvious, in which the outlet and slag line are mainly oxidized by slag, and the furnace mouth and furnace cap are mainly oxidized by gas. The oxidized magnesium-carbon bricks have a loose structure and reduced strength, and are gradually eroded under the scouring of gas flow and steel.
(3)flake
Spalling is divided into mechanical spalling and thermal shock spalling. When adding scrap, the magnesium carbon bricks on the front large surface will be subjected to both thermal shock impact of cold source scrap and mechanical shock, which will cause the magnesium carbon bricks to partially spall off. Converter due to high gas supply flow, gas supply element (permeable brick) around the refractory material temperature change is intense, the internal liquid stirring force is very strong. The damage mechanism of permeable bricks is mainly thermal shock spalling. Therefore, the magnesium-carbon bricks of the former large surface should reduce the carbon content and improve the strength to resist mechanical spalling. In the sputtering slag furnace protection measures to make the end of the permeable brick to generate “slag – metal permeable mushroom head”, to reduce the bubble backlash and water hammer erosion, to improve the life of the permeable brick.
(4)friction
Wear and tear is the main cause of damage at the bottom of the converter, at the gas supply element and at the steel outlet. For example, when the converter is discharging steel, the outlet is subjected to intermittent thermal shock and has to withstand the scouring of molten steel and part of the slag, resulting in the wear of the refractory aggregate. This part is characterized by the coexistence of steel slag and steel flow, it is difficult to form a stable slag adhesion layer, graphite and magnesium sand due to the flow of steel scouring and fall off. Based on the above problems, high-temperature creep resistance can be improved by adjusting the particle gradation of raw materials to increase the bulk density of magnesium-carbon bricks and adding metal fibers.
2.Current status of magnesium-carbon refractories in converter applications
(1)Converter Lining
Generally speaking, magnesium bricks are used for the permanent layer and magnesium carbon bricks are used for the working layer of the top and bottom re-blowing converter. The permanent layer is magnesium bricks and the working layer is magnesium carbon bricks, which need to be masoned with staggered joints when laying bricks. Metal pallets and permanent layer of bricks to join between the pounding material, magnesium bricks between the loose can be added to the iron reinforcement. The triangular gap between magnesium carbon and magnesium bricks should be <3mm, and the gap should be filled with caulking material. The masonry around the steel outlet and the seat brick adopts dry masonry, and the gap is stuffed with processed bricks. In addition, the corners between the horizontal metal buttresses and the permanent layer of bricks were filled manually with pounding material.
Differences in the working conditions of each part of the converter and the influence of operating factors lead to different damage mechanisms, damage frequency and amount of damage in different parts of the furnace lining, so the comprehensive masonry method is used to categorize the lining of the converter masonry. Comprehensive masonry furnace method refers to according to the converter parts of the refractory material by the difference in damage conditions, masonry performance of different magnesium-carbon brick method. According to different parts of the melt damage characteristics, masonry appropriate carbon content of magnesium carbon bricks, so that the overall refractory materials in the furnace damage balance.
(2)Slag Retention System
The refractory elements used in the slag blocking system of the converter include steel outlet, bowl brick, inner water outlet, slide plate and outer water outlet, except for the slide plate which is of aluminum-carbon zirconium, and the rest of the refractory elements are of magnesium-carbon. For the converter sliding plate slag blocking system, the steel outlet is plugged with high alumina plastic, then the inner water outlet is installed, and finally the sliding plate slag blocker is installed. Chrome corundum fireclay needs to be applied to each connection of the bowl brick, inner water spout, upper slide, lower slide and steel outlet, so that the refractory elements are connected tightly at the interfaces, preventing the steel from flowing into the gaps of the interfaces, as well as reducing the scouring area of the steel.
In the process of blocking slag and steel outlet, the steel outlet and slide plate have to withstand the scouring, abrasion, erosion and oxidation of high-temperature molten steel and steel slag. It is not suitable to use magnesium-carbon bricks with high carbon content for the steel outlet, and the slide plate is made of aluminum-carbon zirconium with excellent resistance to erosion and thermal shock, and the upper slide plate is inlaid with zirconium ring and the lower slide plate is inlaid with zirconium plate.
(3)Maintenance and repair materials for furnace linings
Converter repair material is divided into large surface hot repair material, trunnion and fillet spray repair material, and outlet grouting material, all of which are magnesium carbonate unshaped refractory materials. The hot repair material is made of magnesium sand, with bitumen or phenolic resin as binding agent, and is poured into the converter. Through the shaking furnace operation, using the residual heat of the converter to make the spread to the large surface of the repair material fully sintered, sintering time is generally not less than 10 min. spray patch repair trunnion and rounded corners of the furnace lining bricks by spraying, after repairing the service life of the furnace between 6 to 10. After replacing the new outlet brick, use the spray patching equipment to spray the grout into the gap between the outlet and the seat brick, so that the gap is filled with dense.
Graphite is widely used in magnesium carbon bricks due to its poor wettability with steel slag. However, the graphite content in traditional magnesium carbon bricks is too high, which on the one hand will have a carbonizing effect on steel, and on the other hand will cause a large amount of heat loss. Simply reducing the carbon content of magnesium-carbon bricks will bring the problems of deterioration of oxidation resistance, thermal shock resistance and slag resistance. To address the above problems, researchers have improved the performance of low carbon magnesium-carbon bricks through three aspects: modification of bonding agent, application of high efficiency antioxidant and optimization of raw materials.
3.Development trend of magnesium-carbon refractories for converters
(1)Low carbon magnesia carbon brick
Graphite is widely used in magnesium carbon bricks due to its poor wettability with steel slag. However, the graphite content in traditional magnesium carbon bricks is too high, which on the one hand will have a carbonizing effect on steel, and on the other hand will cause a large amount of heat loss. Simply reducing the carbon content of magnesium-carbon bricks will bring the problems of deterioration of oxidation resistance, thermal shock resistance and slag resistance. To address the above problems, researchers have improved the performance of low carbon magnesium-carbon bricks through three aspects: modification of bonding agent, application of high efficiency antioxidant and optimization of raw materials.
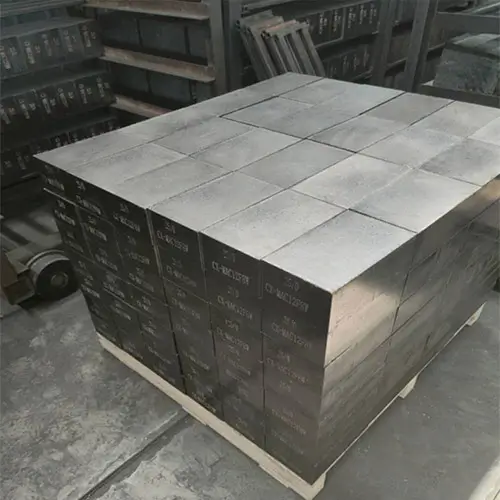
Binding agent modification
A catalyst is introduced into the carbonaceous binding agent to generate carbon nanostructures in situ to improve the oxidation, thermal shock and slag resistance of low carbon magnesium-carbon bricks. The commonly used binding agent is phenolic resin, but it changes into isotropic glassy carbon with high brittleness after carbonization, and at the same time, many gaseous products are released during the transformation of organic groups, which affects the thermal shock resistance and high-temperature mechanical properties of low-carbon magnesium-carbon bricks.
Researchers have found that the addition of suitable catalysts to phenolic resins can transform amorphous carbon to the crystalline state.Yage Li et al. investigated the effect of Fe, Co, and Ni nitrate catalysts on the in-situ formation of carbon nanotubes (CNTs) from the pyrolysis of phenolic resins. The results showed that Fe nitrate was the best catalyst for the formation of CNTs. The high-temperature flexural strength of the samples was higher than that of catalyst-free samples prepared under the same conditions. In the presence of the catalyst, a large number of carbon nanotubes and carbon onions were generated to promote the in situ formation of ceramic phase magnesium whiskers and spinel whiskers/particles. The binding agent modification optimized the microstructure of the samples, generated graphitized carbon and ceramic phases, and improved the oxidation, slag, and thermal shock resistance of the low-carbon magnesium-carbon bricks.
Application of efficient antioxidants
Oxidation is the main factor affecting the service life of low carbon magnesium carbon refractories, adding antioxidants is a common and effective way to inhibit carbon oxidation. The role of antioxidants is to give priority to the carbon is oxidized or the generation of ceramic phase to fill the pores to prevent the oxygen medium into the refractory. Low carbon magnesium carbon refractories in the antioxidant is metal powder, carbide and boride.
Among them, Al powder and Si powder are widely used in low carbon magnesium carbon refractories, but Al powder is easy to hydrate causing volume expansion and affecting the densification. Based on this problem, the researchers solved the shortcomings of Al powder by synthesizing AlB2-Al-Al2O3 composite powder through combustion synthesis method. Silica powder as an antioxidant can provide the bonding strength of magnesium-carbon bricks and generate SiC to fill the voids in magnesium-carbon bricks, and SiC helps to form a dense isolation layer at the oxidation interface to protect graphite from oxidation. However, SiC will be oxidized to form SiO2, and MgO to form spinel crystal type Mg2SiO4 and accompanied by volume expansion, appropriate volume expansion will improve the strength and density of magnesium-carbon refractories. Other scholars have studied the way of B4C+Si composite adding antioxidant, using B4C to generate a low melting point compound B2O3 to fill the pores, inhibit the diffusion of oxygen medium through the pores, to avoid graphite oxidation.
Raw material optimization
The main raw materials of low-carbon magnesium-carbon refractories include magnesium sand and graphite, and the contact area between graphite and magnesium sand is greatly reduced after the graphite content is reduced, which leads to the uneven dispersion of graphite in the matrix, and reduces the material’s resistance to thermal shock and slag resistance. Some studies have been conducted to regulate the porosity in low materials through measures such as particle gradation and carbon source. The particle gradation in low carbon magnesium carbon bricks was calculated by Andreassen’s formula according to the theory of continuous closest packing of particles. It was found that when the critical particle size of 3mm, the appropriate increase in the proportion of coarse particles of low carbon magnesium carbon bricks, so that the individual coarse particles and matrix bonding area increases, the fracture surface energy increases, and improve the thermal shock resistance.
A Japanese refractory company researchers found that it is not the magnesium carbon brick high temperature mechanical properties, the better, the stronger the resistance to damage. Through the two methods of magnesium-carbon brick matrix enhancement or carbon bonding enhancement, developed and applied to different parts of the converter. Ultrafine graphite and graphite with different grain sizes [29] can be well filled in the voids of low-carbon magnesium-carbon materials in order to make the material matrix dense. The introduction of carbonaceous micronized powders and the use of a mixture of amorphous graphite + scaled graphite in the matrix of low-carbon magnesium-carbon bricks were used to reduce the porosity of the specimens and to improve the mechanical properties. The oxidation resistance of amorphous graphite is better than that of squamous graphite, and the mixture of the two can improve the oxidation resistance of low carbon magnesium carbon bricks. This low carbon magnesium carbon brick is applied in the field, and the average erosion rate of the test pack is 1.08mm/furnace lower than that of the normal pack, which has a good application prospect.
Furnace Lining Maintenance
The repair of large surface of the converter using magnesium and carbon repair material, repair will produce a lot of black smoke and repair time is longer, which is not conducive to the site environment and the efficiency of the steel mill. Based on this problem, some researchers have developed an environmentally friendly fast sintering surface repair material by using mid-range magnesium sand, electrofused magnesium sand as the main raw material and introducing aluminum powder as a burnout aid and modified bitumen binding agent. The use of a small amount of liquid wetting agent and flow aids, its environmental protection, sintering time is short, the average life of more than 34 furnaces.
The converter trunnion and furnace bottom are subject to mechanical stress and slag erosion, which require frequent spray patching of these two parts. In order to improve the existing magnesium and carbon patching material is not resistant to the shortcomings of erosion and scouring, the development of magnesium sand as raw material, carbon and asphalt as the binding agent of spray patching material. After the field application, the service life of the original spray patching material has been increased by 30%.
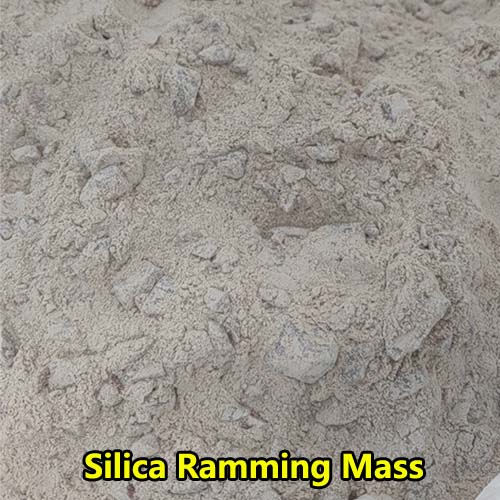
4.Summarize
(1) Comprehensive masonry for converter lining and application of magnesium-carbon bricks with different properties according to the melt loss condition of each part can improve the life and production safety of converter and achieve the best comprehensive economic benefits.
(2)Through the measures of modification of binding agent, optimization of raw materials and application of high efficient antioxidant, we can develop high performance materials such as low carbon magnesium-carbon bricks, high-strength magnesium-carbon bricks and oxidation-resistant magnesium-carbon bricks.
(3) From the perspective of environmental protection, the frequency of converter sputtering slag guarding should be reduced, and fast and environmentally friendly converter repair materials should be developed and applied to solve the problems of long sintering time and black smoke generation.