1.Bulk density
Bulk density of refractory material is the mass per unit volume, which is usually used to describe the density and weight characteristics of the material. Bulk density is one of the important physical and chemical indexes of refractory bricks, which can directly affect the compactness of refractory bricks, as well as thermal insulation and heat conduction properties. For a refractory brick of the same size, the higher the bulk density, the heavier the weight of the brick, which means that it is denser, has a higher compressive strength and is more resistant to the intrusion of external slag. There is a certain relationship between the bulk density and weight of refractory bricks, which can be calculated by the formula “Weight = Volume × Bulk Density”, in which the weight indicates the weight of the refractory brick, the unit is kg or grams; the volume indicates the volume of the refractory brick, the unit is cubic meters or cubic centimeters; Bulk Density indicates the bulk density of the refractory brick, the unit is kg/m3 or g/cm3.
Lightweight refractory bricks are heat-insulating refractory bricks with a wide range of bulk densities, from 0.3-1.2g/cm3, depending on the refractory raw materials used and the production process. For example, the bulk density of lightweight clay bricks is 0.5-1.3g/cm3, while the bulk density of high-alumina poly-light bricks is generally 0.6-1.0g/cm3.These data indicate that lightweight refractory bricks are characterized by light weight, low thermal conductivity, low bulk density, high porosity, and better thermal insulation.
In contrast, the bulk density of dense refractory bricks is higher, such as dense clay refractory bricks with a bulk density of generally 2.05-2.30g/cm3, and high alumina bricks with a bulk density of generally 2.3-2.6g/cm3.These data reflect that dense refractory bricks have higher compressive strength and slag resistance, and can better resist physical and chemical erosion in high-temperature environments.
In summary, the bulk density of refractory bricks is determined according to their specific use and required performance, and different bulk densities are suitable for different industrial environments and application scenarios. Lightweight refractory bricks are suitable for applications requiring good thermal insulation properties, while dense refractory bricks are suitable for high temperature environments requiring high compressive strength and slag resistance.
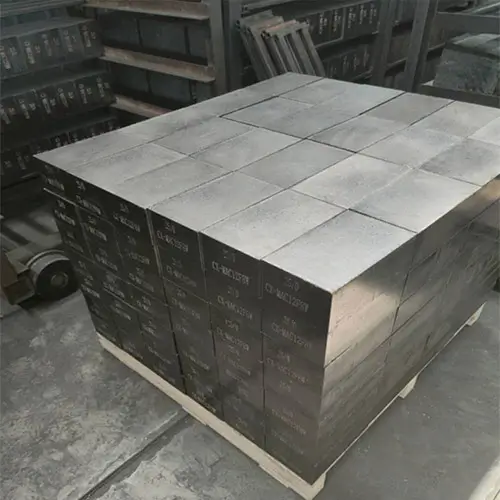
2.Stomatal percentage
The apparent porosity of a refractory material is the percentage of the volume of open pores in a refractory product to the total volume of the product, also known as apparent porosity.
Refractory porosity is an important quality indicator, which not only reflects the degree of densification of the refractory material, but also characterizes the manufacturing process of particle size composition, molding and firing is reasonable. The existence of porosity has a significant impact on the mechanical properties of refractory materials, so it is extremely important to reasonably control the number, morphology and distribution of porosity in refractory materials. The size of porosity affects almost all the properties of refractory products, especially the strength, thermal conductivity, slag resistance and thermal shock resistance.
The existence of pores in the refractory material is mainly in the form of open pores and closed pores. Open pores are pores that communicate with the outside world and can be filled by fluids, while closed pores are pores that are closed in the product and do not communicate with the outside world. Refractory product porosity is usually expressed in terms of apparent porosity, that is, the ratio of the volume of open pores to the total volume of the product. This ratio can be as small as near zero or as large as 80%, depending on the type of refractory product and the application scenario. In general, dense products have apparent porosity between 10% and 28%, while thermal insulations have true porosity greater than 45%. Products with less than 15% porosity are called low porosity products.
3.Compressive strength, flexural strength
The compressive strength of refractory materials refers to the ability of the material to resist damage under the action of compressive force, usually in megapascals (MPa). This strength index reflects the structural stability of refractory materials when subjected to pressure, the higher the compressive strength, indicating that the material is able to withstand greater external forces without fracture or deformation, thus maintaining its structural and functional integrity. In practical application, according to different use environment and requirements, it is very important to choose refractory materials with appropriate compressive strength. The compressive strength of refractory materials is one of the important indicators of their performance, and together with the flexural strength, it jointly determines the suitability and durability of refractory materials under specific conditions.
Flexural strength
The flexural strength of refractory materials is the stress per unit of sectional area subjected to the action of bending moment until it breaks. This index is one of the important parameters for assessing the performance of refractory materials, which is directly related to the reliability and durability of the material in actual use. Flexural strength, also known as flexural strength or modulus of rupture, is a measure of the ability of the material to resist damage when subjected to bending loads. For refractory materials, this performance indicator is particularly important because it relates to the long-term stable operation and safety of high-temperature equipment.
The flexural strength of refractory materials is affected by a variety of factors, including material composition, microstructure, production process and temperature conditions. The flexural strength of refractory materials can be improved by optimizing the formulation, controlling the microstructure, appropriate heat treatment and mechanical reinforcement. In addition, flexural strength is tested by standard mechanical test methods, such as three-point bending test or four-point bending test, to ensure that the refractory material can withstand the challenges of high temperature and stress in real-world applications, thus safeguarding the normal operation and service life of industrial equipment.
4.Load softening temperature
The load softening temperature of refractory material is an important parameter to measure the performance of refractory material in high temperature resistance under a certain load, which is directly related to the durability and reliability of refractory material in the actual high temperature industrial application.
The load softening temperature of refractory material, also known as load softening point or load deformation temperature, refers to the temperature at which the refractory material starts to change from solid state to plastic state under a certain load. This temperature point is the critical point where the refractory material begins to lose its original mechanical strength and structural integrity. The load softening temperature is an important basis for predicting the service life of refractory materials in high temperature environments, and it is also a key indicator for selecting suitable refractory materials when designing furnace lining structures. In addition, it is also an important quality indicator for assessing the performance of refractory materials, indicating the ability of refractory materials to resist both high temperature and loading at the same time, and to a certain extent, indicating the structural strength of products under similar conditions of use.
The test of load softening temperature usually adopts load softening point tester, by applying a certain compression load to the material in a controlled atmosphere and gradually increasing the temperature until the material softens or deforms permanently. Factors affecting the load softening temperature of refractory materials include chemical composition, microstructure, production process and ambient atmosphere. Strategies to improve the load softening temperature include the selection of raw materials, precise control of the microstructure, the use of composite technology and the use of additives. These strategies are of great significance to optimize the load softening temperature of refractories and play an important role in the stable development of high temperature industry.
5.Heating permanent line change
The heating permanent line change of refractory material refers to the percentage of the residual shrinkage or expansion of the length of the refractory material to the original length when it is heated to a specified temperature at high temperature and held for a certain period of time, and then cooled to room temperature.
This index is one of the important parameters for evaluating the quality of refractory materials, especially in high temperature environments, the volumetric stability of refractory materials is essential to ensure their safety and reliability in practical applications. The determination of the rate of change of the permanent line of heating usually involves heating a refractory specimen to a specific temperature and holding it there for a certain period of time, then cooling it down to room temperature and measuring the change in its length in comparison with the original length as a way of evaluating the volumetric stability of the material. Positive values indicate expansion, known as reburn line expansion, and negative values indicate contraction, known as reburn line shrinkage. Such changes may be due to physical and chemical changes in the material at elevated temperatures that persist after the material has cooled to room temperature, and are therefore referred to as “permanent” or “residual” line changes.
The heated permanent line change of a refractory material is essential to ensure its performance in high-temperature environments. In the metallurgical industry, for example, refractory materials are subjected to extremely high temperatures and pressures, and if the material’s thermal permanent line variation is too great, it may lead to structural instability in the furnace and may even cause safety accidents. Therefore, for different types of refractory materials, such as refractory castables and refractory bricks, the determination and control of the rate of change of the heating permanent line plays a key role in the selection and use of the materials.
6.Coefficient of thermal expansion
The coefficient of thermal expansion of a refractory material is a physical quantity that measures the change in length or volume of a refractory material during heating, and is usually expressed in terms of the coefficient of linear expansion or the coefficient of bulk expansion.
The thermal expansion of a refractory material is the physical property that its volume or length increases with increasing temperature. This property is an important parameter in kiln design because it directly affects the size of the reserved expansion joints and thus the performance and safety of the kiln. The coefficient of thermal expansion can be measured and calculated by different methods, including the coefficient of linear expansion and the coefficient of bulk expansion, as well as the percentage of linear expansion and the percentage of bulk expansion. The coefficient of linear expansion is the relative rate of change in the length or volume of a specimen for every 1°C increase in temperature during the interval in which the refractory is heated from room temperature to the test temperature. The coefficient of bulk expansion, on the other hand, is the rate of change in volume.
The thermal expansion of a refractory material is affected by a variety of factors, including its chemical composition, mineral composition and microstructure. For example, the thermal expansion of a material composed of crystals is related to the nature and strength of the chemical bonds in the crystals. Generally speaking, in the process of developing from covalent bonding to ionic bonding, the ionic bonding increases and so does its expansion. Crystals with larger bond strengths and non-isotropic crystals have lower thermal expansion in the direction of the bond strength. In addition, the thermal expansivity of refractories varies with the temperature interval.
In practical applications, the coefficient of thermal expansion of refractory materials is a key index, which not only relates to the use performance of the material, but also affects the design and safety of related equipment and structures. Therefore, accurate determination and evaluation of the coefficient of thermal expansion of refractory materials is essential to ensure the safety and efficiency of high-temperature industrial applications.
7.Thermal shock resistance
Thermal shock resistance of refractory materials refers to the ability of a material to maintain its integrity and functionality when subjected to sharp temperature changes. This property is also known as thermal shock resistance, thermal shock stability, resistance to rapid changes in temperature, resistance to rapid cold and heat or thermal stability. Refractory materials in the process of use, often subject to rapid changes in ambient temperature effect, so its thermal shock resistance is its mechanical properties and thermal properties in the temperature change conditions of the integrated performance. This performance is crucial for the long-term stable use of the material, because it is directly related to the material in the use of the process can resist the thermal stress caused by temperature changes, to avoid cracking, spalling and other damage phenomena.
The thermal shock resistance of refractory materials is affected by a variety of factors, including the mechanical strength of the material, modulus of elasticity, coefficient of thermal expansion, thermal conductivity, specific heat capacity, bulk density, structural homogeneity and surface heat transfer coefficient. In addition, for products, shape and thickness also affect their thermal shock resistance. Improving the thermal shock resistance of refractories has always been one of the goals pursued by refractory scientists and technicians, because it is important to ensure the safe use of the material and prolong its service life.
In practice, the thermal shock resistance of refractory materials is evaluated by a series of test methods, such as the water quenching and cooling method for straight bricks, to ensure that the materials can maintain good performance under actual use conditions. These tests simulate the rapid changes in temperature that may be encountered by the material in actual use, and the thermal shock resistance is assessed by observing the material’s performance under these extreme conditions.
8.Creep
Creep of refractory material refers to the refractory material at high temperature, when the refractory material is subjected to stress lower than its ultimate strength, the material will produce plastic deformation, and this deformation will increase with the extension of time, and may even lead to material destruction.
This phenomenon is known as creep. Creep is an important physical phenomenon of refractory materials under specific conditions, which is affected by temperature, stress, time and material structure. Specifically:
Temperature and stress: the higher the temperature at which the refractory material is located, the greater the stress it is subjected to, and the longer the time, the greater the creep rate. This is because under the action of high temperature and stress, the crystal defects within the material, grain boundary slip, the bonding state between the grains and other factors will affect the degree of creep.
Time: creep is a process over time, deformation increases with time. Creep process can be divided into deceleration, constant velocity and acceleration of three stages, each stage reflects the balance of the material’s internal physicochemical changes and external stress effects.
Material structure: The creep of refractory materials is not only affected by the crystal structure, but also by the influence of pores or cracks in the material. The presence of pores or cracks directly affects the creep behavior of the material because they can act as points of stress concentration and promote plastic deformation of the material.
In addition, the creep behavior of refractory materials is crucial for assessing their durability and safety in practical applications. For example, the creep properties of refractory materials used in high-temperature industrial furnaces or kilns are directly related to the service life and safety of the equipment. Therefore, the study and improvement of the creep properties of refractory materials is an important direction in materials science research.
9.Fire resistance
The refractoriness of a refractory material is the temperature at which a material reaches a specific degree of softening under the action of high temperature, and characterizes the resistance of the material to the action of high temperature.
Refractoriness, also known as fusibility, is a technical indicator used to characterize the performance of an object to resist high temperatures without melting. It is not a physical constant of the material, but is determined by the chemical composition of the material, the dispersion, the proportion of the liquid phase in it and the viscosity of the liquid phase. Refractoriness is determined by making the test material into a truncated triangular cone of a specified size, heating it at a certain rate, and observing its gradual bending down due to its own weight to the temperature at which the tip comes into contact with the chassis, so as to determine the refractoriness of the test material. Refractory materials refers to the refractoriness of not less than 1580 ° C of a class of inorganic non-metallic materials, such materials because of their physical and chemical properties allow the use of high-temperature environments, and is widely used in metallurgy, chemical, petroleum, machinery manufacturing, silicate, power and other industrial fields, of which the largest amount of metallurgical industry, accounting for 50% to 60% of the total output. To summarize, the refractoriness of refractories is an important performance index, which is directly related to the performance and safety of the materials used in high temperature environment.
10.Abrasion resistance
The abrasion resistance of a refractory material is its ability to resist friction and abrasion (grinding, rubbing, impact, etc.) of hard materials or gases (containing solid materials), and this ability can be used to predict the refractory’s adaptability to abrasive and scouring environments.
Abrasion resistance is usually assessed by measuring the loss of volume or mass of the material after a certain grinding condition and grinding time. The abrasion resistance of a refractory material depends not only on its mineral composition, organizational structure, and the firmness of the material’s particle bond, but is also related to its own density and strength. Specifically, materials with high room temperature compressive strength, low porosity, dense and uniform organizational structure, and good sintering usually have good wear resistance.
According to the strength of the wear resistance of refractory materials, they can be divided into different categories. For example, silicon carbide-based refractories have the strongest abrasion resistance, while alkaline refractories, siliceous and clay-based refractories have relatively poor abrasion resistance. In addition, high-alumina and corundum refractories have intermediate wear resistance, while silicon nitride-bonded silicon carbide materials have better wear resistance than clay-bonded silicon carbide materials, mainly due to their higher hardness and strength.
The wear resistance of a refractory material is critical to its performance in a given usage environment, especially in applications that require resistance to friction, abrasion and impact. For example, the wear resistance of refractories is particularly important in the interior walls of circulating fluidized bed boilers, cyclone walls, pulverized coal piping and coal injection tubes in power plants. Refractories in these areas need to be able to resist friction, abrasion and impact from solid materials to ensure the long-term stable operation of the equipment.
11.Resistance to erosion
Erosion resistance of refractory materials refers to the resistance of refractory materials to the erosion of slag at high temperatures. This resistance is mainly reflected in the refractory material can resist the chemical action of the external medium and mechanical abrasion, so as to protect the internal structure from damage and prolong the service life.
Refractory material erosion resistance is a measure of its ability to resist various erosion media erosion and erosion at high temperatures, these erosion media including slag, molten metal, glass melt, acid and alkali, electrolyte liquid and various gaseous substances. Refractory material erosion resistance is affected by a variety of factors, including its chemical, mineral composition, organizational structure, porosity, and the interaction with the erosion medium.
In addition, the nature of the erosion medium, the conditions of use (e.g. temperature, pressure) and the interaction between the erosion medium and the refractory material under the conditions of use are also important factors affecting the erosion resistance. Therefore, in order to improve the service life of refractory materials, the selection of materials needs to take into full account the main harmful components in the kiln charge and the nature of the material, and select the appropriate nature of the refractory material to ensure that it can effectively resist erosion and maintain the integrity and stability of the kiln lining.
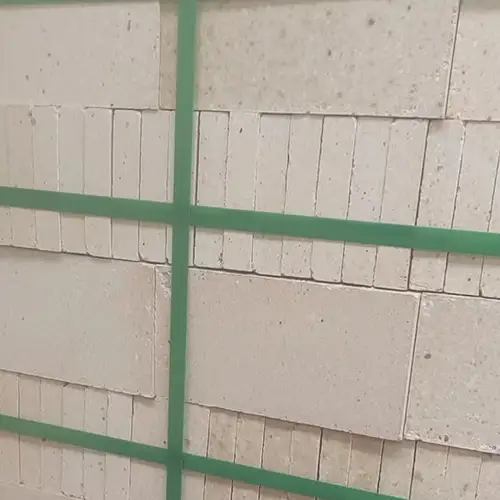