As the key functional refractory material for billet continuous casting, the sizing nozzle plays a role in controlling the flow of molten steel and determines the casting speed of the billet in continuous casting. It is a necessary condition to ensure the normal operation of continuous casting, which is called continuous casting function. refractory material. In addition to the sizing nozzle not being able to burst, clog or fall off during pouring, it is also required that its diameter expansion speed cannot be too fast to meet the requirements of long-term casting.In order to achieve cost savings, the ideal use state of the three types of tundish refractory materials with different functions is to achieve simultaneous damage. However, with the application of the fourth-generation dry vibrating material/paint working lining of the tundish, its service life has been greatly improved. The maximum can exceed 60 hours. In comparison, the life of the sizing nozzle cannot match this, which is the current bottleneck that restricts the improvement of the overall life of the continuous casting tundish.At present, the production process of domestic billet continuous casting tundish sizing nozzle is generally as follows: PSZ particles are used as 10 aggregates, monoclinic zirconia fine powder is added with stabilizers such as magnesium oxide or calcium oxide as the matrix, and then a small amount of Binders and additives are mixed and granulated before dry pressing. The firing temperature is generally between 1650°C and 1760°C.
The production process of the sizing nozzle plays a vital role in its performance. The particle size distribution of raw materials, mixing time, molding pressure, drying method and firing system and other process parameters will affect the performance of the nozzle. By controlling production process factors such as granulation, molding, and firing, the service life of the sizing nozzle can be improved.
According to the structure, the sizing nozzle can be divided into three categories: homogeneous sizing nozzle, direct composite sizing nozzle and inlaid sizing nozzle.
1.Homogeneous sizing nozzle
It is mainly made by adding zirconia to zircon or zircon in a certain proportion and directly mixing it, then forming, drying and sintering (sintering temperature is 1620-1650°C). Containing ZrO2 is 60-90%. It is characterized by good integrity, relatively uniform composition, performance and structure, high strength, corrosion resistance, and good usability, but the cost is high and the service life is relatively short.
2.Direct compound sizing nozzle
In order to reduce production costs, ordinary zirconium sizing nozzles can be made into direct compound type. The inner layer and the outer layer of this sizing nozzle are formed with different materials, the body of the nozzle is made of zircon, and the inner hole (working surface) of the sizing end of the nozzle is made of zirconite and zirconia. The zirconia content of the composite part is 72%-78%. The main body and composite parts are formed at the same time and fired at one time. The firing temperature is 1620-1650℃. The cost of this type of nozzle is much lower than that of a fully homogeneous sizing nozzle. Since the nozzle body and the composite part are molded and fired at the same time, the composite part will not fall off during use. However, since zirconia undergoes phase change and volume change at 1100-1250°C, it is easy to cause the nozzle to burst during use. Therefore, stable zirconia must be used in the production of this nozzle and the content should not be too high. Since the thermal expansion coefficients of stabilized zirconia and zircon are still inconsistent, the nozzle may also crack during use. Its advantages are good nozzle integrity, no bonding seam, high strength, high corrosion resistance, safe and reliable use, and low price; the disadvantage is that it is difficult to manufacture, and it is necessary to solve the problem of inconsistent thermal expansion coefficients of the two materials.
3.Inlaid fixed diameter nozzle
This calibrated nozzle is divided into two parts: the nozzle seat brick and the nozzle core during production. After being made, it is inlaid with fire clay and combined. The seat bricks are made of high-aluminum material and only serve to fix and support the inner core. Their functional requirements are not high. Because the inner core plays a key role in flow control, zirconia raw materials are generally used. The specific composition and production process can be adjusted according to different requirements. At present, its production is mainly made of raw materials with high zirconia content (ZrO2>90%) It is then fired at high temperatures to achieve longevity. The mosaic sizing nozzle solves the cracking problem caused by the thermal expansion mismatch of the inner and outer layers of the composite nozzle. The thermal stability is better than that of the direct compound sizing nozzle, and the cost is lower. The life can be adjusted according to the content of ZrO2 in the inner core. Very extensive.

According to the particle size of raw materials used in the production of sizing nozzles, it can be divided into three types: coarse particle type, fine particle type and pottery type sizing nozzle.
1.Coarse zirconia sizing nozzle
The particles of this type of sizing nozzle are relatively coarse (up to 2mm), the fired products have small shrinkage, good thermal shock stability, and rarely explode during use. However, this type of sizing nozzle has low pressure resistance and high apparent porosity, which makes it have poor corrosion resistance and erosion resistance during use and has a short service life.
2.Fine particle zirconia sizing nozzle
The raw material particle size of this sizing nozzle is all <50pm, and the fired product has a uniform structure, low apparent porosity, high compressive strength, good erosion resistance and corrosion resistance. However, compared with the thermal shock stability of coarse-grained products, explosion may occur at the moment of pouring and cause abnormal stoppage of pouring.
3.Ceramic type zirconia sizing nozzle
The particle size of raw materials used in this sizing nozzle is less than 5pm, and the fired products have extremely low apparent porosity, high compressive strength and long service life, which makes it unnecessary to frequently change tundishes during the continuous casting process, reducing downtime (preparation) time and loss , Improve the efficiency of the casting machine. However, the thermal shock stability of ceramic products is poor, and the nozzle will burst if used improperly. Therefore, when producing and using ceramic zirconia sizing nozzles, measures must be taken to reduce the heat received when the nozzle is opened and poured stress.
Wanhao is a manufacturer who is specialized in designing various kinds of furnace and making refractory products for electric furnace, ladle, tundish, blast furnace, AOD furnace, IF furnace, etc.
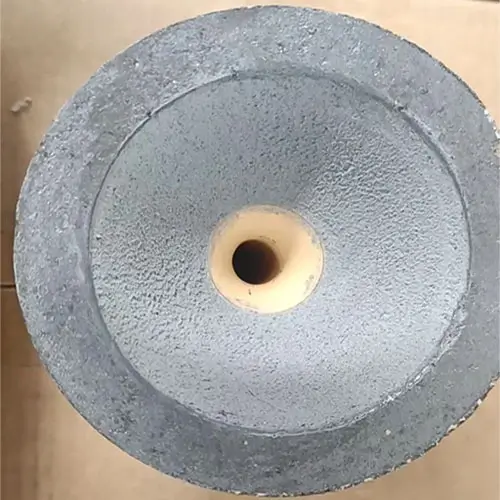