1. Strictly control the slag from the big bag
The main sources of slag components in the casting area of the tundish are ladle refining slag, tundish covering agent and molten steel inclusions floating up into the slag layer. Among them, the low silicon aluminum killed steel refining slag, which is more severely corroded by the stopper rod, is a high basicity refining slag system, and the CaO content in the slag is controlled at 55%-65%. The large ladle slag of each furnace will form a refined slag enrichment in the injection point area of the tundish. During the subcontracting process and when the pouring steel stream impacts the slag surface of the injection point area, it will cause the refined slag to enter the casting area and cause erosion of the stopper.
Therefore, it is necessary to strictly control the slagging of the big ladle, and use the automatic control of the slag detection to avoid a large amount of slagging at the end of pouring. At the same time, the tundish slagging operation should be adopted. When the large ladle is continuously pouring 5 to 7 furnaces of molten steel, the tundish level slagging operation should be carried out to control the thickness of the slag layer in the injection point area.
2. Control the superheat of the package
The liquidus line of the molten steel of XGM6-1 steel grade is 1535℃, and the superheat is controlled at 25~45℃. From the actual production process, when the average superheat of the tundish reaches 45℃ (the temperature of the tundish is 1580℃), all slag lines appear erosion off the situation. The average superheat of the tundish is reduced by 15℃, and the actual control average tundish temperature is reduced to about 1560~1565℃. The erosion of the slag line has been significantly improved, and the erosion rate of the monoblock stopper slag line can be stably controlled within 20%.
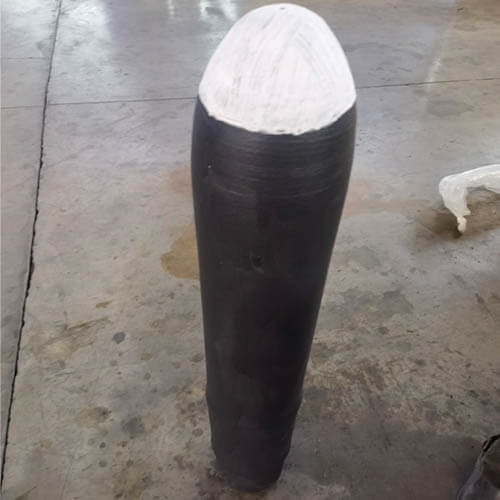
3. Optimizing the composition of the covering agent for tundish molten steel
In view of the reaction situation between the tundish slag and the stopper slag line, it is impossible to completely avoid the problem of refined slag entering the casting area and high superheat of the tundish in the actual production process. Therefore, the composition of the covering agent for the tundish molten steel is optimized for different steel grades. The temperature condition of the package increases the MgO content in the covering agent, and forms the Mg-Ca-Al-Si multi-element compound in the slag layer of the middle cladding. The melting point is above 1600℃. A protective layer is formed at the slag line of the stopper to slow down the damage of the slag. The rod body is resistant to corrosion.
The control of the MgO content in the covering agent needs to be adjusted according to the actual control range of the molten steel ladle. When the MgO content exceeds 15%, the melting point of the tundish slag will increase significantly. The slag layer in the ladle pouring area is crusted, which affects the normal stopper control.
By optimizing the composition of the tundish covering agent, a coating layer of high-melting compound mainly composed of MgO is formed at the slag line of the monoblock stopper rod, which prevents the slag-steel interface reaction from corroding the refractory material at the slag line and effectively improves the service life of the stopper.
