The ladle slag line is the part where the molten steel is in direct contact with the air. At present, most of the ladle slag line masonry uses magnesia carbon bricks. Due to the temperature difference and the existence of oxygen-rich environment, the erosion rate of this part is significantly faster than other parts. In addition, the tipping and slag discharge of the molten steel during operation cause great damage to the slag line. Therefore, the ladle slag line is one of the parts with the highest maintenance frequency. The life of the ladle slag line is mainly affected and restricted by three aspects: external environment, refractory quality and masonry method.
1.External Environment
The ladle is a device for receiving molten steel and performing pouring operations. The temperature of the molten steel is often around 1500℃. When the slag line of the ladle comes into contact with the air at this temperature, a strong oxidation reaction will occur. In addition, the temperature difference between the contact surface of the molten steel and the air also has a very severe impact on the slag line of the ladle. The large temperature difference will severely test the thermal stability of the slag line of the ladle[20]. During the frequent receiving and pouring operations, the refractory will produce a certain degree of cracking. Therefore, in the external environment, oxidation under high temperature has a great impact on the erosion of the slag line. At the same time, the huge temperature change puts high demands on the thermal stability of the refractory. Under the interaction of melting loss and cracking of the refractory, the slag line of the ladle is easily damaged, and then the phenomenon of steel seepage occurs.
LF refining slag can easily cause oxidation and decarburization of magnesia carbon bricks. LF slag has relatively low viscosity at high temperatures, has strong penetration ability in the decarburization layer, and has high solubility for magnesium oxide. At the same time, molten slag easily penetrates into the decarburization layer. Magnesia particles are dissociated at the grain boundaries of periclase, as shown in Figure 1 (SA in the picture is the slag; TA is the intersection of the three pieces). Therefore, the service life of the LF slag line magnesia carbon bricks is relatively low. Shen Pingping systematically studied the damage mechanism of ladle magnesia carbon bricks during the LF refining process, showing that smaller MgO grain aggregates are easily eroded by high-temperature slag, and after erosion, the slag will continue to penetrate along the periclase grain boundaries. MgO aggregate inside, eventually causing cleavage of periclase aggregate.
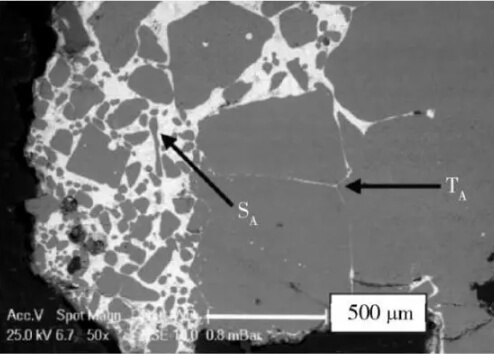
2.Refractory quality
At present, the ladle slag line is mainly built with magnesia carbon bricks. Whether it is traditional magnesia carbon bricks or low-carbon magnesia carbon bricks currently used in large quantities, they mainly use flake graphite as their carbon source. Flake graphite is generally selected from -197, -196, etc., that is, the particle size is greater than 100 mesh, the purity is higher than 97% or 96% (mass fraction), and the binder is a thermosetting phenolic resin. During the carbonization reaction, the self-chain segments undergo cross-linking reactions to form a network structure that can form a mechanical interlocking force between magnesia sand particles and graphite. Graphite, as the main raw material for the production of magnesia carbon bricks, mainly benefits from its excellent physical properties: ① non-wetting of slag, ② high thermal conductivity, ③ low thermal expansion. In addition, graphite and refractory materials do not melt together, and graphite has high refractoriness. It is precisely because of this characteristic that magnesia carbon bricks are selected for slag lines with harsh operating environments. For low carbon magnesia carbon bricks (mass fraction of carbon ≤8%) or ultra-low carbon magnesia carbon bricks (mass fraction of carbon ≤3%), it is difficult to form a continuous network structure due to the low carbon content, so the design of the organizational structure of low carbon magnesia carbon bricks is relatively complicated. On the contrary, the organizational structure design of high carbon magnesia carbon bricks (mass fraction of carbon>10%) is relatively simple.
Due to the fact that magnesia carbon bricks are susceptible to moisture and the influence of formula selection, the performance of magnesia carbon bricks will be affected to a certain extent. When magnesia carbon bricks are damp, the structure becomes loose, and water escapes at high temperature to produce multiple empty channels, which will have a negative impact on the thermal stability and corrosion resistance of magnesia carbon bricks, and the ability to cope with molten steel will be greatly weakened. MgO-C is very sensitive to thermomechanical abrasion because the thermal expansion coefficient of MgO has a high reversibility. The binder of magnesia carbon bricks is also an important factor affecting the quality of magnesia carbon bricks. Too much or too little binder content will affect the performance of magnesia carbon bricks. If the binder content is too little, the magnesia carbon brick powder is not tightly bound and is easily washed and peeled off; if the binder content is too much, the thermal shock stability and refractoriness of magnesia carbon bricks will deteriorate, and too many harmful elements will be added to the molten steel.
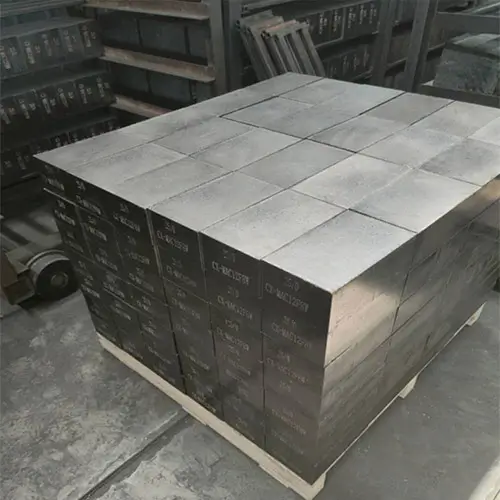
When the ladle receives the molten steel from the converter, a large amount of slag will be produced at the same time. The low-melting-point 2CaO·SiO2 in the slag dissolves into the MgO grain boundary and reacts chemically with the trace impurity elements in the MgO layer, which plays a major role in the dissolution of magnesia refractory materials. From the perspective of converter slag, research on improving the performance of magnesia-carbon bricks mainly focuses on magnesia sand, antioxidants and microstructure.
In addition, the addition of antioxidants to magnesia carbon bricks also affects their quality. In order to improve the oxidation resistance of magnesia carbon bricks, a small amount of additives are often added. Common additives include Si, Al, Mg, Al-S, Al-Mg, Al-Mg-Ca, Si-Mg-Ca, SiC, B4C, BN and Al-B-C and Al-SiC-C series additives. The role of additives mainly has two aspects: on the one hand, from a thermodynamic point of view, at the working temperature, additives or additives react with carbon to generate other substances. Their affinity with oxygen is greater than that of carbon with oxygen, and they are oxidized before carbon, thereby protecting carbon. On the other hand, from a kinetic point of view, the compounds generated by the reaction of additives with O2, CO or carbon change the microstructure of carbon composite refractory materials, such as increasing density, blocking pores, and hindering the diffusion of oxygen and reaction products [28]. At present, Al powder is mainly used in magnesia carbon bricks to prevent the oxidation of carbon. Although Al has a strong ability to resist oxidation, at high temperatures, Al reacts with C and N2 to form Al carbon and nitrogen compounds. Among them, Al carbide is prone to hydration in the process from high temperature to low temperature, resulting in the formation of voids inside the magnesia carbon brick, which causes the structure to become loose and cracks to form.
3.Masonry method
Magnesium carbon bricks in ladle slag line generally adopt two methods: dry laying (directly stacking bricks without fireclay bonding) and wet laying (using fireclay combined with refractory bricks). The advantage of dry laying is that it minimizes the impact of fireclay. Under high temperature conditions, due to the different materials of magnesium carbon bricks and fireclay, the thermal expansion rates are different due to the influence of temperature, which easily leads to gaps on the contact surface. The disadvantage of this method is that the magnesium carbon bricks cannot guarantee 100% close contact. At the same time, when the magnesium carbon bricks expand due to heat, there is no room for buffering between bricks, resulting in bricks being squeezed and broken; or due to the expansion of magnesium carbon bricks, the whole ring of slag line is lifted as a whole, and the huge extrusion force causes the ladle edge plate to deform, and the refractory material loses protection and is washed and peeled off, posing a greater threat to the quality of the slag line.
The wet masonry method is similar to the masonry method in construction, but the requirements are more stringent. The advantage of this method is that it can well avoid the gaps that may occur in dry masonry. At the same time, the strength of fire mud is weak at high temperatures. When the magnesia carbon bricks expand due to heat, they can flow to adapt to the changes in the gaps between bricks, dispersing the squeezing force between bricks, thereby avoiding the generation of gaps. The disadvantage of this method is that the use of fire mud makes the structure of the slag line unstable and increases the difficulty of masonry. If the fire mud is uneven, gaps will still occur between bricks.
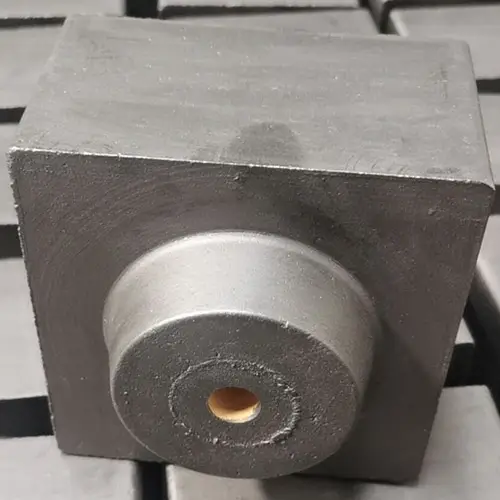