The tundish is a container for holding molten steel after the steelmaking ladle equipment and for diverting the molten steel for continuous casting. The tundish is the last container in the continuous casting system that contacts the refractory material before the molten steel is formed. It is an important part of the continuous casting process and has a great impact on the quality of steel. With the advancement of smelting technology and the emergence of ladle secondary refining technology, the tundish has many important functions, such as providing a stable static pressure of the molten steel, maintaining the stability of the molten steel flow rate and flow strands to reduce turbulence, removing non-metallic inclusions in the molten steel, purifying the molten steel, and keeping the molten steel temperature basically unchanged. It has become a molten steel refining container before the molten steel is formed. With the increase of the functions of the tundish, the variety of refractory materials used in the tundish has increased, and the quality requirements for refractory materials have become higher and higher. In order to meet the use requirements of the tundish, China has developed many high-quality refractory products in recent years.
1.Development history of refractory materials for tundish lining
The traditional lining of the tundish is mainly composed of permanent lining and working lining, and its refractory materials are light bricks, heavy bricks, insulation boards, coatings and dry materials. Traditional permanent linings are all built with refractory bricks. Due to the many brick joints and poor integrity, it is easy to cause puncture accidents. In recent years, with the successful application of integral casting technology on ladles, the permanent lining of the tundish also uses castables or ramming materials of amorphous refractory materials. The development of the working lining of the continuous casting tundish in my country is roughly as follows.
1.1 Silicon insulation board period
From the introduction of continuous casting technology in the 1980s to 1995, the tundish working lining mainly used siliceous insulation boards, whose main raw materials were quartz sand, a portion of paper scraps, powdered thermoplastic phenolic resin and methenamine, vacuum filtration molding, and use after drying. The average service life is about 6 hours, and the maximum is no more than about 10 hours. Siliceous insulation boards have a short service life, poor corrosion resistance, and pollution to molten steel. Since 1995, they have been gradually replaced by magnesium or magnesium-calcium coatings.
1.2 Magnesium or magnesium-calcium coating period
Before 2000, the working lining of the continuous casting tundish in my country generally used magnesium or magnesium-calcium coatings, which were applied on the surface of the permanent lining of the tundish, with a thickness of generally 35-40 mm. This type of alkaline coating is usually prepared by sintering or fused magnesia sand or magnesium-calcium sand. However, since magnesium-calcium sand is easily hydrated, raw dolomite can be used to introduce CaO or anti-hydration magnesium-calcium sand and magnesium sand can be mixed in a certain proportion. The critical particle size of the coating is 3-5 mm, of which 60%-65% are larger than 0.088 mm, and 35%-40% are smaller than 0.088 mm. Organic fiber accounts for 0.5%-2.5% (short fibers processed from natural plants are better). As the amount of fiber added increases, the volume density decreases, and it is generally better to control it at 1.9-2.3 g/cm3. The main additives are plasticizers, such as soft clay, bentonite, silica powder, slaked lime, etc., which also play a sintering role. The higher the CaO content of the tundish lining, the better the effect of purifying molten steel. However, it is difficult to prepare coatings with high CaO content. Generally, the CaO content of coatings is between 10% and 50%.
Forsterite is used to replace magnesia to produce tundish coating. Forsterite has low thermal conductivity, high refractoriness, no hydration, good chemical stability, and good resistance to metal melt penetration. Moreover, it is rich in resources and widely distributed, which can be said to be both energy-saving and environmentally friendly, and can reduce costs. The formula of forsterite tundish coating produced by Xinjiang Bayi Steel Plant is: forsterite 40% (2.5-0.5 mm), medium-grade sintered magnesia 48% (0.5-0.088 mm), lightly burned magnesium oxide powder 5% (<0.088 mm), plus magnesium sulfate heptahydrate 2.5%, paper fiber 2%, borax and explosion-proof fiber 0.1% each. It can be adjusted appropriately according to different seasons. The amount of water added is about 25%, and it is applied manually with good adhesion. The service life is equivalent to that of magnesium coating, which can reach 10-14h. Its thermal insulation performance is better than that of magnesium coating. When turning the bag after use, it is easy to separate from the permanent lining.
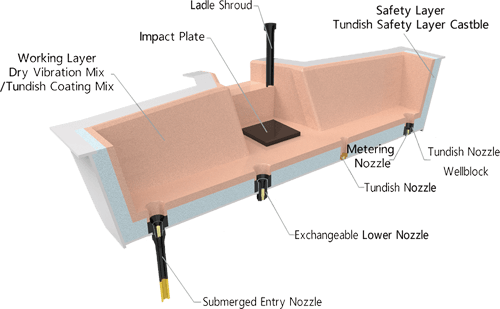
1.3 Wet alkaline spray coating
Wet alkaline spray coating is generally sprayed with a spiral pump, and the mud is sprayed onto the permanent lining. The spray coating is composed of sintered magnesia or magnesia-calcium sand, a binder, a plasticizer and organic fiber. It is required that the CaO/SiO2 of magnesia can be controlled above 2, and a small amount of raw dolomite or limestone fine powder can also be added to increase the CaO content. It is not only beneficial to the purification of molten steel, but also beneficial to the disintegration and shedding of the coating. The binder can be instant polyphosphate, instant water glass or composite polyphosphate. Plasticizers include soft clay, carboxymethyl cellulose, calcium lignin sulfonate, etc. Add organic fiber, generally natural plant fiber is preferred, requiring a diameter of 10 to 40 μm, a length of 1 to 5 mm, and an amount of addition within 0.5% to 3%. The thickness of the spray coating is determined according to the use requirements, requiring 45 to 60 mm for 20 to 30 heats, and 60 to 80 mm for 30 to 40 heats.
With the advancement of iron and steel metallurgical technology, not only the service life of the tundish is required to be long, but also the cleanliness and thermal insulation effect of the steel are required to be high. Therefore, ultra-light (volume density 1.4g/cm3) magnesium spray coating is available. At present, the manufacturing method of ultra-light spray coating mainly adopts lightweight aggregate, adds fiber and adjusts the particle size, and adds foaming agent. For example, the proportion of ultra-light tundish spray coating used by Baosteel Electric Furnace Plant is: w (aggregate + paper fiber + glass fiber): w (silicon powder): w (foaming agent alkyl sulfonate FL): w (foam stabilizer amine organic matter M): w (sodium tripolyphosphate): w (other additives) = 100: 3: 0.05: 0.02: 0.25: 0.05. The physical and chemical indicators of the spray coating are: w(MgO)=83.36%, w(CaO)=1.56%, w(SiO2)=5.66%, the volume density after drying at 110℃ for 24h is 1.45g/cm3, the compressive strength is 2.12 MPa, the volume density after burning at 1500℃ for 3h is 1.40 g/cm3, and the compressive strength is 6.1MPa. Production and use show that: the wall and bottom of the tundish are wet-sprayed with a spiral mixer, and there are no cracks. There are only a few small cracks at the angle of the wall, which is within the allowable range. Wet spraying is usually used for new lining spraying and areas where the lining is not damaged, to prevent local damage.
Although the service life of the tundish coating and spray coating is longer than that of the silicon insulation board, the average service life is about 10h, up to 24h, and it has a purifying effect on molten steel. However, there are disadvantages such as high labor intensity, long maintenance time, and complex baking process during spraying.
1.4 Alkaline dry material
Since 2000, with the promotion of the technology of fast nozzle replacement in the tundish, higher requirements have been put forward for the tundish working lining, and new alkaline dry materials have been applied and promoted. Dry materials are easy to construct and bake, and the labor intensity is greatly reduced. Moreover, they can be constructed under any climatic conditions and have a long service life of more than 40 hours.
The alkaline dry material of the tundish is composed of sintered magnesia sand, magnesia calcium sand or fused magnesia sand, magnesia calcium sand, medium and high temperature sintering agent and a small amount of low temperature binder. The sintering agent includes magnesia calcium iron sand, soft clay, borate, iron scale, etc. The purpose of adding a small amount of low temperature binder is to produce strength after baking with a mold at 200-300°C, so that the lining has shape retention. The binder is generally a powdered phenolic resin. A steel company in Shanxi Province conducted a study on the dry material of the tundish and found that: fused magnesia sand is used as the main raw material, the ratio of aggregate to matrix material is 65:35, among which the aggregate adopts three-level particle grading of 5-3mm, 3-1mm and <1mm; the matrix material includes two kinds of fine powders <0.044mm and <0.088mm; the binder adopts powdered phenolic resin containing a hardening accelerator, and the addition amount is preferably 6%; the sintering agent is metaphosphate, and the addition amount is preferably 2%; the modifier is a synthetic material containing Al2O3, and the addition amount is preferably 3%. The average service life of fused magnesia dry material is more than 40 hours, while the service life of sintered magnesia dry material can reach 24 hours.
Since no water is needed for reconciliation, sintered magnesium calcium sand can be used to prepare dry materials with different CaO contents, which is beneficial to purifying molten steel, improving the service life of the working lining, and can be continuously cast in multiple furnaces. The remaining lining is easy to remove (fall off) after use. However, during the firing process, phenolic resin decomposes some cresol, formaldehyde, xylenol and other components, which cause great pollution to the environment. In addition, the residual carbon after solidification pollutes the molten steel and is not suitable for low-carbon steel. A refractory enterprise in Inner Mongolia explored the binder of magnesium dry materials and found that the composite addition of metasilicate, phosphate and borate with an addition amount of about 6% has a good effect. In addition, α-Al2O3 and CaCO3 mixed micropowders are added to generate spinel at high temperature, accompanied by volume expansion, supplementing volume shrinkage, and stabilizing the overall volume. The decomposition of Ca CO3 produces some micropores to increase thermal insulation performance.
The study on the collapse and local peeling of dry materials in the tundish found that the introduction of glass fiber and explosion-proof fiber in the dry materials can effectively improve the collapse and peeling of dry materials. The addition of composite antioxidants Al powder and Si powder and boric acid to promote sintering of magnesia sand also have certain effects.
The nano-porous insulation board (5 mm thick) + floating bead bricks (30 mm thick) + permanent lining castable (185 mm thick) + working lining coating (40 mm) are built in the steel shell of the tundish. Not only does the shell cool down significantly, but it also reduces the temperature drop and temperature fluctuation of molten steel during the casting process of the tundish, and improves the quality of the ingot.
2.Slag retaining weir (wall)
The slag weir (wall) is set in the continuous casting tundish to change the flow state of molten steel in the tundish, increase the residence time of molten steel, promote the floating of inclusions in molten steel, and play a role in purifying molten steel. There are two types of slag weirs (walls): high-aluminum and magnesium. High-aluminum slag weirs have good resistance to thermal vibration, slag erosion and molten steel scouring. Magnesium slag weirs can absorb Al2O3 and SiO2 inclusions in molten steel, improve the cleanliness of molten steel, and will not cause secondary oxidation of molten steel. my country’s magnesium slag weir uses magnesium castables made of electro-melted or sintered magnesia sand and silicon micropowder to form a MgO-Si O2-H2O system cohesion and bonding, and adds explosion-proof agents, dispersants or 2% steel fibers.
The magnesium slag weir has a long service life and is easy to be penetrated; the aluminum-magnesium slag weir has good corrosion resistance, but it is not as good as the magnesium slag weir for the purity of molten steel. It is very important to use a composite slag weir, that is, the slag line uses aluminum-magnesium castables, and the molten steel area uses magnesium castables. After vibration molding, the two materials are combined into one to form a composite slag weir, so that the two castables are well combined and have good construction performance. Therefore, it is necessary to select a retarder for magnesium material, add 0.15% sodium polyhydroxy acid by mass, select SiO2 micropowder with a pH value close to 7 or slightly greater than 7, and the water reducer is a composite of tripolyphosphate and organic water reducer, so that the magnesium castable and aluminum-magnesium castable have the same construction effect. The use temperature, slag amount, and slag liquid level fluctuation amplitude of the tundish of each steel plant are different. The production ratio of the two materials should be determined according to the actual situation. Generally, the upper one-third is aluminum-magnesium and the remaining two-thirds are magnesium castables.
3.Filters
In order to better purify molten steel, installing a ceramic filter that can remove non-metallic inclusions on the wall next to the tundish is one of the effective measures. The filters are divided into foam filters, mesh filters and annular filters, each with its own advantages. The structural forms include slit type, straight-through hole type and dispersion type. The materials currently used are mainly CaO, ZrO2, Al2O3, SiC and cordierite. In 1988, Wuhan Iron and Steel developed a lime filter with a non-metallic inclusion removal rate of more than 10% to 30%. During the “Ninth Five-Year Plan” research and development period, a high-purity straight-through hole ceramic filter with a CaO content of more than 98% was developed. It was tested on the 10t tundish of the Liuzhou Steel slab continuous casting machine. The service life is synchronized with the lining refractory material (continuous casting 7 to 8 furnaces), and the filtration efficiency is 22.7% to 40.0%. It is also very effective in reducing non-metallic inclusions in molten steel when used in Baosteel. Anshan Iron and Steel Co., Ltd. installed a filter with w(CaO)>97% on the high-aluminum slag weir, which reduced the non-metallic inclusions in the steel by 13.1%. When the flow rate of molten steel is large, a straight-through filter is used; when the flow rate is small, a foam filter is selected. CaO filters can absorb molten steel inclusions, but they are difficult to manufacture.
4.Bottom blowing air brick
By installing air-permeable bricks near the tundish slag weir and blowing argon, the inclusion content is reduced by more than 20% compared to the case without argon blowing. Compared with other methods that can only remove larger inclusions, the tundish argon blowing technology plays a particularly important role in removing tiny inclusions of about 50μm to ensure the quality of special thin steel sheets (such as automobile steel sheets). The airway structure and operation method of this air-permeable brick are different from other air-permeable bricks. There are also various blowing methods to make the gas carry the inclusions to float up without blowing away the protective slag, such as burying air-permeable pipes, installing air-permeable beams, and burying air-permeable elements in the slag weir or at the bottom of the ladle.
5.Flow stabilizer
The flow stabilizer is a functional refractory material that stabilizes the flow state of molten steel injected into the impact zone of the tundish, improves the flow field of molten steel in the tundish, promotes the floating of inclusions, and prevents slag from being drawn into the molten steel, causing internal quality defects of the continuous casting billet. A steel plant in Shandong uses large-grained fused magnesia as the main raw material, silicon powder as a binder, and steel fiber to manufacture the flow stabilizer, which has a good effect and a maximum service life of 100 hours.
6.Air curtain retaining wall
The air curtain retaining wall is located at the bottom of the tundish. The air curtain is used to blow argon into the molten steel in the tundish to produce floating bubbles, which cause inclusions to float to the surface slag layer. The upper dense layer of the air curtain retaining wall should have sufficient strength and will not crack under the static pressure of the molten steel. The working pressure of the air curtain retaining wall is 0.2MPa, and the air permeability is 5-10 L/min. The material used must be resistant to erosion by molten steel and slag. Some also set steel flow buffers and air permeable beams in the tundish.
7.Covering agent
The heat dissipation of the steel liquid surface in the tundish is very large, accounting for more than 90% of the heat loss of the tundish. The tundish steel covering agent plays an important role in heat preservation of molten steel, reducing heat loss and temperature drop during steel pouring, absorbing floating inclusions in the molten steel, improving the quality of molten steel and preventing secondary oxidation of molten steel in the tundish, giving full play to the metallurgical function of the tundish. Therefore, the covering agent is required to have less erosion on the lining of the tundish and the ladle casing, and have good operability. That is, it should be well spread and covered on the surface of the molten steel, without crusting during the steel pouring process, and easy to clean after the steel pouring is completed and does not affect the unpacking operation.
The covering agents used are mainly single-layer covering agents (such as carbonized rice husks, composite slag) and double-layer covering agents (carbonized rice husks + composite slag). Carbonized rice husks have good heat preservation, but cannot purify molten steel, and may have a carbon-enhancing effect on some low-carbon steels. When using composite slag, a liquid slag layer is formed on the surface of the molten steel, which is conducive to absorbing and assimilating the floating inclusions in the molten steel. Adding carbonized rice husks or other insulation materials to the surface of the composite slag can achieve the functions of insulation and purification at the same time.
The traditional tundish covering agent has achieved good results when using silicon insulation board as the working lining, but it is not suitable for magnesium tundish lining. This covering agent is based on the CaO-Al2O3-SiO2 ternary phase diagram. In order to adapt to the magnesium coating lining of the tundish, the MgO-Al2O3-SiO2 covering agent is used instead. The base material falls in the ternary system, and its melting point is controlled at 1200-1450℃, without adding flux such as CaF2. According to the influence of drainage sand on the covering agent, the more suitable melting point is between 1350 and 1450℃. The melting rate is more suitable when it is 20-30℃/s; the viscosity is more suitable when it is 1.0-1.2Pa·s at 1450℃. Too much viscosity will cause crusting. With appropriate viscosity, it can insulate and prevent secondary oxidation of molten steel.
Disadvantages of magnesium covering agent: large-area sintering is prone to occur during use, especially in the tundish where the flow rate is controlled by a stopper rod. Large-area sintering will stick to the stopper rod. Some people have studied the effects of graphite and magnesia powder amount, as well as the type and amount of ladle slag added on the sinterability of granular magnesium covering agent in the tundish. The results show that adding a certain amount of graphite (≤15%) to the covering agent particles can promote sintering between covering agent particles. In the finished product of granular magnesium covering agent, 2-3mm and 1-2mm particles have basically no bonding phenomenon (the particles are made by adding fine powder to 3% starch, adding 16% to 24% water, and mixing evenly with a swing granulator), 0.6-1.0mm particles have slight bonding, and <0.6mm particles are sintered together. Therefore, the more fine powder, the easier it is to sinter. The greater the amount of ladle slag added, the easier it is to sinter between covering agent particles.
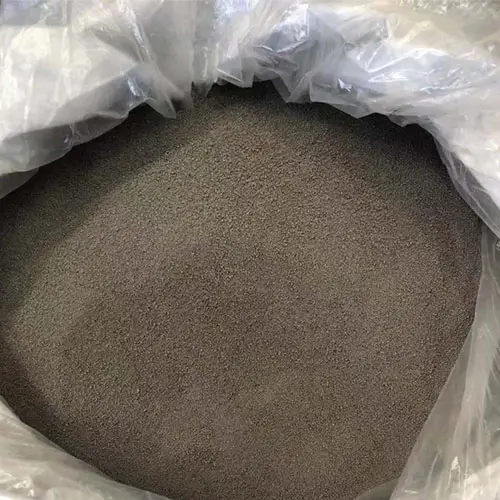
In order to improve the adsorption of inclusions in molten steel by the covering agent, a calcium covering agent was developed. At the same time, lightweight thermal insulation materials (perlite and rice husk 20%) and gas retaining agents were introduced into the covering agent, so that a reasonable amount of gas exists in the upper powder layer to increase the thermal insulation effect. At the same time, composite carbon source was introduced. The higher the carbon content, the smaller the particle size, and the stronger the melting rate was reduced. The appropriate melting rate enables the covering agent to maintain a reasonable three-layer structure during the working process, namely the molten layer, the semi-molten layer, and the powdery layer. It is more appropriate to control w(Ca O)=30%~45%, w(Al2O3)<10%, and w(Si O2)=5%~15% for this covering agent, and the actual use effect is good.
By adding appropriate diluents, air entraining agents and air retaining agents, the composition, melting temperature, melting rate and viscosity of the covering agent are optimized. The physical and chemical performance indicators of the developed high calcium alkaline covering agent are: w (Ca O)> 50%, w (Si O2) < 10%, w (C) < 12%, volume density 0.8 ~ 1.2 g / cm3, melting temperature 1300 ~ 1400 ℃, viscosity (1450 ℃) 0.8 ~ 1.2Pa s. Due to the high content of free CaO, the ability to adsorb inclusions in the molten steel is strong, and the low content of SiO2 reduces the viscosity of the slag, making it easier to adsorb inclusions.
8.Cover
Clay or high-alumina prefabricated parts are commonly used.
9.Tundish Refractory Products
The tundish is an important equipment in the continuous casting process. The refractory lining used mainly includes the insulation layer, permanent layer and working layer.
(1) The insulation layer (i.e., the insulation layer, 10-30 mm) is close to the steel shell. Its main function is to keep warm. It usually uses asbestos insulation bricks or lightweight castables, aluminum silicate fiber felt, and nano-microporous insulation board plus lightweight insulation bricks.
(2) The permanent layer (100-200 mm) is in contact with the insulation layer and mainly plays a safety protection role. In the 1970s, clay bricks were mainly used for masonry, and later high-aluminum bricks were used. In the late 1980s, castables were used for integral casting, generally high-aluminum or semi-lightweight mullite castables.
(3) The working layer (20-50 mm) is in contact with the molten steel. In the early days, high-aluminum bricks were used, and later insulation boards were used. Later, refractory coatings and refractory spray coatings were used. With the development of multi-furnace continuous casting technology and rapid nozzle replacement technology, dry vibrating materials have begun to be used. The insulation board is generally made of silica, magnesia and forsterite, and the coating and dry materials are mostly made of magnesia, magnesia-calcium and magnesia-chromium.
(4) The impact zone of the bottom of the ladle is mostly reinforced with prefabricated blocks, generally made of corundum, magnesia and castables, and some use zircon bricks or castables.
(5) The slag weir is generally made of high-aluminum, aluminum-magnesium and magnesium prefabricated parts.
(6) The stopper rod is made of aluminum-carbon or magnesium-carbon materials.
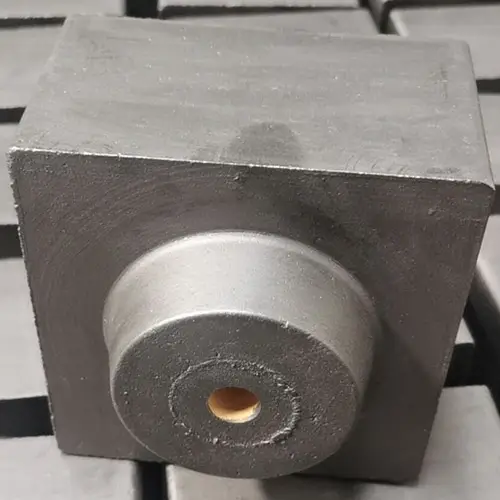