Production process of refractory bricks
The production of refractory bricks goes through multiple production processes and procedures. Each Zhengyuan refractory brick undergoes strict quality control. Today, the editor will introduce to you how refractory bricks are made. Refractory brick production process introduction: raw material selection, high temperature calcination, sorting and grading, crushing and grinding, scientific batching, mixing, trapped materials, strong restriction molding, static drying, high temperature firing, kiln inspection and packaging, loading and delivery. The production and process of high-alumina refractory bricks mainly depends on the nature of the raw materials or the quality requirements of the finished product.
(1) Material preparation
It mainly involves the preparation of high-aluminum clinker and the preparation of combined high-aluminum. The preparation of clinker is to calcine the refractory high-aluminum raw materials at high temperature into various levels of granular materials and fine powders, and the preparation of combined high-aluminum is to crush the high-aluminum coarsely, dry, grind it into powder and mix it into slurry.
(2) Batching, mixing and molding
The calcined refractory high-alumina clinker is used as the lean material, and a certain proportion of combined high-alumina is added to make a mixture. The clinker accounts for a large proportion in the mixture, which is called a multi-clinker product. This type of crystal has high volume stability and other properties are also good, but it requires strong molding.
(3) Heating and drying
The moisture content of high alumina brick blanks varies according to the molding method. Semi-dry pressed blanks have low moisture content and almost no shrinkage when the water evaporates. They can be dried quickly or directly loaded into the kiln. Brick blanks with high moisture content can be dried by natural air drying or hot air heating in advance, and then sent to the tunnel kiln. The key factor in controlling the drying process is the drying speed, which should be based on the principle of ensuring that the brick blanks do not deform, crack and have a certain strength. The moisture content of the brick blanks that finally enter the firing kiln is controlled to be below 2%.
(4) Firing
The purpose of firing is to sinter the bricks so that they have a certain strength of appearance, density and porosity, high mechanical strength, good volume stability and good fire resistance.
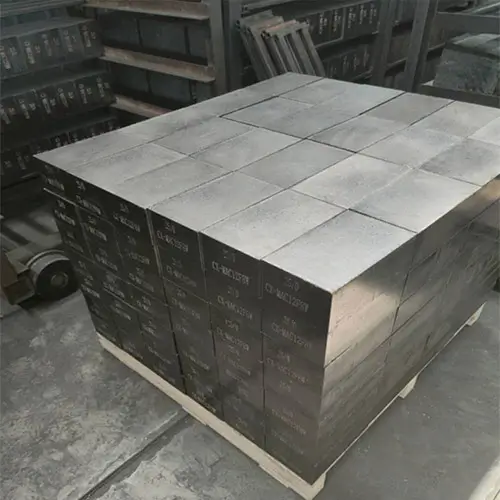
Special shaped refractory bricks
1.Special-shaped refractory bricks are irregular in shape
Because special-shaped refractory bricks are refractory bricks with irregular shapes, although they can be made into refractory bricks of different materials. However, due to their weight or shape, they are difficult to shape or burn, so they are difficult to make. Generally, special-shaped refractory bricks are used in nozzles, furnace doors, pipes or some irregular parts with steel parts, but the number of special-shaped refractory bricks is small, and it is difficult to shape them. Because of their small number, many manufacturers use manual or hydraulic methods to make them.
2.Special-shaped refractory bricks are made in different ways
If the refractory bricks made of clay and high-alumina bricks weigh more than 100kg, the ratio of prefabrication is relatively high, because the casting molding process is simple. For clay bricks and high-alumina special-shaped refractory bricks with small weight, the water discharge must be controlled, and the firing process can be fired together with standard bricks. If the free water and crystal water are not discharged completely, it is easy to burst during firing.
If the unit weight of the special-shaped refractory brick is small, it is made with wooden molds, and it is also extruded with steel molds. The cost of using steel molds is high, and it is not easy to shape. After drying, it must be sintered at high temperature. The process in the production process will be more labor-intensive and time-consuming than the commonly used standard bricks, because the drying process in the middle is long. If the bricks are too heavy, the finished product rate will be lower after firing.
If the pouring method is used, there will be no situation where it is difficult to shape or the finished product rate is low, but the drainage process of prefabricated bricks is long, and the production time needs to be controlled. In general, the use time should be communicated with the user manufacturer, and it cannot be delayed.
If the special-shaped refractory bricks are made into magnesia refractory bricks, it is necessary to consider the control of the drainage process, because magnesia refractory bricks are afraid of water. If the drainage process is not scientific, the fired finished product is easy to crack or explode. If it must be made into magnesia refractory bricks, try to use the method of mechanical forming. If it is formed by hand, the yield rate of magnesia special-shaped refractory bricks.
If it is to be made into silicon special-shaped refractory bricks, the mold size needs to be well-made before the mold can be made, otherwise the finished product will be too large to be used.
The reason why special-shaped refractory bricks are difficult to make is that the conditions are different and the quantity is small. It depends on different conditions. If the weight is small, it can be directly pressed by machine. If the weight is too large, prefabricated refractory bricks can be selected. If you must use machine pressing and friction molding, you must make sure to make the mold size in advance.
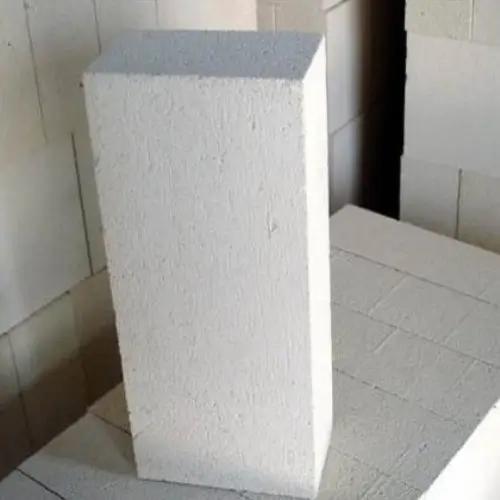