1.Furnace bottom
There are three structural forms: full ceramic, full carbon brick and integrated furnace bottom.
In the past, when designing the furnace bottom, heat dissipation and cooling conditions were not taken seriously, which was a typical corrosion-inhibiting full ceramic design. At present, this form is only suitable for the furnace bottom structure of small blast furnaces.
The design of the furnace bottom of modern blast furnaces mainly focuses on heat transfer. Carbon bricks are used, combined with cooling, and permanent furnace bottoms, namely full carbon brick furnace bottoms and integrated furnace bottoms, have appeared. By heat dissipation, a sintering layer is formed at the furnace bottom as early as possible to limit the erosion to this range. In essence, an iron retaining wall is built with the isotherm (or surface) of the solidification temperature of molten iron (generally 1150℃). Obviously, as the heat dissipation capacity of the furnace lining increases, this isotherm is compressed away from the furnace shell and furnace base, that is, the molten iron is surrounded in a smaller range. After the blast furnace is opened, as the molten iron erosion line moves downward, the 1150℃ isotherm also moves downward, but the former moves faster, and finally the two overlap, and a stable “iron shell” protective layer is formed at the furnace bottom. As long as the thermal balance is not destroyed, the protective layer will remain “permanently”.
A more reasonable one is the integrated furnace bottom with furnace bottom cooling. On the base is the air-cooled carbon ramming layer, on which 2 to 3 layers of carbon bricks are laid flat or vertically, and on top of that, there are ring-laid carbon bricks all around until below the slag mouth, and in the center are vertically laid high-alumina bricks or clay bricks. Carbon bricks with different properties should be used according to different parts. Microporous carbon bricks with good permeability resistance are used for the parts below the iron mouth that are prone to severe erosion; high thermal conductivity C-SiC bricks are used for the lowest layer of the furnace bottom; ordinary carbon bricks or microporous carbon bricks are used for the rest of the parts. At the same time, the length of the ring-laid carbon bricks below the slag mouth should be increased to resist the strong penetration and erosion of molten iron and alkali metals; the brick joints should also be changed from wide joints to narrow joints (less than 0.5mm).
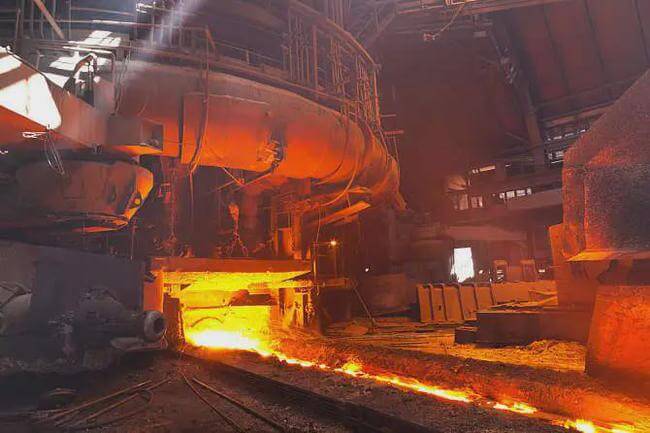
2.Furnace cylinder
The furnace lining is thinner than the furnace bottom to enhance cooling to protect the slag skin and the not very thick graphite layer precipitated from the molten iron. Modern blast furnace furnaces are mostly built with carbon bricks. In China, they are built to the center line of the slag mouth or between the tuyere and the slag mouth. The junction between carbon bricks and high-alumina bricks should avoid the slag liquid surface. There are also full carbon brick furnaces abroad. The thickness of the furnace side wall is 685~1350mm, which is generally thinned to 570mm at the tuyere. Small and medium-sized blast furnaces are mostly built with all high-alumina bricks or clay bricks.
3.Furnace belly, furnace waist and furnace body
Since the furnace belly mainly relies on slag skin, the commonly used structure is a ring of high-alumina bricks (or clay bricks) with a thickness of 345mm or 230mm, so as to protect the surface of the brick-lined cooling wall from being burned when the furnace is opened. When laying, it is necessary to lay close to the cooling wall or the furnace shell, and ensure that the vertical joints are staggered, the same as the brick rings laid flat on the furnace cylinder, and the brick joints are less than 1mm.
The furnace waist structure has thick walls, thin walls and transitional forms. The brick lining of the furnace waist should be considered in combination with the expected operating furnace type and the cooler used. Since the coal gas rises along the inclination direction of the furnace belly and turns at the junction of the furnace belly and the furnace waist, it is inevitable to scour the furnace waist. The thick-walled furnace waist lining is easily scoured and eroded by the coal gas flow, which makes the furnace belly height expand upward and the radial section increase. Moreover, the greater the furnace waist height, the thicker the furnace lining, the higher the furnace belly extends upward, and the greater the radial expansion, which makes the design furnace type and the operating furnace type differ greatly. If a thin-wall furnace waist is used, the above disadvantages can be avoided and the furnace shape can be fixed. However, when the original design furnace shape is too different from the reasonable operation furnace shape, an unreasonable fixed furnace shape will be obtained. The transition form is to use brick cooling walls at the furnace waist and the lower part of the furnace body. The brick lining of the furnace waist is gradually thickened, which can be gradually increased from 345mm to 575mm (or 690mm) at the lower part of the furnace body. The furnace waist also adopts the circular bricklaying method, and the brick joint is less than 1mm.
With the emergence of new refractory materials, the refractory materials at the bottom of the furnace body are constantly improving. From high-alumina bricks, sillimanite bricks, synthetic mullite bricks, fired corundum bricks to silicon carbide bricks, silicon carbide bricks combined with silicon nitride are all used. From single high-alumina bricks and high-density clay bricks to various combined furnace linings. For example, the inner and outer layers of the furnace lining are made of different materials. Silicon carbide bricks are laid in the outer masonry near the brick-lined cooling wall, and clay bricks or high-alumina bricks are laid in the inner layer.
The thickness of the furnace body brick lining has tended to be thinner, usually 690~805mm, the lower section of the brick joint is not more than 1.5mm, and the upper section is not more than 2mm. The circular bricklaying method is adopted. Because the furnace body is relatively high, a stagger is made every 5 layers to reduce the inner diameter, and it is controlled by an active radius gauge. In order to prevent the water slag filler in the gap with the furnace shell from loosening downward, a circle of bricks can be pushed to the furnace shell every 10~15 layers.
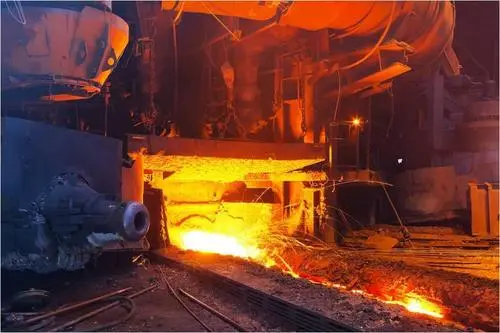
4.Furnace throat and furnace head
The throat protection plate (or throat steel brick) is filled with refractory materials behind it to serve as the throat lining to resist the impact of the charge and high temperature expansion. Steel bricks are hollow boxes made of cast steel with a wall thickness of 60 to 150 mm. There are mainly block-shaped, strip-shaped and variable-diameter throat protection plates.
Block-shaped hanging throat protection plates are composed of several rings of small steel bricks of different shapes. Each ring has more than a dozen steel bricks, and the adjacent steel brick side walls are connected with screws. Then the upper and lower rings are connected together with screws and hung on the furnace shell with eight hanging plates. In this structure, the entire ring is almost rigidly connected. Under the action of long-term high temperature, the horizontal linear expansion is greater than the longitudinal direction. The steel bricks squeeze each other and protrude into the furnace, and even the entire throat becomes funnel-shaped and accelerates damage. In view of the above shortcomings, the strip-shaped throat protection plate is changed to a long strip along the height of the throat. The entire throat structure is composed of dozens of strip-shaped protection plates. Each steel brick has two upper and lower hanging devices. A 20mm gap is left between two adjacent steel bricks to prevent mutual influence of thermal expansion. It has good adaptability to uneven temperature and small thermal stress, so it has been widely used.
The movable throat protection plate is used on large blast furnaces. It not only solves the strength problem of the throat structure, but also mainly regulates the distribution of furnace charge and airflow, as a supplementary means of charging and distributing.
The furnace head is often lined with a cast steel lining plate inlaid with refractory bricks. It is connected to the furnace shell with screws, and clay-cement slurry is poured into its gap. Some small and medium-sized blast furnaces are also lined with bricks. A brick ring is laid flat on a circular support beam made of steel. The first ring is close to the furnace shell, and the layers above are laid flat inwards.