Quartz sand is an acidic furnace lining material, due to the low price and wide range of sources. Once the silica sand after the first furnace high-temperature sintering to complete its phase change, volume expansion changes, the late melting of the furnace lining volume change is very small, thermal stability and anti-ferrous liquid leakage performance is good, but also to adapt to intermittent operation of the melting conditions. In addition, the load softening temperature and refractoriness of quartz sand is close to the high-temperature thermal shock strength, so the melting of cast iron furnace manufacturers commonly used quartz sand acid knotting furnace lining materials.
Medium-frequency induction furnace furnace lining materials and iron contact with the hot surface of the internal sintering layer, by the back of the induction coil by the internal cooling water cooling, the temperature of the furnace lining material will be in the direction of the vertical section of the temperature gradient exists; at the same time by the electromagnetic stirring of iron and iron furnace cyclical melting, out of the iron backing up the operation of the impact, so that the furnace in the furnace, on the furnace lining material does not have a strong mechanical contraction and the repetition of the rapid hot and cold! In order to ensure the normal service life of the furnace lining, the furnace lining material is required to have good characteristics to meet the needs of special working conditions.
A quality quartz sand-based furnace lining material must have the following characteristics:
Sufficiently high refractoriness and load softening point:
Medium-frequency induction furnace for cast iron smelting furnace temperature is generally in 1500-1650 ℃, so the requirements of the refractoriness of the furnace lining materials and load softening temperature is not lower than the highest above temperature, and even greatly exceed this temperature, which is to ensure that the lining of the furnace in the closure of the furnace, the shed material, excessive heating can still be safe to use the basic premise of the case, so as to ensure that unnecessary safety accidents occur.
Good chemical stability:
It is required that no decomposition and reduction reactions occur under high or low temperature conditions, and it is not easy to produce reactants with metal alloys, metal slag, etc. during the melting process, that is, the chemical properties must be stable.
Good thermal stability and small thermal expansion coefficient:
The temperature of the molten iron in the furnace lining is constantly changing, and the refractory material does not crack due to uneven heating; after the sintering phase change volume expansion is completed, the volume expansion must be stable during the repeated temperature changes during the melting process, and there must not be drastic expansion and contraction that causes the furnace lining to deform.
Good strength properties:
The temperature of the molten iron in the furnace lining is constantly changing, and the refractory material does not crack due to uneven heating; after the sintering phase change volume expansion is completed, the volume expansion must be stable during the repeated temperature changes during the melting process, and there must not be drastic expansion and contraction that causes the furnace lining to deform.
Low conductivity and good insulation performance:
The furnace lining cannot conduct electricity and must have good insulation performance when smelting metal at high temperature, otherwise it will cause leakage and short circuit accidents in the electric furnace, causing unnecessary safety problems.
Good knotting performance:
It is easy to compact and sinter, and the performance after sintering is stable, and it can be quickly formed.
No harmful impurities such as iron oxide and low melting point minerals:
Harmful impurities such as iron oxide and low melting point minerals will seriously reduce the refractoriness of the quartz sand furnace lining, so it is necessary to control their content.
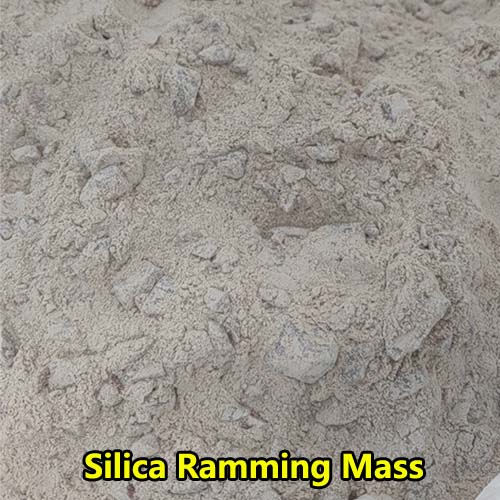