Aluminum carbon bricks are mainly composite refractory materials produced by combining alumina (such as sintered/fused white corundum, sub-white corundum, brown corundum, plate-shaped alumina, sintered bauxite, etc.) and carbon/graphite raw materials. In most cases, additives (such as SiC, Si, Al, etc.) are also added to improve their performance. According to the production method, Al2O3-C refractories can be divided into shaped Al2O3-C refractories (bricks) and amorphous Al2O3-C refractories. The former can be further divided into fired Al2O3-C refractories (fired aluminum carbon bricks) and unfired Al2O3-C refractories (unfired aluminum carbon bricks).
The bonding of unfired Al2O3-C refractories (unfired aluminum carbon bricks) after carbonization treatment or use is based on the adhesion of the coke network to the refractory particles, as well as the direct bonding of some atoms in the coke network, negative valence bonding and van der Waals forces.
Fired aluminum carbon bricks belong to ceramic bonding materials, or ceramic-carbon composite bonding materials. Fired aluminum carbon bricks are widely used as sliding bricks, long nozzle bricks, immersed nozzle bricks, upper/lower nozzle bricks, ladle integral plugs, etc. for sliding nozzles for continuous casting; while unfired aluminum carbon bricks belong to carbon bonding materials. Because aluminum carbon bricks have high oxidation resistance and resistance to corrosion by Na2O slag, they are also widely used in molten iron pretreatment equipment and as refractory materials for ladle lining.
In addition, Al2O3-C amorphous refractory materials (ramming materials, plastic materials, castable materials, vibrating materials, etc.) are also widely used. The following is a brief introduction to aluminum carbon bricks for ladle.
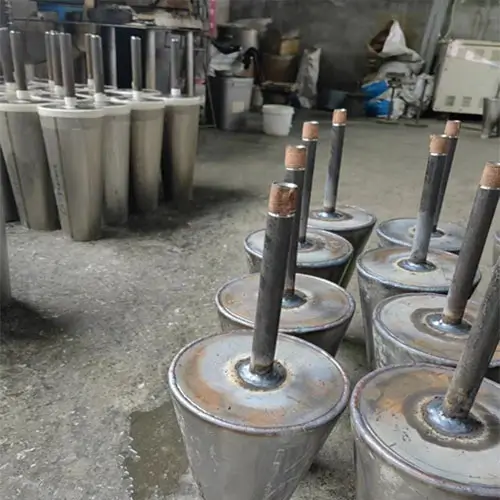
Ladle Aluminum Carbon Bricks
Traditional high-aluminum ladle lining bricks are made of sintered bauxite as the main raw material. Due to their inherent disadvantages as described below, their usage is not much:
(1) High-aluminum bricks shrink in volume, resulting in more severe penetration and erosion of molten steel and slag, and the formation of a thicker slag layer at the joints between bricks.
(2) The inherent brittleness of high-aluminum bricks and their structural characteristics cause the ladle lining to form a thicker denudation zone and slag layer.
(3) The inherent wettability of high-aluminum bricks to molten steel and slag causes more severe erosion and penetration of slag, and produces flaking.
In order to overcome the above disadvantages of high-aluminum bricks, graphite is added to the ingredients to produce Al2O3-C bricks to replace traditional high-aluminum bricks for ladle lining. This type of aluminum-carbon brick is made of corundum, sintered bauxite and graphite as the main raw materials, phenolic resin as a binder and antioxidants. Usually, the amount of graphite added is less than 12%, which basically belongs to low-carbon aluminum-carbon bricks.
Development of magnesia carbon bricks
The development and application of MgO-C composite refractories have a history of more than 40 years. They began with the tar/asphalt combined dolomite refractory developed for converters in the 1950s. At first, the service life of this carbon-containing refractory was about 100 furnaces in some steel plants. For this reason, fine magnesia powder was added to the tar/asphalt combined dolomite refractory to manufacture the so-called magnesia-dolomite bricks, which made great progress. Around the 1970s, fired oil-immersed magnesia bricks with a small number of pores became the standard lining bricks for the impact zone and other high-wear parts of the converter. At the same time, the implementation of “comprehensive lining” was implemented, that is, the implementation of partitioned lining, which achieved balanced erosion and increased service life.
In the late 1970s, magnesia-carbon bricks were successfully tested on converters, thus creating a precedent for the application of MgO-C composite refractories in converters.
In the 1980s, resin-bonded magnesia carbon bricks were developed, and the amount of carbon added was increased. At the same time, in order to reduce the burning rate of carbon, antioxidants were added to protect the carbon.
Since magnesia carbon bricks 100% utilize the characteristics of natural graphite (flakes) that are difficult to wet with slag, have high thermal conductivity and large stress relaxation capacity, they maximize the high corrosion resistance of MgO, so this type of refractory material is a revolutionary refractory material.
Later, fused magnesia, large-grained sintered magnesia, high-purity (sintered/fused) magnesia and high-purity graphite were introduced into magnesia carbon bricks to improve the material’s corrosion resistance, thereby greatly improving the service life of the converter.
Performance advantages of magnesia carbon bricks
The advantages of magnesium carbon bricks are: good resistance to slag erosion and thermal shock. The disadvantages of MgO-Cr2O3 bricks and dolomite bricks in the past were that they absorbed slag components, caused structural spalling, and led to premature damage. Magnesium carbon bricks eliminate this disadvantage by adding graphite. Its characteristics are that slag only penetrates into the working surface, so the reaction layer is limited to the working surface, with less structural spalling and long service life.
Now, in addition to traditional asphalt and resin combined magnesium carbon bricks (including fired oil-immersed magnesium bricks), magnesium carbon bricks sold on the market are:
(1) Magnesia carbon bricks made of magnesia containing 96%~97% MgO and graphite 94%~95%C;
(2) Magnesia carbon bricks made of magnesia containing 97.5% ~ 98.5% MgO and graphite 96% ~ 97% C;
(3) Magnesia carbon bricks made of magnesia containing 98.5%~99% MgO and 98%~C graphite.
According to the carbon content, magnesia carbon bricks are divided into:
(I) Fired oil-impregnated magnesia bricks (carbon content less than 2%);
(2) Carbon bonded magnesia bricks (carbon content less than 7%);
(3) Synthetic resin bonded magnesia carbon brick (carbon content is 8%~20%, up to 25% in a few cases). Antioxidants are often added to asphalt/resin bonded magnesia carbon bricks (carbon content is 8% to 20%).
Magnesia carbon bricks are produced by combining high-purity MgO sand with scaly graphite, carbon black, etc. The manufacturing process includes the following processes: raw material crushing, screening, grading, mixing according to material formula design and product setting performance, according to the combination The temperature of the agent type is raised to close to 100~200℃, and it is kneaded together with the binder to obtain the so-called MgO-C mud (green body mixture). The MgO-C mud material using synthetic resin (mainly phenolic resin) is molded in a cold state; the MgO-C mud material combined with asphalt (heated to a fluid state) is molded in a hot state (at about 100°C) forming. According to the batch size and performance requirements of MgO-C products, vacuum vibration equipment, compression molding equipment, extruders, isostatic presses, hot presses, heating equipment, and ramming equipment can be used to process MgO-C mud materials. to the ideal shape. The formed MgO-C body is placed in a kiln at 700~1200°C for heat treatment to convert the binding agent into carbon (this process is called carbonization). In order to increase the density of magnesia carbon bricks and strengthen the bonding, fillers similar to binders can also be used to impregnate the bricks.
Nowadays, synthetic resins (especially phenolic resins) are mostly used as binders for magnesium carbon bricks.
The use of synthetic resins to bind magnesium carbon bricks has the following basic advantages:
(1) The environment allows the processing and production of these products;
(2) The products can be produced under cold mixing conditions, which saves energy;
(3) The products can be processed under non-curing conditions;
(4) Compared with tar pitch binders, there is no plastic phase;
(5) Increased carbon content (more graphite or bituminous coal) can improve wear resistance and slag resistance.
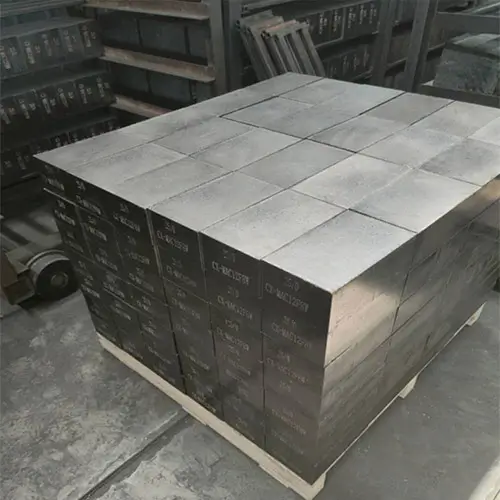