Refractory raw materials
No matter how the technology develops, refractory raw materials are the basis of refractory materials. Refractory raw materials directly determine the quality of refractory materials and affect the development of refractory materials. All the development of new refractory materials cannot be separated from the support of refractory raw materials. For example, magnesia-alumina spinel bricks, iron-alumina spinel bricks, and magnesia-iron spinel bricks cannot be separated from refractory raw materials such as magnesia-alumina spinel, iron-alumina spinel, and magnesia-iron spinel. For another example, special high-alumina bricks such as anti-stripping bricks and silica-molybdenum bricks cannot be separated from zircon, silicon carbide, andalusite, and kyanite. In addition, almost all high-grade amorphous refractories cannot be separated from micropowders including silica fume, α-alumina, and various chemical admixtures. Therefore, if you want to produce high-quality refractory materials, or develop new refractory materials, or try new refractory materials, you need to understand refractory raw materials.
Magnesium aluminum spinel
Magnesium-aluminum spinel is a refractory raw material with high melting point, small thermal expansion coefficient, low thermal conductivity, good thermal shock stability and strong erosion resistance. According to the different synthesis processes, it can be divided into sintered magnesium-aluminum spinel and fused magnesium-aluminum spinel.
Magnesium-aluminum spinel has good erosion resistance, abrasion resistance and good thermal shock stability. Its main uses are: first, it replaces magnesium-chromium sand to make magnesium-aluminum spinel bricks for cement rotary kilns, which not only avoids chromium pollution, but also has good spalling resistance; second, it is used to make ladle castables, which greatly improves the erosion resistance of steel plate linings. It is widely used in refractory materials for steelmaking. The preparation of high-quality pre-synthesized spinel provides new raw materials for the production of amorphous and shaped high-purity refractory materials.
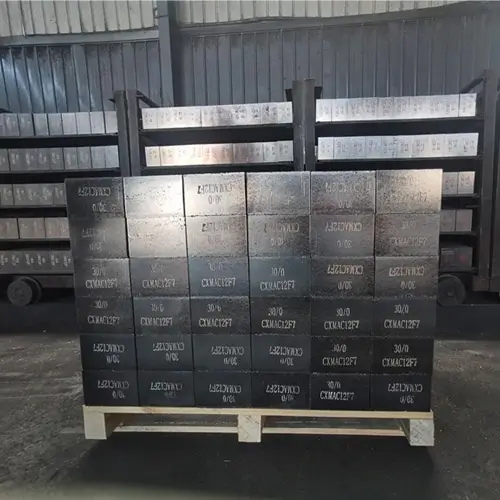
Zircon
Zircon sand has low thermal expansion, high thermal conductivity, and strong chemical stability. It is mainly used in the production of refractory materials: zircon refractory materials, such as zircon corundum bricks and zircon refractory fibers.
Zircon sand can be used to make zircon bricks for glass kilns, zircon bricks for steel ladle, ramming materials and castables; adding zircon sand to other materials can improve their performance. For example, adding zircon sand to synthetic cordierite can broaden the sintering range of cordierite without affecting its thermal shock stability; adding zircon sand to high-alumina bricks can make anti-stripping high-alumina bricks, and the thermal shock stability is greatly improved; it can also be used to extract ZrO2.
Silicon Carbide
Silicon carbide is widely used in abrasives, heating elements, refractory materials and structural ceramics for its high hardness, electrical conductivity, high temperature resistance and high strength. Commercially available silicon carbide is divided into black and green. Most of the refractory materials use black silicon carbide.
Silicon carbide has good high temperature resistance. Under normal pressure, the inconsistent melting temperature of silicon carbide is 2760℃. Silicon carbide has high strength and its flexural strength can reach 625MPa. Silicon carbide has good thermal shock resistance, which is due to its moderately low thermal expansion coefficient (4.7×10-6K-1) and high thermal conductivity [84W/(m·K)]. Therefore, silicon carbide is widely used in the production of various ceramics and refractory materials.
Andalusite, Kyanite
Both andalusite and kyanite belong to the kyanite group of minerals, and together with sillimanite are referred to as “three stones”. High-purity kyanite, andalusite, and sillimanite can be used to smelt aluminum-silicon alloys to make aircraft and ships, or to make ceramic components such as spark plugs, thermowells, and crucibles. Of course, kyanite group minerals are also used to make refractory materials. When using kyanite group minerals, it is necessary to maximize the advantages of kyanite, andalusite and sillimanite raw materials according to the needs of refractory materials technology.
① Due to the large expansion of kyanite, a smaller dosage can compensate for the high-temperature shrinkage of refractory materials. Due to its low transformation temperature, kyanite is suitable for use in refractory materials that shrink at lower temperatures. Therefore, kyanite is suitable as an additive for medium and low-grade refractory materials.
②The expansion of andalusite when heated is low, and the dosage is limited. However, compensating for the same shrinkage requires a higher dosage. As the content of andalusite increases, the creep resistance and thermal shock resistance of refractory materials will be greatly improved. However, manufacturing costs also increase significantly. Therefore, andalusite is suitable for medium and high-grade refractory materials.
Silica Fume
Silica ash is a byproduct obtained by recovering the smoke from the exhaust gas overflowing from the furnace when producing metallic silicon or ferrosilicon alloy. Under the action of the high temperature of the electric arc furnace, the quartz in the furnace is melted into SiO2 liquid, and the liquid SiO2 is reduced to Si by C. At the same time, part of SiO2 is also reduced to SiO gas. SiO gas overflows the furnace with the flue gas and is oxidized to SiO2 by O2 in the air. Subsequently, these SiO2 are condensed into glassy small balls with an average particle size of <1μm and captured by the dust collection device outside the furnace.
In addition, silica ash can also be captured when zircon is used to produce desiliconized zirconium raw materials. This silica ash can also be used to make refractory materials.
The SiO2 content of silica ash is 90%~98%, the specific surface area is 15~30m2/g, the median particle size is 0.3~0.5μm, and the pH is 5.3~7.6. Imported silica ash has a higher purity and a lower pH value. Domestic silica ash has a lower purity and a higher pH value. Domestic silica fume contains a small amount of MgO and R2O, which makes it weakly alkaline. Generally speaking, the fluidity of refractory castables prepared with imported silica fume is very good, but the raw material cost is also very high.
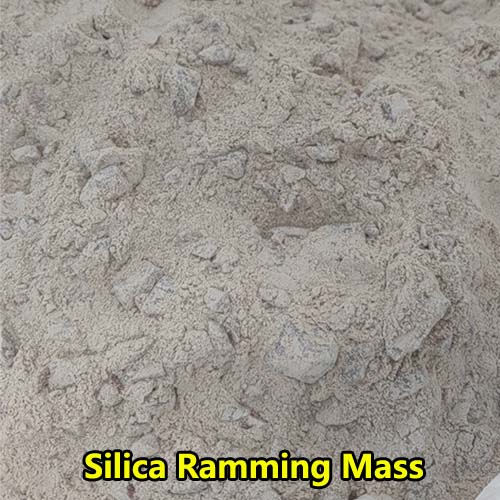
More details about Refractory Material
What is a refractory material?
Refractories are ceramic materials designed to withstand the very high temperatures (in excess of 1,000°F [538°C]) encountered in modern manufacturing. More heat-resistant than metals, they are used to line the hot surfaces found inside many industrial processes.
What is the best refractory material?
Stick with simple refractory materials that typically include monolithics, magnesite bricks, high aluminum bricks, mullite, corundum, sillimanite, castes, etc.
How to choose refractory material?
The furnace manufacturers or users have to consider the following points, before selecting a refractory.
1.Area of application.
2.Working temperatures.
3.Extent of abrasion and impact.
4.Structural load of the furnace.
5.Stress due to temperature gradient in the structures and temperature fluctuations.
6.Chemical compatibility to the furnace environment.
7.Heat transfer and fuel conservation
8.Cost considerations.
It is therefore, essential to have an objective evaluation of the above conditions. A proper assessment of the desired properties would provide guidelines for selection of the proper refractory materials.
What is basic refractory material?
Basic refractories include magnesia, CaO, dolomite, chrome, and combinations of these materials.