The ladle is responsible for the dual tasks of carrying molten steel and refining outside the furnace. With the development of steelmaking technology, my country’s ladle refractory materials have also been well developed. Especially since the 1980s, my country’s refractory research institutions, production enterprises and users have worked closely together to develop new refractory materials for ladles in accordance with my country’s national conditions, so that my country’s ladle refractory materials have developed at a faster pace and met the needs of the rapid development of my country’s steelmaking industry.
From the 1950s to the 1970s, my country’s ladle lining mainly used aluminum silicate refractory materials, including various clay bricks and high-aluminum bricks. Since the 1980s, my country has successively developed a series of new ladle refractory materials such as aluminum-magnesium (carbon), magnesium-carbon and magnesium-calcium (carbon). Among them, aluminum-magnesium (carbon) refractory materials have many varieties and full specifications, and are the main refractory materials for ladles in my country.
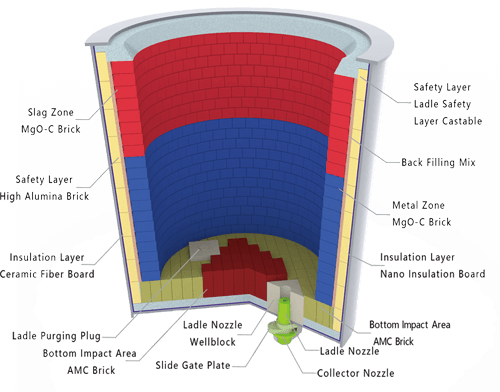
1.Aluminosilicate ladle refractories
1.Clay bricks
Clay brick is China’s earliest use of ladle refractory materials, the 20th century, 50 ~ 60 years, China’s ladle refractory materials are mainly used in a variety of clay bricks, due to the use of low-cost, until the 80s there are still a number of steel mills ladle is still used in the use of clay bricks. The physical and chemical indexes of clay bricks for ladle of a steel plant are: Al2O3 44.10%, SiO2 52.10%, Fe2O3 1.72%, apparent porosity 16%~18%, room temperature compressive strength 54.9~96.0MPa. The service life of clay ladle lining bricks varies according to the different conditions of use in each steel plant.
2.High Aluminum Brick
With the continuous development of steelmaking technology and steel production and quality continues to improve, clay ladle lining brick due to the use of short life, since the end of the 1960s, some of China’s steel mills ladle began to use a variety of high-alumina lining bricks, so that the life of the ladle has increased dramatically. Wuhan Iron and Steel flat furnace with 270t ladle from 1968 began to use second-class high alumina bricks, to 1970 the age of the package reached 25.7 times, is the clay lining bricks of 2.5 times. 1974 the age of the package reached 31.5 times. Wuhan Iron and Steel second steelmaking converter with 70t ladle from 1980 to use Al2O3 content greater than 72% of high alumina bricks, the age of 34 times, up to 50 times. Baosteel 300t ladle from June 1986, the whole package wall using a refractory materials factory production of first-class high alumina bricks, the average age of about 50 times. After the continuous casting machine put into operation, ladle use conditions deteriorate, packet lining service life is shortened. Baosteel and some refractory production enterprise cooperation, developed the use of excellent performance micro-expansion of high alumina brick, in April 1992 the official use of A factory products, the average service life of 81.5 times, the highest life of 100 times. The average service life of the products from Plant B is 78.6 times, and the highest service life is 122 times (continuous casting ratio is 55.73%). TISCO 70t ladle using high aluminum lining brick, service life of 64.3 times. In short, China’s ladle after the use of high aluminum lining brick, so that the service life of the ladle significantly improved to ensure the smooth progress of steel production, and promote the further development of the steel industry.
3.High-alumina pounding material
At the end of the 1970s, some steel mills in China use high alumina pounding material for ladle lining, which has achieved good results. High-alumina pounded material is high-quality high alumina bauxite clinker as raw materials (aggregate and fine powder), industrial phosphoric acid as a binding agent, after batching, mixing and formulated into a plasticity of a good non-conformable refractory materials. Adopting the whole pounding technology, it is made into the whole package lining, which obtains a long service life.
4.Waxed stone tiles
Wax stone brick is a kind of sintered products produced by foliated wax stone as the main raw material.In the early 1970s, a refractory factory in Fujian produced wax stone ladle bricks in Maanshan Iron and Steel, Anshan Iron and Steel, Shanghai Iron and Steel three factories, Sanming Iron and Steel and other iron and steel enterprises in different types of ladle on trial. The results show that the use of wax stone brick performance is better than the use of clay bricks and third-class high alumina bricks. Used on 15t ladle of Masteel, the life span reached 66 times. Wuhan Iron and Steel two steelmaking plant 70t ladle also tried the production of the plant’s SiO2 content of 72% of the wax stone brick, but the effect is not very satisfactory, the service life of only 14 times. Baosteel 300t ladle in September 1985 to 1988 years have been used in Japan imported wax brick, the average life expectancy of 38 times. The physical and chemical indexes of wax stone brick for ladle produced by a factory are as follows: SiO2 78.95%, Al2O3 18.85%~19.51%, Fe2O3 0.44%~0.52%, apparent porosity 14%~18%, normal temperature compressive strength 32.9~62.9MPa. Due to various reasons, wax stone brick has not been popularized and applied to the ladle in our country.
2.Aluminum and magnesium (carbon) ladle refractory materials
From the 1980s, China’s steelmaking industry into a rapid development stage, continuous casting and furnace refining and other modern steelmaking technology to promote the application of clean steel production and the increase in the use of ladle refractory materials to make the use of more severe conditions. Steel temperature rise, steel in the ladle to extend the residence time, steel and slag on the ladle refractory materials and slag on the ladle refractory materials of chemical erosion are more serious, the previous ladle refractory materials have been unable to meet the needs of modern steel production. For this reason, China has developed a variety of aluminum and magnesium (carbon) quality ladle refractories. Aluminum and magnesium (carbon) refractories in the process of use, Al2O3 and MgO in the high temperature reaction to generate magnesium-aluminum spinel this high-temperature performance of minerals, so that the refractory erosion resistance and anti-flaking performance significantly improved. Therefore, the use of aluminum and magnesium (carbon) ladle refractories can greatly improve the service life of the ladle.
1.Aluminum-magnesium monolithic pounding material
In the early 1980s, Lonai Institute, Anshan Coke & Patience Institute and Anshan Iron & Steel cooperated and jointly developed the aluminum-magnesium ladle overall pounding material. The pummeling material is a kind of plasticity good indefinite refractory material formulated with special high alumina bauxite clinker as aggregate, special high alumina bauxite clinker powder and sintered magnesium sand powder mix as matrix, and liquid water glass as binding agent. It was used in 200t ladle of Anshan Iron & Steel, and its life expectancy was 5-7 times higher than that of clay bricks, with an average life expectancy of 85.15 times and a maximum of 108 times, and the consumption of refractory material per ton of steel was 2.7 kg. In June 1982, the pounding material passed the appraisal of the former Ministry of Metallurgy. After that, the ladle of many steel mills in the country successively used this aluminum-magnesium ladle overall pounding material, have achieved good results.
2.Aluminum and magnesium castables
Following the aluminum and magnesium pounding material, China has developed the aluminum and magnesium castable with high-quality high alumina bauxite clinker and sintered magnesium sand as raw materials and liquid water glass as binding agent. The castable “Sixth Five-Year Plan” period first in the small steel ladle on the popularization and application, and achieved good results. Such as a steel plant in Hebei 10t and 14t ladle using water glass combined with aluminum and magnesium castables, the average age of a package for 109.7 times, is more than 8 times the clay brick lining. Heilongjiang a steel plant 15t and 13t ladle, the use of aluminum and magnesium castables, a package age of 53 times, while the clay lining brick package age is only 6 to 10 times. During the “Seventh Five-Year Plan” period, the whole ladle cast lining technology was listed as the former Ministry of Metallurgy’s key new technology promotion projects in the country. By the third quarter of 1987, China’s 30t converter with small and medium-sized ladle (45t capacity), most of the overall cast lining. Overall cast lining life in 40 to 60 times, some small ladle up to 90 times. Refractory consumption and lining costs have decreased significantly, and obvious economic benefits have been achieved. A steel mill ladle water glass combined with aluminum and magnesium castables physical and chemical indicators for Al2O3 75.20%, MgO 9.47%, SiO2 10.25%, bulk density (110 ℃ × 24h) 2.67 ~ 2.73g./cm3, room temperature flexural strength (110 ℃ × 24h) 14.9MPa.
3.Aluminum-magnesium unfired bricks
In addition to aluminum and magnesium pounding material, aluminum and magnesium castables, China has also developed a combination of water-glass aluminum and magnesium non-burning bricks, used in the ladle, the life of the ladle than the traditional aluminum silicate ladle bricks long. Bensteel 160t ladle using aluminum and magnesium unburnable bricks, the average life of 40.56 times, than the use of third-class high alumina bricks (life of 18.5 times) to improve more than 1 times. Tianjin three steelmaking plant 20t ladle using aluminum and magnesium unburnable brick average life 38.8 times, up to 55 times, is clay lining brick life (9 times) more than 4 times. A factory production of water glass combined with aluminum and magnesium unburnable brick physical and chemical indicators are: Al2O3 68.46% ~ 74.07%, MgO 7.65% ~ 12.32%, SiO2 9.02% ~ 13.37%, Fe2O3 1.12% ~ 1.83%, bulk density of 2.48 ~ 2.86g/cm3, the apparent porosity of 16% ~ 23%, the room temperature compressive strength of 55.6 ~ 123MPa. 55.6~123MPa.
4.Magnesium-aluminum spinel castables
In the early 1990s, with the bauxite-based synthetic magnesium-aluminum spinel put into industrial production, a number of refractory research institutes and production enterprises in China have developed a variety of different performance of bauxite-based magnesium-aluminum spinel castables for ladle. Because of this kind of castables with a certain proportion of pre-synthesized magnesium and aluminum spinel, so that the anti-erosion performance and anti-flaking performance of the castables is greatly improved, and its performance is better than the water-glass combination of aluminum and magnesium castables. It has been used in various types of ladle and achieved good results. Luonaiyuan and a refractory factory in Henan jointly developed bauxite-based aluminum-magnesium spinel castables by TISCO 70t (DH vacuum lance blowing argon) ladle, HISCO 30t continuous casting ladle (continuous casting ratio of not less than 94%) trial, the average life of up to 71 and 114 times, respectively, than the water-glass bonded aluminum-magnesium castables to improve the respectively 1 to 3 times. Hangzhou, a steel plant 25t continuous casting (continuous casting ratio of more than 70%) ladle using magnesium-aluminum spinel castables, the average package age of 77 times, than the water-glass combination of aluminum and magnesium castables to improve 1.2 times. Jiangxi New Steel a steelmaking plant 28t ladle using magnesium aluminum spinel castables, the average life of 79 times, than the water glass combined with aluminum magnesium castables increased by 1.6 times. Bauxite-based magnesium-aluminum spinel castables are made of high-quality high-alumina bauxite clinker as aggregate, high-quality high-alumina bauxite clinker powder, synthetic magnesium-aluminum spinel powder and sintered magnesium sand powder as matrix, and the binding agents are: polyphosphate, SiO2 micropowder, Al2O3 micropowder, and pure calcium aluminate cement. The physical and chemical indexes of bauxite-based magnesium-aluminum spinel castables produced by a factory are as follows: Al2O3 68.84%, MgO 14.63%, SiO2 11.27%, Fe2O3 1.74%, bulk density (110℃×24h) 2.73g/cm3, room temperature compressive strength of 42.88MPa, room temperature flexural strength of 55.1MPa.
5.Aluminum-magnesium-carbon bricks
In the 1990s, is the rapid development of China’s continuous casting technology period, high-efficiency continuous casting technology has become the center of gravity of its development. In order to improve the service life of continuous casting ladle, to adapt to the needs of the development of high-efficiency continuous casting technology, our country has developed a ladle with aluminum magnesium carbon bricks for various types of continuous casting ladle, so that the service life of the ladle greatly improved. Luonai hospital, baosteel and jiaozuo a refractory materials factory co-developed aluminum magnesium carbon ladle bricks in baosteel 300t continuous casting ladle on the use of ladle age from the use of first-class high alumina bricks more than 20 times, increased to more than 80 times, the highest reached 126 times. Anshan Iron and Steel three steelmaking 200t all continuous casting and furnace refining ladle, the use of aluminum-magnesium carbon bricks, the average life expectancy of 64 times, up to 73 times. 1993 ladle with high-quality aluminum-magnesium carbon bricks with the popularization of the use of the full-scale in our country, many of the country’s steel mills, according to the actual situation of the enterprise, one after another, the use of aluminum-magnesium carbon ladle lining bricks, so that the ladle’s life expectancy significantly improved, such as Pangangang 160t ladle using aluminum-magnesium carbon lining bricks, the average life expectancy increased to 90 times, the average life expectancy of the ladle lining bricks. After using aluminum-magnesium-carbon lining bricks, the average life expectancy has increased to 90 times, with a maximum of 115 times. Aluminum-magnesium-carbon bricks are made of special high-alumina bauxite clinker, electrofused magnesium sand or sintered magnesium sand and graphite as raw materials, and liquid phenolic resin as binding agent.
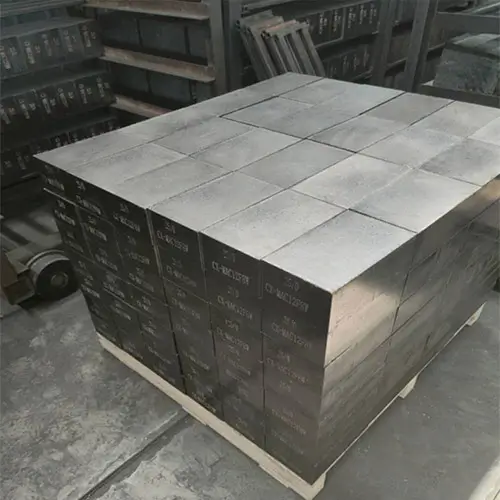
6.Magnesia-aluminum spinel carbon bricks
In the development of aluminum-magnesium carbon bricks on the basis of China has developed a steel ladle with magnesium-aluminum spinel carbon bricks. Aluminum-magnesium spinel carbon brick is added to a certain proportion of pre-synthesized magnesium-aluminum spinel in the brick material, and its performance is better than that of the same grade of aluminum-magnesium carbon brick. Jiaozuo a refractory factory and Baosteel cooperation in the development of magnesium and aluminum spinel carbon brick in Baosteel 300t continuous casting ladle on the use of the average service life of 105 times, up to 200 times. The magnesium-aluminum spinel carbon bricks developed by the General Research Institute of Architecture are used in Anshan Iron and Steel’s 200t continuous casting ladle with out-of-hearth refining, with an average service life of 73.3 times and a maximum of 82 times. Shougang and xinxiang a refractory materials factory cooperation development of aluminum magnesium spinel carbon brick in shougang two steel 90t ladle on the use of life from the original use of aluminum magnesium carbon brick 20 times to 40 times, up to 51 times. The development and use of aluminum-magnesium spinel carbon brick, so that the service life of China’s continuous casting ladle has been further improved.
7.High-grade aluminum and magnesium unburnable bricks
Carbon-containing ladle lining bricks will cause carbonization of molten steel in the process of use, which is very unfavorable to the smelting of clean steel, low carbon steel and ultra-low carbon steel. In order to meet the needs of clean steel, low carbon steel and ultra-low carbon steel smelting, the development of high-grade aluminum and magnesium non-burning bricks (no carbon non-burning bricks). High-grade aluminum and magnesium non-fired brick and the early 1980s development of water-glass combination of aluminum and magnesium non-fired brick compared to a qualitative leap. In addition to the use of high-purity raw materials (corundum, high-purity fused magnesia and high-purity aluminum-magnesium spinel, etc.), the bonding agent also uses high-performance composite bonding agent. High-grade aluminum and magnesium non-burning bricks in the ladle on the use of good results, the service life to meet or even exceed the carbon ladle lining bricks, while reducing the carbon increase in molten steel. Such as Henan a refractory materials company developed aluminum and magnesium not burning brick, in a steel plant 100t ladle and LF refining ladle on the use, life is aluminum and magnesium carbon brick 1.5 times. Anshan steel 200t ladle using aluminum-magnesium non-burning brick a package age of more than 110 times, up to 128 times. 170t continuous casting ladle service life of 119 times, more than the aluminum-magnesium carbon brick. Baosteel 300t continuous casting ladle from June 1998 to stop using aluminum-magnesium carbon bricks, began to use high-grade aluminum-magnesium non-burning bricks.
8.High-grade aluminum and magnesium (spinel) castables
In the mid-1990s, China developed high-grade aluminum and magnesium castables for large and medium-sized ladles. The raw materials used in high-grade aluminum and magnesium (spinel) castables are corundum (fused corundum, sintered corundum, etc.), high-purity fused magnesium sand, high-purity aluminum and magnesium spinel (fused and sintered) and so on. The binding agents are pure calcium aluminate cement, Al2O3 micropowder, high purity SiO2 micropowder, etc. Baosteel 300t ladle from December 1996 began to try our refractories factory developed high-grade aluminum and magnesium castables, to 2000 the average service life of 258 times. Shougang three steel mills and a refractory company in Xinxiang developed high-grade aluminum and magnesium spinel castables, three steel mills in Shougang 90tLF refining ladle on the use of life of 138 times, the erosion rate of 0.62mm / times. Anshan Iron and Steel three refining steel plant 200t continuous casting ladle using high-grade aluminum and magnesium (spinel) castables, service life of 150 times. There are also steel mills using castables prefabricated blocks, also achieved very good results. Such as Bensteel ladle using aluminum-magnesium carbon brick life of 65 times, changed to high-grade aluminum-magnesium spinel prefabricated blocks, the average service life increased to 118 times, the highest reached 126 times. By 2000, 90% of the steel ladle of Bensteel adopts high-grade aluminum and magnesium casting material prefabricated block lining.
3.Magnesium-carbon ladle refractories
1.Magnesium carbon bricks
Magnesia carbon bricks have excellent erosion resistance and spalling resistance. Magnesia carbon brick in the ladle is mainly used in the slag line parts, while the non-slag line parts use other refractories (castables, unburnable bricks, etc.), which can obtain a high service life, but also reduce the cost of refractory materials. A steel mill ladle slag line with magnesium carbon brick physical and chemical indicators for MgO 77.4%, C 16.75%, apparent porosity 3.1%, bulk density 2.90g/cm3, room temperature compressive strength of 38.6MPa. 1981 September WISCO two steel mills took the lead in the 70t ladle slag line using magnesium carbon brick, service life of 50 times, due to non-slag line parts of the high alumina brick damage is serious and out of use. Baosteel 300t ladle slag line from July 1989 began to use MT-14A magnesium carbon bricks, slag line life is maintained at more than 100 times. A steel mill 90tLF refining ladle slag line using carbon content of about 16% of the magnesium-carbon bricks, slag line life of 95 times. There are also steel mills ladle with full magnesium-carbon brick lining, such as a steel plant with 60tLF-VD electric furnace refining ladle, full magnesium-carbon brick lining, the average life expectancy of 47 times, up to 57 times.
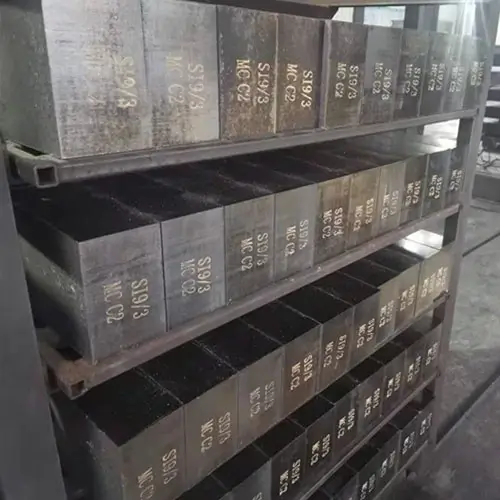
2.Low carbon magnesium carbon bricks
Steel ladle slag line using magnesium carbon bricks exist in the steel carbon problem, in recent years, some steel mills and refractory manufacturers to cooperate, the development of a low carbon steel ladle slag line magnesium carbon bricks. Baosteel 300t ladle slag line tried carbon content of less than 7% and less than 5% of the low-carbon magnesium-carbon bricks, the service life of up to 110 times or so, and ordinary magnesium-carbon bricks comparable to basically meet the requirements of the use of 300t ladle. Anshan steel ladle slag line also used in the carbon content of 5% or less of the low-carbon package lining brick, the use of good results.
4.Magnesium-calcium (carbon) refractories for ladles
Magnesia-calcium refractories have good high-temperature stability and resistance to high alkalinity slag, especially the free CaO in them has the effect of purifying the steel, therefore, magnesia-calcium refractories are one of the ideal refractories for ladle. With the increasing production of clean steel, the application of magnesium-calcium refractories will continue to expand.
1.Dolomite pounding material
In the early 1980s, TISCO to ordinary sintered dolomite as raw material, medium temperature asphalt as a binding agent made of dolomite pounding material, used in 70t ladle, achieved good results, the average life of 76 times, up to 112 times.
2.Non-fired magnesium-calcium bricks
At the beginning of 1990s, Lonai Academy developed the non-burning magnesium-calcium bricks for ladle with synthetic magnesium-calcium sand and electrofused magnesium sand as the raw material, and solid inorganic salt and inorganic salt solution as the combining agent, and used them on 40tLF-VD refining ladle of a steel plant in Shanghai, with the life span of more than 40 times, and the oxygen content of the steel decreased from 12.2×10-6 to 11.13×10-6. In 1992, the product passed the appraisal of the former Ministry of Metallurgy, and then was used on the refining ladle of Great Wall Special Steel and other steel plants. In 1992, the product passed the appraisal of the former Ministry of Metallurgy, and then it was used in the refining ladle of Great Wall Special Steel Plant and other steel mills. In recent years, a refractory company developed anhydrous resin-bonded non-burning magnesium-calcium bricks, which were used in a steel company’s 100tLF refining ladle, with a life span of 80-85 times and an erosion rate of 1.28-1.37mm/times. In July-August 2006, Shandong Magnesium Mining cooperated with a refractory factory to develop non-burning magnesium-calcium bricks, which were used in a steel factory’s 90tLF refining ladle (refining rate of 100%). 100%) package wall non-slag line parts used, life expectancy of more than 60 times. Because of the bottom of the package breathable brick serious erosion and discontinued, not burned calcium magnesium brick thickness of 130mm or so, can continue to use, is expected to normal package age up to 80 ~ 100 times.
3.Non-fired magnesium-calcium-carbon bricks
At the beginning of this century, Shougang Second Steelmaking Plant cooperated with a refractory company to develop a non-burning magnesium-calcium-carbon brick with synthetic magnesium-calcium sand, electrically fused magnesium sand and high-purity graphite as raw materials, and anhydrous resin as binding agent for the non-burning magnesium-calcium-carbon brick, which is used for the non-slag line part of 225t ladle of Shougang Second Steelmaking Plant (magnesium-carbon bricks for slag line) with an average service life of 116.8 times, and the average life is 116.8 times, and the average service life is 37.57 times, compared with that of the original aluminum-magnesium-carbon bricks with the thinning of the wall of the ladle by 20mm. Compared with the original aluminum-magnesium-carbon bricks, the average service life is 116.8 times. And the oxygen content in the steel and non-metallic inclusions have been reduced. There are also some steel mills in China in SKF and LF-VD and other refining ladle slag line parts of the use of magnesium and calcium carbon bricks, achieved good results.
5.Zirconium bricks
Between September 1985 and 1989, Baosteel 300t ladle used zirconium ladle lining bricks imported from Japan, with an average service life of 90 times. During this period, a refractory factory in wuxi with domestic raw materials also developed a zirconium ladle lining brick, in baosteel 300t ladle on trial, the life of 88 times, due to the bottom of the ladle sliding plate mechanism failure and stop using. Domestic zirconium ladle brick physical and chemical indicators: ZrO2 60.80%, Al2O3 1.76%, Fe2O3 0.60%, bulk density of 3.53g/cm3, the apparent porosity of 19%, room temperature compressive strength of 62.9MPa.
In summary, since the 1950s, with the continuous development of China’s steelmaking technology, China’s ladle refractories are also moving forward, new product varieties continue to increase, product quality continues to improve, the use of better and better, to meet the needs of China’s steelmaking industry continues to develop. According to the development trend of China’s steelmaking industry, it is suggested that the future development of refractory materials for ladle should be carried out in the following aspects.
(1) Develop refractories for ladle with longer service life to meet the needs of high-efficiency continuous casting and out-of-hearth refining.
(2) Develop low-carbon, carbonless and magnesium-calcium series of ladle refractories with better erosion resistance and spalling resistance to meet the needs of smelting clean steel, low-carbon steel and ultra-low-carbon steel.
(3) Develop energy-saving refractories for ladle, such as indeterminate refractories and unburnt bricks.
(4) Develop resource-saving and environment-friendly refractories for ladle.
(5) Carry out research on the reuse of various residual steel ladle refractories after use.