High alumina refractory bricks play an extremely important role in industrial furnaces due to their excellent high temperature resistance. According to different classification standards, high alumina refractory bricks can be subdivided into multiple types to meet various specific application requirements. The following are the main classification methods of high alumina refractory bricks:
Classification according to aluminum oxide content
Ⅰ grade high alumina bricks: alumina content ≥75%.
Ⅱ grade high alumina bricks: alumina content between 60% and 75%.
Ⅲ gradehigh alumina bricks: alumina content between 48% and 60%.
Classification according to mineral composition
Low mullite (diorite) high alumina bricks: contain a low percentage of mullite.
Mullite high alumina bricks: mullite is the main mineral component.
Mullite-corundum high alumina bricks: mullite mixed with corundum as the mineral component.
Corundum-mullite high-alumina bricks: mineral composition of corundum mixed with mullite.
Corundum-mullite high-alumina bricks: corundum is the main mineral composition, when the alumina content reaches 90% or more, usually called corundum bricks.
Classification according to production process and use
Ordinary high alumina bricks: standard fired bricks, the main mineral composition is mullite, corundum and glass phase. Widely used in blast furnace, hot blast furnace, electric furnace roof, blast furnace, reflector furnace, rotary kiln lining.
Modified High Alumina Bricks: Including high load soft high alumina bricks, micro-expansion high alumina bricks, low creep high alumina bricks, and phosphate bonded high alumina bricks, etc. These types of high alumina bricks are usually designed to meet specific high temperature performance needs.
Special grade high alumina brick: a special building material, high alumina products fired from calcined bauxite as the main raw material, with good refractoriness, load softening temperature, high temperature volumetric stability, slag resistance, abrasion resistance and so on.
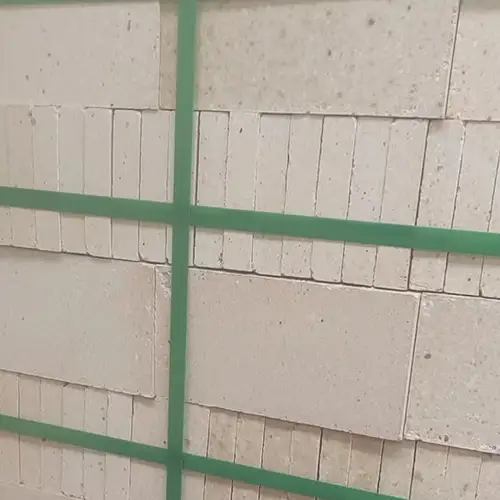
Classification according to shape
Standard Brick: the most common shape with uniform dimensions.
Plain Brick: Similar to the standard brick, but may vary slightly in size.
Wedge-shaped bricks: have a beveled surface and are used for special kiln designs.
Shaped bricks: Various shapes, customized to the requirements of the specific area of use.
Special shaped bricks: more specialized shapes, often requiring special design for specific kiln configurations.
Classification by use
Primary high alumina bricks, secondary high alumina bricks, tertiary high alumina bricks, special high alumina bricks, corundum bricks, low creep high alumina bricks, dense high alumina bricks, aluminum carbide high alumina bricks, red stalactite high alumina bricks and so on, these types of high alumina bricks according to the use of different occasions and choose.
Classification by number
According to different national standards, high alumina refractory bricks will have different numbers, for example, LZ series, in which LZ stands for the initial letters of the aluminum bricks in hanyu pinyin, and the number after it indicates the mass fraction of alumina.
Selection basis
The selection of high alumina refractory bricks needs to be decided according to the specific use environment and demand. For example:
Where high strength and high refractoriness are required, special high alumina bricks or corundum bricks with higher alumina content may be chosen. And where corrosion resistance is required, low creep high alumina bricks or spalling resistant high alumina bricks might be chosen. Each type of high alumina refractory brick has its own specific applications and advantages, and the correct choice of the right high alumina refractory brick is essential to ensure the stable operation and prolonged service life of industrial furnaces and kilns.