Aluminum Carbon Brick
Aluminum carbon bricks are mainly produced using alumina (such as sintered/electrofused white corundum, sub white corundum, brown corundum, plate alumina, sintered bauxite, etc.) and carbon/graphite raw materials with the production of composite refractory materials in most cases, but also to add additives (eg, SiC, Si, Al, etc.), in order to improve its performance. According to the production method, Al2O3-C refractories can be divided into shaped Al2O3-C refractories (bricks) and unshaped Al2O3-C refractories, the former can be further divided into fired Al2O3-C refractories (fired aluminum-carbon bricks) and unfired Al2O3-C refractories (unfired aluminum-carbon bricks).
The bonding of unfired Al2O3-C refractories (unfired aluminum-carbon bricks) after carbonization or use is based on the adhesion of the coke network to the refractory particles, as well as on the direct bonding of some of the atoms within the coke network, negative valence bonding, and van der Waals forces.
Fired aluminum carbon brick belongs to the ceramic bond material, or belongs to the ceramic – carbon composite junction > type fired aluminum carbon brick is used as a large number of continuous casting with sliding spout sliding plate brick, long spout brick, immersed spout brick, up / down spout brick, the whole plug bar, etc.; and do not burn the aluminum carbon brick belongs to the carbon bond material due to the high oxidation resistance and resistance to the erosion of the Na2O system slag performance of the aluminum carbon brick, so it is also widely used in the pre-treatment of iron and steel equipment In addition, Al2O3-C bricks are also widely used in iron pre-treatment equipment, and also used as refractory materials for ladle linings.
In addition, Al2O3-C quality amorphous refractories (pounding material, plastic, casting material, vibrating material, etc.) also have a wide range of applications. The following is a brief introduction to aluminum carbon bricks for ladle.
Aluminum carbon bricks for steel ladle
Conventional high alumina ladle lining bricks are made from sintered bauxite as the main raw material, and they are not used much anymore because of their inherent disadvantages as described below:
(1) The existence of volume contraction of high alumina bricks leads to more serious penetration and erosion of steel and slag, as well as the formation of a thicker slag layer at the joints between bricks and bricks.
(2)The brittleness between the high alumina bricks themselves and their organizational and structural characteristics make the ladle lining form a thicker spalling zone and slag layer.
(3) The inherent wettability of high alumina bricks to steel and slag leads to more serious erosion and penetration of slag, and produces flaky spalling.
In order to overcome the above shortcomings of high alumina bricks, that is, to add graphite to the ingredients, the production of Al2O3-C bricks instead of the traditional high alumina brick masonry ladle lining. This kind of Al2O3-C brick is made of corundum, sintered bauxite and graphite as the main raw materials, and phenolic resin as the binding agent and added antioxidant. Usually, the graphite content is less than 12%, basically belongs to the low carbon aluminum carbon brick.
Development of magnesium carbon bricks
MgO-C composite refractories have been developed and used for more than 40 years, starting with tar/asphalt bonded dolomitic refractory village materials developed for converters in the 1950s. At first, the service life of this carbon-containing refractory in some steel mills was about 100 furnaces. For this reason, the so-called magnesium-dolomite bricks were manufactured by incorporating magnesium sand fines into the tar/asphalt-bonded dolomitic refractory material, which led to considerable progress. Around the 1970s, the number of pores is very small fired oil-impregnated magnesium bricks to become a converter impact zone and other high wear parts of the standard lining bricks, while the implementation of the “integrated furnace lining” that is, the implementation of the lining of the sub-district, but to achieve a balanced erosion, and improve the service life.
In the late 1970s, magnesium and carbon bricks in the converter on the successful test, thus creating a factory MgO-C quality composite refractories in the converter on the application of the precedent.
In the 1980s, the resin bonded magnesium carbon brick has been developed, and then also increased the amount of carbon into the same time, in order to reduce the burning rate of carbon, add antioxidants to protect carbon.
Due to the magnesium carbon brick 100% of the use of natural graphite (scale) is difficult to wet with the slag, high thermal conductivity and stress relief capacity and other characteristics, maximize the high corrosion resistance of MgO performance, so this type of refractories is the refractory materials.
Later, electrofused magnesium sand, large grain sintered magnesium sand, high purity (sintered/electrofused) magnesium sand, etc. and high purity graphite were introduced into magnesium carbon bricks to improve the material’s resistance to corrosion, thus greatly improving the service life of the converter.
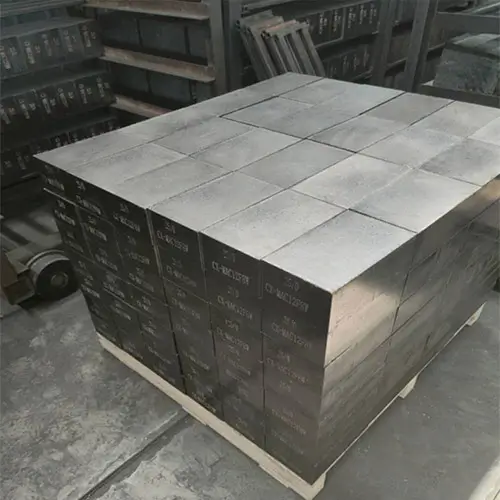
Performance advantages of magnesium carbon bricks
The advantages of magnesium-carbon bricks are: good resistance to slag erosion and thermal shock. Previously, the disadvantage of MgO-Cr2O3 bricks and dolomite bricks is the absorption of slag components, resulting in structural spalling, leading to overrun damage magnesium-carbon bricks eliminated this disadvantage through the addition of graphite, which is characterized by the slag is only penetrated into the working surface, so the reaction layer is confined to the working surface, with less structural spalling and a long service life.
Now, in addition to the traditional asphalt and resin bonded magnesium carbon bricks (including fired oil impregnated magnesium bricks), magnesium carbon bricks sold on the market are:
(1) Magnesia-carbon bricks made of magnesia sand containing 96%~97% MgO and graphite with 94%~95% C; (2) Magnesia-carbon bricks made of magnesia sand containing 97.5%~98.5% MgO and graphite with 96%~97% C.
(2) Magnesia-carbon bricks made of magnesia sand containing 97.5%~98.5% MgO and graphite with 96%~97%C; and
(3) Magnesia carbon bricks made of magnesia sand containing 98.5%~99% MgO and graphite with 98%~C.
According to the amount of carbon content, magnesium carbon bricks are divided into:
(1) Fired oil-impregnated magnesium bricks (carbon content less than 2%).
(2) Carbon bonded magnesium bricks (carbon content less than 7%); and
(3) Synthetic resin-bonded magnesium-carbon bricks (carbon content of 8% to 20%, and in a few cases up to 25%). Antioxidants are often added to the asphalt/resin-bonded MgC brick (carbon content of 8% to 20%).
Magnesium carbon bricks are produced by combining high-purity MgO sand with scaled graphite and carbon black, and their manufacture has the following processes: crushing, sieving and grading of raw materials, mixing according to the design of material formulas and the set performance of the products, warming up to close to 100-200°C according to the type of bonding agent, mixing with the bonding agent in order to obtain the so-called MgO-C clay (billet mixture). The MgO-C clay using synthetic resins (mainly phenolic resins) is molded in the cold state, and the MgO-C clay using bitumen (heated to a fluid state) is molded in the hot state (at a temperature of about 100° C.). Depending on the batch size and performance requirements of the MgO-C products, the molding can be performed using vacuum vibration equipment, compression molding equipment, extruders, isostatic presses, hot presses and warming equipment, and tamping equipment to process the MgO-C sludge to a desired shape. The formed MgO-C billet is placed in a kiln at 700~1200°C for heat treatment to convert the binding agent into carbon (this process is called carbonization). In order to improve the density of magnesium-carbon bricks and strengthen the bond, a filler similar to the binding agent can also be used to impregnate the brick blanks.
Nowadays, synthetic resins (especially phenolic resins) are mostly used as the binding agent of magnesium-carbon bricks. The use of synthetic resin binding magnesium carbon brick has the following basic advantages:
(1) The environmental aspects allow for the processing and production of these products; and
(2) The process can be produced under cold mixing conditions which saves energy.
(3) The products can be processed under non-maintenance conditions.
(4) no plastic phase exists compared to tar pitch binders; and
(5) Increased carbon content (more graphite or bituminous coal) improves wear and slag resistance.
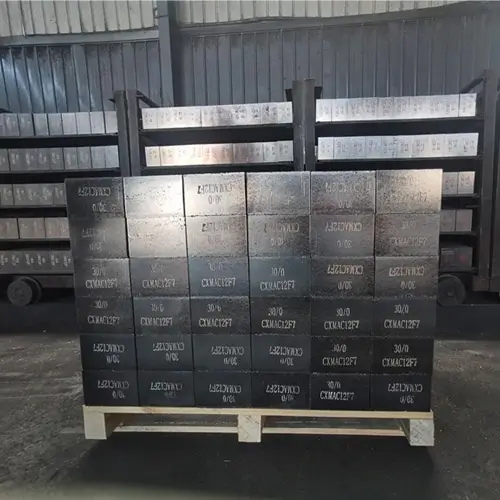