Technical Requirements for Construction of Furnace Roof Plasticizable
1.Pounding construction order
Generally from the heating furnace furnace length direction of one end, in turn to the other end of the pounding construction, can also start from both ends at the same time to the middle of the pounding construction, can also be segmented pounding construction. In order to reduce the doorway, it is best to start from one end to the other end of the construction in turn, so that the entire roof is only a doorway.
2.Mold supporting method
Furnace top can be plastic construction, generally use the pulling mold supporting mode, tie rod transverse spacing according to the length of the template adjustment, in order to facilitate the placement of the template. At present, generally in accordance with the P3015 standard in the construction of steel mold plate length 1.5m spacing. In order to ensure the strength of the pulling mold lifting and pulling, the longitudinal tie rod is generally not more than 1.5m spacing.
3.Spreading and pounding
Only a single row of material can be laid in each layer, the air hammer should be perpendicular to the pounding surface, and start pounding from the joints of material blanks. The hammer head should move vertically between the upper and lower templates, and the hammer marks should overlap 2/3, and the rows and rows should overlap 1/2, at least once round trip. The pounding should be smooth, dense and uniform. After each layer of pounding, scrape the surface of the pounding, and then lay down a layer of plasticizer. Plastic pounding, the upper template should be pressed, so as not to plastic the upper part of the pounding is not solid, affecting the overall strength of the roof plastic.
4.Construction time control
Furnace roof plasticizable construction should be carried out continuously, and plastic sheet should be applied to cover the pounding surface during the intervals to prevent moisture dissipation. If the construction is interrupted for a long time, the joints should be left at the centerline of the two rows of anchored bricks, and when the construction is continued, the dried surface should be cut down and scraped.
5.Anchor brick installation
Before installing the roof anchoring brick, should be wedged with the real brick with the same tooth shape of the wooden mold brick, pounded into the plastic more than 20mm, the formation of tooth marks, remove the wooden mold brick, and then the anchoring brick pounding embedded, wedge tightly fixed. Anchor brick and hanging beams must be wedged tightly between, and in a state of force, to prevent the furnace roof sinking when the mold is removed. Incomplete pounding of the coroplast will result in gaps around the anchoring bricks. In the process of baking and using the furnace, the fire phenomenon will appear at the gap around the anchoring brick.
6.Close the door construction
It is preferable to choose the location where there are fewer obstacles in the horizontal roof section. The width of the door should be not more than 600mm, and pounded into a funnel. The plastic at the door should be broken, as small as possible, layered material, pounded in layers.
Demolding and trimming after construction of furnace roof coroplasts
After the construction of plastic, after the construction body reaches a certain strength, the mold should be dismolded and trimmed in time. Demolding time is generally determined according to the ambient temperature, due to pounding after the plastic itself already has a certain strength, so demolding time is shorter than the casting material, plastic demolding should be no earlier than 4h after the construction. demolding, the construction of the body should be immediately after the scraping, cut expansion joints, zapping holes and other trimming construction. Before trimming, the plastic around the end face of the anchored brick should be gently tapped with a wooden hammer, so that it is tightly bitten, and then take the end face of the anchored brick as the benchmark to cut off the excess.
1、Scraping
After demolding, scraping with nail tooth plate is helpful to exclude the moisture of furnace lining and avoid cracks.
2、 Expansion joint
Plastic lining heated surface of the expansion joints cut according to the design position, expansion joints should be through, spacing 1.2 ~ 1.5 m. Expansion joint width is generally 3 ~ 5mm, depth 80mm. expansion joints should not be cut too deep, because the oven can not be accurately before the top of the furnace to find the expansion joints from the top of the location, so can not be pressed with the clay bricks to prevent the formation of penetrating cracks in the use of the phenomenon of leaping fire occurs. Cut the expansion joint construction.
3、 Tie the ventilation hole
With a diameter of 03 ~ 4mm small pointed brazier in the plastic heated surface tie ventilation holes, the depth of the thickness of the furnace lining 2 / 3, spacing is generally 150 ~ 200mm.
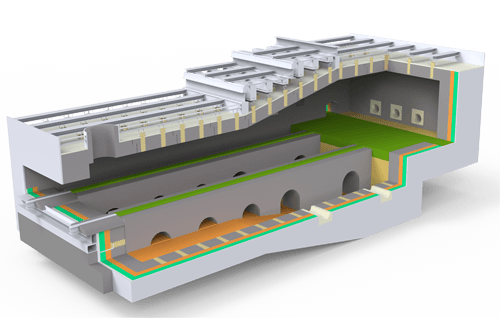
Furnace top coroplast construction precautions
(1)The specification of the plastic blank is 230mmxl65mmx50mm, 5 pieces per box, sealed in plastic bags, weighing 25kg.The plastic should be stored in indoor warehouse, preventing from direct sunlight, keeping away from high temperature environment, and well waterproof. The plastic will be difficult to pound because of the plasticity value decreases after too long a period of time, so the plastic produced should be used as soon as possible after arriving at the project site.
(2) During or after construction, the plastic liner is not allowed to contact with water. When contacting with the plastic masonry at the construction of castables, the waterproofing of the plastic should be done.
(3) After the plasticizable construction, the furnace roof insulation must be covered tightly and compacted.
After the plastic construction is completed, the mold should be removed as early as possible, remove the mold too late plastic will become hard, not conducive to scraping, cutting expansion joints, zapping ventilation holes and other finishing processes.
(4) Remove the mold as early as possible also appropriately extend the oven before the masonry degassing natural drying time.
(5) Due to the plastic “zero expansion” design, so plastic masonry in the drying, baking, cracks and expansion joints after the expansion is a normal phenomenon. If the crack width exceeds 10mm, the cracks and expansion joints should be filled with white refractory fiber blankets to prevent the lining of the furnace at low temperatures in the state of fire and smoke, cracks and expansion joints will tend to close around 1350 ℃.
Heating furnace roof with plastic construction is good or bad, directly affect the service life of the heating furnace, so in the heating furnace roof plastic construction process, can be strictly in accordance with the technical requirements of the construction of the construction, and after construction in a timely manner on the construction of the body to repair, you can make the roof with plastic to achieve the best performance, thereby extending the service life of the heating furnace.
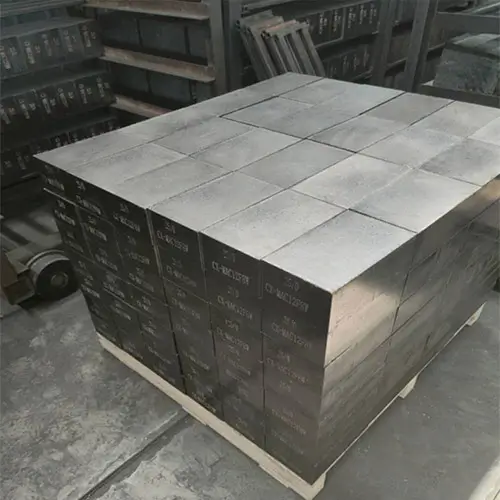