MgO-CaO system refractory is a kind of advanced refractory used in steel making, it has good characteristics of erosion resistance, high temperature resistance, good thermodynamic stability and the ability to purify the steel, for the production of clean steel, especially stainless steel smelting, other refractories can not be compared with it, so in the VOD furnace, AOD furnace, LF furnace and other refining outside the furnace to get a lot of It is widely used in VOD furnace, AOD furnace, LF furnace and other extra-furnace refining. With the transformation of China’s position in the world’s iron and steel industry, from a large steel country to a steel powerhouse, and there are a number of million tons of stainless steel projects completed and put into operation, coupled with Japan and South Korea and other international markets to increase demand, in recent years, the demand for MgO-CaO refractory materials will be a substantial increase in demand. At the same time, the demand for high-quality steel is also higher and higher, so it is necessary to improve the purity of steel. High purity means to strictly control carbon, sulfur, nitrogen, phosphorus, oxygen, hydrogen and other components in the liquid steel; however, cleanliness means to strictly control non-metallic inclusions in the liquid steel.
For the non-metallic inclusions in the steel, it is the main source:
① Refractory melt loss and involvement;
②Oxidation of deoxidized products and air;
③ Involvement of slag.
The cleanliness of steel is closely related to the refractory material and its quality. It is necessary to improve the refractory material in order to improve the quality of refractory material, reduce the melt loss and flaking of refractory material, and at the same time, it is possible to prolong the service life of refractory material.MgO-CaO refractory material has the above unique characteristics, which has become the focus of research and development.
Erosion mechanism of MgO-CaO bricks for AOD furnace linings:
The infiltration and dissolution of the silicate in the liquid phase makes the magnesium-calcium refractory bricks severely eroded. The Ca/Si temperature in the decarburization phase is very high and can reach 1690°C-1720°C, with a reaction time of roughly 40-50 min, and rapid dissolution occurs. Kinetically, the solubility of calcite (<500 μm) in sintered magnesia is higher than that of the large crystals (200-500 μm) contained in electrofused magnesia. In contrast, the “two-phase” is more resistant to damage by acidic slag. During the reduction period of AOD smelting starvation, the chromium return operation and the manufacture of slag with a high content of calcium reduce the slag consistency, increase the wetting capacity, and increase the scouring of refractory bricks, which can cause damage to the bricks.
During smelting, the reaction zone in the furnace is molten or molten. When condensing then the corresponding phase diagram can be applied to explain. For magnesium-calcium bricks, the reaction occurs within the CaO-MgO(MnO)-Al2O3(Cr2O3)-SiO2 system, and the substances obtained are silicates and spinels. The severity of erosion is usually judged by the thinness of the reaction zone. But the treatment of this problem should also be considered from multiple facets: the thicker the reaction layer, indicating that the degree of reaction between the brick and slag hit, the amount of generation is also high, but also indicates that the annual generation of the product will be increased because of the temperature, the reaction product is not easy to be lost; on the contrary, the reaction zone is thin, indicating that the degree of erosion is small, and the generation of the amount is also small, and it is very easy to be lost.
AOD furnace lining brick in the decarburization period experienced a very easy to lose the material produced by the reaction of a period of reduction. The thickness of the reaction zone is ten to twenty millimeters at the end of the smelting process, which reduces the degree of erosion and makes it less susceptible to loss. The high-alumina type precipitated in the reaction zone is not as stable as the high-chromium type of spinel if smelting factors are not taken into account. Due to the formation of many relatively parallel transverse cracks between the brick and the reaction zone, this causes the reaction zone to produce a winning concentration of refractory brick spalling. If the reaction layer spalls, a new layer will continue to erode, which will undoubtedly lead to increased refractory damage.
Transverse cracks are produced by thermal shock and chemical factors:
1) Thermal shock factor
The reason why cracks are created in the home is because there is a large density difference between the original brick zone and the permeable zone, which is also the most sensitive place to drastic temperature changes.
2)Chemical reaction factor
When the AOD furnace lining temperature is reduced, the reaction zone will be cold contraction, resulting in stress concentration resulting in transverse cracks. It bureau surface layer is shallow, yo may be produced in these parts: between the reaction band and permeability band, between the reaction band, between the original brick band and permeability band (less than 10mm).
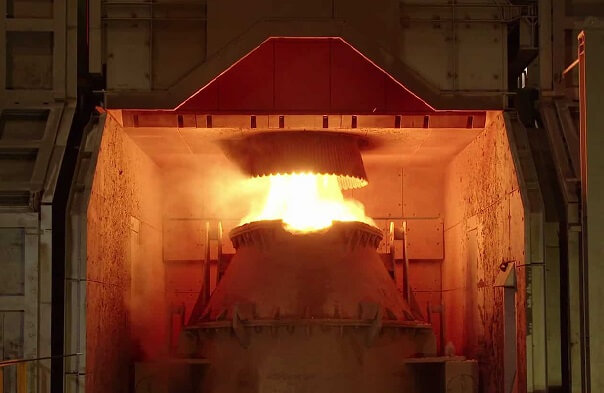
How does an AOD furnace work?
The AOD vessel is a brick lined steel shell with provision for introduction of oxygen and inert gas (argon or nitrogen) below the surface of the molten metal. This introduction causes significant agitation and, therefore, intimate slag-metal contact.
How does an AOD work?
The key feature in the AOD vessel is that oxygen for decarburization is mixed with argon or nitrogen inert gases and injected through submerged Tuyere air nozzles. This argon dilution minimizes unwanted oxidation of precious elements contained in specialty steels, such as chromium.
What is the difference between AOD and VOD process?
What is the difference between the two? The AOD furnace is a refined equipment for the refining method of the oxygen. The VOD furnace is an off -chromium stainless steel refining technology for blowing oxygen and decarburizing under vacuum conditions.
What does AOD stand for in the steel industry?
AOD (argon oxygen decarburization) is an advanced technology for refining stainless steel. It has the advantages of simple equipment, convenient operation, strong adaptability, low investment and low production cost, and is widely used.