After the various raw materials of the casting material are determined, first of all, it should be combined with the present, and then made into a mixture by mixing, and some mixtures also need to be trapped material. According to the nature of the mixture to take the appropriate method of casting molding and maintenance, and finally will have hardened the structure, after the correct baking treatment and put into use.
1.Pellet mixing
The granular materials of all levels of particle size are matched according to the principle of close packing of their waste.
Because the castable material is mostly used to constitute a variety of large cross-section of the structure and made of large blocks, the limit size of granular material can be increased accordingly. However, in order to avoid the coarse particles and cement stone in the heating process between the expansion difference is too large and destroy the combination of the two, in addition to the selection of low expansion of granular materials, should also be appropriate to control the limit particle size. It is generally believed that the vibration molding should be controlled in 10 ~ 15mm below; machine pressure molding should be less than 10mm, for large products or whole structures should not be greater than 25mm; all should be less than 1/5 of the minimum size of the cross-section.
All levels of granular material ratio is generally 3 ~ 4 levels, the total amount of granular material accounted for 60% ~ 70%.
Volume stability at high temperatures, high fineness of the powdered admixture, especially in which there is a part of the ultra-fine powder admixture, the castables at room temperature and high temperature properties have a positive effect, should be matched with the appropriate number of fine powder dosage is generally believed to be appropriate between 30% -40%.
2.Determination of binding agent and coagulant promoter
The type of binding agent depends on the requirements for the nature of the structure or product, corresponds to the material of the selected granular and powdered material, and is also related to the construction conditions.
When manufacturing castables made of non-alkaline granular materials, cement is generally used as the binding agent. The use of cement as a binding agent, should take into account the requirements of the hardened body of the room temperature and high temperature properties, as far as possible to choose fast hard and high strength and low fusible cement, the amount should be appropriate, generally believe that it should not be more than 12% ~ 15%. In order to avoid the hardened body of the medium temperature strength reduction and improve its high temperature performance, the amount of cement should be minimized, and instead of ultra-fine powder dope.
If phosphoric acid or phosphate is used as binding agent, the corresponding concentration of diluted phosphoric acid or phosphate solution should be used according to the requirements of the nature of the hardened body of the casting material and the construction characteristics. The concentration of about 50% of the phosphoric acid is appropriate, and its external dosage is generally controlled between 11% and 14%. If aluminum phosphate as a binding agent, when Al2O3/P2O5 (molar ratio) for 1:3.2, relative density of 1.4, plus the amount of appropriate control in about 13%. This kind of bonding agent formulated castables in the non-heat treatment before the condensation of slow hardening, strength is very low, it is often added less alkaline material to promote its solidification. If the ordinary high alumina cement as a coagulant, the general addition of 2% -3%.
If water glass is used, its modulus and density should be controlled. When the modulus is 2.4-3.0, the relative density of 1.36-1.40g/cm3, the general dosage of 13%-15%. If sodium silicofluoride hardening agent is used, its dosage is generally 10%~12% of water glass.
Other binding agent and its dosage, according to the characteristics of the barren material, the nature of the hardening body and construction requirements.
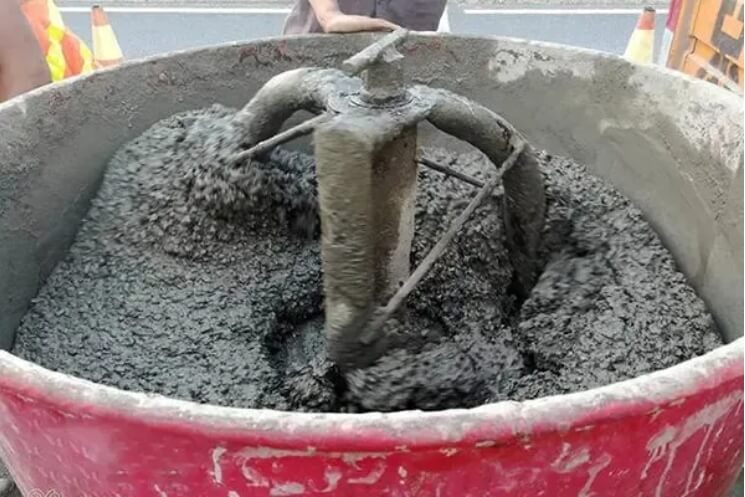
3.Water consumption
All kinds of castables contain water corresponding to the amount of binding agent. Can be in the binding agent and barren material composition mix and then add water, such as easy to hydrate the faster setting speed of calcium aluminate cement is often carried out in this form; water can also be pre-mixed with the binding agent to make a certain concentration of aqueous solution or sol to join, such as the need for pre-hydrolysis to have adhesion to the binding agent is mainly carried out in this form. When the binding agent in the water reaction does not deteriorate, in order to make the binding agent in the casting material distribution is uniform, but also often pre-mixed with water, such as the aforementioned phosphoric acid and water glass and so on is such a treatment.
Generally by the ordinary high alumina cement combined with aluminum silicate clinker made of castables, the use of the water-cement ratio of 0.4 ~ 0.65, of which, to vibration molding, often take 0.5 ~ 0.65, the mixture of water for 8% ~ 10%; machine pressure molding, often take 0.4 or so, the mixture of water for 5.5% ~ 6.5%. In order to reduce the water in the casting material, improve the density of the hardened body, in the casting material should be added to the appropriate plasticizing water reducing agent.
4.Maintain
After the castables are molded, appropriate measures must be taken to maintain and promote hardening according to the hardening characteristics of the binding agent. Calcium aluminate cements should be maintained at appropriate temperatures and under humid conditions. Among them, ordinary high alumina cement should first be covered at a lower (less than 35 ℃) temperature, between the condensation of water or water immersion maintenance for 3 days; low-calcium high alumina cement maintenance for 7 days, or steam maintenance for 24 h. For some metal Eucalyptus salt to be dried and baked. Such as water glass combined, to be stored in the air at 15 ~ 25 ℃ for 3 ~ 5 days, not allowed to moisture, but also by 300 ℃ below the baking; but never in the wet conditions of maintenance, not to mention watering, because of the expansion of the silicate gel water absorption, the loss of adhesion, water dissolved, the strength will also be sharply reduced. Made of phosphate, can first be in the air at 20 ℃ above the maintenance of more than 3 days, and then baked by 350 ~ 450 ℃; not baked, not allowed to moisture and no water.
When the castables constitute the lining and furnace body of thermal equipment, they should generally be baked before the first use in order to make the physical and crystallization water gradually excluded, so as to make their volume and certain properties reach a stable state at the time of use, and to achieve a certain degree of sintering. Whether the sintering system is appropriate or not, it has a great influence on the service life. The basic principle of the development of baking system Chu heating speed and possible dehydration and other physical changes and deformation to be compatible. In the rapid production of the above changes in certain temperature stages, should be slowly warmed or even held for a considerable period of time. If the baking is not appropriate or not baked, immediately and quickly warmed up and put into use, it is very easy to produce serious cracks, or even loose collapse, and may even explode in the extra large and thick parts. Hardened body baking speed according to the bonding agent and structure section size varies.
As far as cement castables are concerned, they can be roughly divided into three stages:
(1) Discharge free water. Increase the temperature to 110~150°C at the rate of 10~20°C/h and hold for 24~48h.
(2) Exclude crystallization water. Increase the temperature to 350°C at the rate of 15-30°C/h and keep warm for 24~48h.
(3) Homogenization stage. Rise the temperature to 600℃ at the rate of 15-20℃/h and keep warm for 16~32h; then, rise the temperature to the working temperature at the rate of 20~40℃/h. Structures with a large cross-section of the heating rate to take the lower limit, insulation to take the upper limit; cross-section of the opposite small.
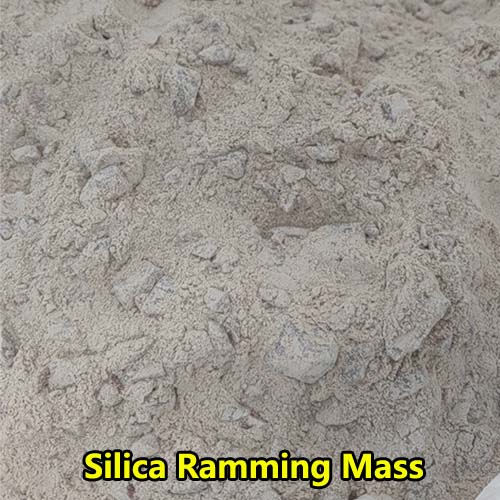