The lining of the medium frequency furnace is usually made of refractory materials of various specifications and sizes. The commonly used refractory materials are mainly magnesium, quartz, aluminum and composite materials. Once the lining is damaged, it will not only affect the power, melting speed and capacity of the medium frequency furnace, but also affect the service life of the lining, and increase the cost of maintenance and replacement. So, what are the reasons for the damage of the lining of the medium frequency furnace? How to repair and prevent it?
1.Reasons for damage to the furnace lining of the medium frequency furnace
1, charging damage
Medium frequency furnace lining mechanical damage mainly from the charging operation. In increasing the block of material when the fall height is too high, smashing the furnace lining; in the addition of flake material cut through the furnace lining, resulting in damage.
2, thermal shock damage
Medium frequency furnace lining thermal shock damage refers to thermal stress lining damage, which is mainly caused by improper use. Liquid metal out of the furnace if not continue to use, the furnace temperature will drop, in the cooling process, the furnace lining not only “thermal expansion and contraction”, accompanied by quartz type inverse transformation, the two together result in the lining of the sintered layer of cracks, glaze warping, flaking, and other damages, when re-opened to the damaged sintered layer may be damaged part of the loss of the lining, resulting in a substantial decline in life expectancy Significantly reduced.
3、Chemical erosion damage
①Iron Liquid Erosion
Medium frequency furnace lining by the erosion of carbon in iron: SiO₂ + 2C-Si + 2CO this erosion melting gray cast iron, ductile iron will be damaged, melting ductile iron damage is more serious.
②Scrap erosion
Medium frequency furnace melting scrap iron in CaO, SiO₂, MnO, etc. is prone to the formation of low melting point slag, especially CaO. Therefore, we should pay attention to the cleanliness of the raw materials used in the furnace lining, oxidation of serious thin-walled scrap produces more slag, should try not to use or batches of use, melting to be added to each furnace less.
③ refractory erosion
High melting point slag is caused by the aluminum in the furnace lining materials, it reacts with the SiO₂ in the furnace lining to generate mullite (3Al₂O₃-2SiO₂), the melting point of 1850 ° C. Therefore, we should remove the aluminum in the intermediate frequency furnace lining raw materials in order to avoid the formation of high melting point slag, erosion and damage to the furnace lining.
④Auxiliary erosion
In the melting operation if the use of slag coagulant or slag flux will aggravate the erosion of the intermediate frequency furnace lining, so try to avoid the use of.
⑤ Carbon deposition erosion
Carbon deposits are found on the cold side of the furnace lining, and can even be deposited in the heat insulation layer. Furnace start-up early use of oil-impregnated waste, such as chips, etc., because the furnace lining has not been fully sintered, CO infiltration into the back of the furnace lining, the occurrence of 2CO-2C + O ₂ reaction, the carbon generated in the furnace lining of the cold side or the air holes of the insulation material, when carbon deposition will cause the furnace ground leakage, and even coil sparking, resulting in damage to the lining of the furnace.
2.Medium frequency furnace lining damage repair method
1、Join the refractory repair
Medium frequency furnace outlet refractory materials and furnace wall joints cracked or damaged repair, available refractory materials can be shaped to push the repair. Repair should first remove the slag, residual iron, coated with water glass, and then add 5% -6% water glass mixed refractory materials beat repair, or repair with non-shaped refractory materials. Erosion range is slightly larger, to use charcoal and other drying, into the mold repair.
2、Adding boric acid to repair
Bottom, side wall tilt part of the burned or damaged furnace lining can be added with the same amount of new furnace boric acid, mixed with uniform refractories pounding. Clean up the broken slag, the cracks will be expanded to 60 ° gap, and then brush with concentrated boric acid, sprinkle a little dry boric acid powder, mixed added to the location of the furnace lining material, with a mallet to tighten and smoothen the surface. If there is a pit at the bottom of the furnace, the slag in the pit should be removed first, and then the thickness of the furnace lining material than the surrounding 20-30mm high added to the pit, and then tighten with a mallet, smoothing the surface, and remove excess material, and then send electricity with 220V voltage.
3、Electrified baking repair
Repair due to corrosion and thinning of the medium frequency furnace lining, should first be stripped of the sintered layer has been infiltrated by steel or slag, and then into the metal mold, and then fill the furnace lining material to the surrounding gap, knotting and then baking sintering. In the cavity mold after demolding, followed by baking, baking in two stages, baking time of the first 4 ~ 6h, medium frequency induction furnace induction loop energized current for the rated current of 20% ~ 60% and gradually adjusted upward, and then adjust the frequency induction furnace induction loop energized current to the rated current of 100% until the completion of the baking.
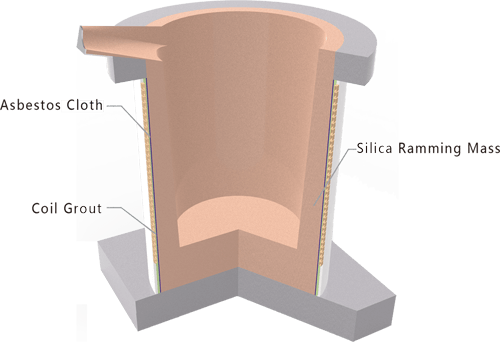
3.Medium frequency furnace lining damage prevention methods
1、Slag acidity and alkalinity should be compatible with the furnace lining material
Magnesium furnace lining material can be eroded by high CaO slag and SiO₂ slag. The amount of CaF in the slag should be controlled, excessive CaF will erode the alkaline furnace lining, so that the slag line area premature melting. When the slag in the fluoride ions, manganese metal ions, such as high or melting pool temperature to 1700 ℃ or more, the viscosity of the solution will also be a sharp decline in the destruction of the furnace lining to accelerate the rate of destruction of the furnace lining life will be greatly reduced.
2、Improve the content of magnesium oxide and slag viscosity
Improve the magnesium oxide content and slag viscosity is conducive to reducing the slag erosion of the furnace lining, but also conducive to improving the effect of slag collection. When the slag alkalinity is low, the magnesium lining erosion is more serious, the life of the lining is reduced; on the contrary, when the slag alkalinity is higher, the erosion of the lining is more slight, the life of the lining is relatively improved. Improve the slag alkalinity and slag in the MgO content, reduce the slag in the FeO content, favorable to reduce the slag on the refractory erosion. Therefore, the use of slagging agent should focus on the selection of materials with high magnesium oxide. Reasonable configuration of slag structure, speed up the slagging speed, shorten the smelting time, reduce the iron oxide content in the slag.
3、According to the furnace lining material selection of suitable slag
Alkaline slag is suitable for magnesium furnace lining, acidic slag is suitable for quartz furnace lining, magnesium-alumina furnace lining can only be applied to weakly alkaline or neutral slag. Alumina furnace lining at high temperature in different pH will show the typical gender, which can adapt to different pH slag, but compared with acidic furnace lining and alkaline furnace lining is a little worse.
4、Improve the erosion and spalling resistance of the furnace lining
Medium frequency furnace lining materials should have high thermal strength, low permeability and low porosity characteristics. But the performance of the furnace lining depends on a variety of factors, such as particle size distribution of materials, physical and chemical properties of materials and sintering temperature of the lining, etc., can be improved by increasing the high-temperature flexural strength and caustic softening temperature to improve the high-temperature resistance of the lining matrix erosion resistance and resistance to spalling.
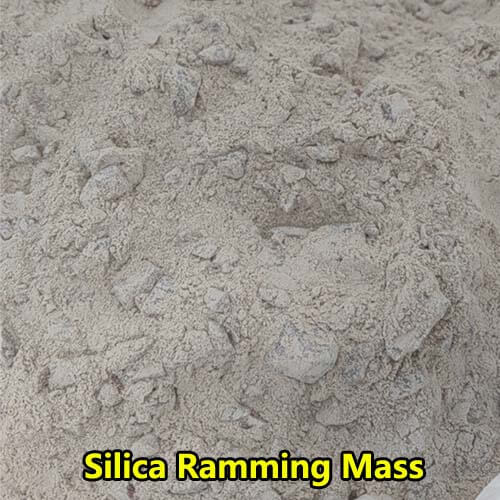