The use of magnesium carbon bricks in the converter, mainly masonry converter lining. According to different parts, different erosion conditions, choose different materials of magnesium carbon bricks, masonry in different parts of the converter, the implementation of integrated masonry. For vulnerable parts, such as trunnions and slag lines, which are often affected by airflow, steel slag erosion and other factors and are seriously damaged, high-grade magnesium-carbon bricks with a carbon content of 16%~18% and the addition of metal antioxidants are used in order to enhance their resistance to erosion.
In the charging side, due to the frequent scouring of steel slag, mechanical stress and other effects, the choice of carbon content of 10% to 14%, and add metal antioxidant high-grade magnesium-carbon brick masonry, in order to enhance its impact resistance and slag coating protection, to prolong the service life of the furnace body. In the furnace cap part, the carbon content of 14% ~ 16% of the middle grade magnesium-carbon bricks, in order to reduce the disappearance of carbon vapour, increase the tightness of the lining, to prevent falling bricks, leakage of steel and other accidents.
In the molten pool part, because it is the main body of the converter, often affected by the erosion of molten steel, air flow and other effects, so the use of carbon content of 16% ~ 18%, and add metal antioxidant high-grade magnesium-carbon brick masonry. In the bottom of the furnace, the use of no metal additives, carbon content of 14 per cent to 16 per cent of the magnesium and carbon bricks. In short, the use of magnesium carbon bricks in the converter, mainly masonry converter body, the implementation of integrated masonry furnace, in order to extend the life of the furnace body, improve the age of the converter furnace.
1. Destruction process and mechanism of magnesium carbon bricks
Destruction process of magnesium carbon bricks
Magnesium carbon brick damage, first of all, due to the brick carbon oxidation, the formation of decarburisation layer, coupled with high temperature magnesium oxide and graphite thermal expansion rate difference (1000 ℃, respectively, 1.4% and 0.2%), resulting in loose structure, strength reduction, and then by the slag erosion, mechanical scrubbing and other roles, the brick in the magnesium oxide particles are gradually eroded by melting, layer by layer, resulting in the destruction of magnesium carbon brick. The destruction process of magnesium carbon brick is: oxidation → decarburisation → loosening → erosion → scouring → shedding → destruction.
Damage mechanism of magnesium carbon bricks
A large number of research work has proved that above 1600 ℃, the following reaction is the main reason leading to the destruction of magnesium-carbon bricks.MgO(s) +C(s) → Mg(g) +CO(g) magnesium-carbon bricks destruction, first of all, the work of the lining of the hot surface of the oxidation of carbon, the formation of a layer of thin decarburisation layer, carbon oxidation is due to the slag in the iron oxides and the O2 in the air, as well as CO2, SiO2, and other oxides Oxidation results, as well as dissolved in the liquid steel or brick in the MgO vaporization of carbon; followed by high-temperature liquid slag penetrate into the decarburization layer of the pores or due to the role of heat cracks in the reaction with magnesium oxide in the brick to form a low melting point compounds, resulting in the surface layer of bricks and weakened texture, in the powerful slag churning, mechanical scouring and other stresses layer by layer off, resulting in magnesium-carbon bricks, loss of section, and so on and so forth, and so on, and so forth, and so forth, and so forth, and so forth, and so forth, and so on. So week after week, the furnace lining becomes thinner and thinner, and the furnace is eventually mended, repaired and stopped.
(1) Carbon oxidation of magnesium carbon bricks is firstly the result of oxidation of carbon in the bricks, the oxidation of carbon is carried out through the following reactions.
Due to the oxidation of carbon, destroying the network structure of carbon in the brick, thus making the organisational structure loose, the strength of the product is reduced, and at the same time increase the porosity, but also exacerbate the slag on the erosion of the brick.
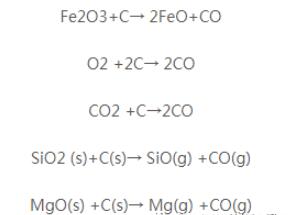
(2) The effect of porosity in magnesium carbon bricks, especially open porosity, the destruction of magnesium carbon bricks has an important impact.
In the process of using magnesium carbon brick, mainly through the pores to promote the oxidative destruction of carbon, and then exacerbate the slag on the brick lining of the erosion, thus causing the destruction of magnesium carbon bricks. Existing in the brick in the open air holes, cooling from the external air inhalation. When reheated, the oxygen in the air reacts with the surrounding carbon to produce CO, and this process is repeated over and over again, increasing the porosity. In addition, the binding agent present in magnesium-carbon bricks is an important factor in the generation of porosity. As the magnesium carbon brick binding agent, generally often use phenolic resin. Adding 3%~4% of phenolic resin, the porosity after moulding is low, about 3%. But in the process of use, phenolic resin heating decomposition of H2O, H2, CH4, CO, CO2 and other gases evaporated out of the gas evaporation pathway will be formed pores, but also make the porosity increase. In this way, the presence of oxygen in the air and the slag in the oxides and so on will be eroded through the pores of the brick, on the one hand, to promote the oxidation of carbon damage, on the other hand, exacerbated the slag and the brick in the reaction of MgO, resulting in magnesium-carbon bricks damage. Such a process over and over again, through the oxidation of carbon, slag erosion, on the one hand, the destruction of the carbon network structure in the brick, so that the organisational structure of the loose, high-temperature strength reduction, on the other hand, the formation of the surface of the brick low melting point of the compounds, weakened and deteriorated, so that in the powerful slag churning, mechanical scrubbing, thermal shock, and other stresses layer by layer to come off, resulting in magnesium carbon bricks damage.
2.Solution
1.The use of high-quality electrofused magnesium sand as raw material high-quality electrofused magnesium sand has the advantages of perfect crystalline development, large grain size, high bulk density, low chemical activity, erosion resistance, etc., and at the same time, resistance to carbon reduction is strong, can prevent the erosion of MgO particles. Secondly, the high content of magnesium oxide, low impurity content, especially the low content of SiO2, the structure of the silicate phase is less, resisting its reaction with the graphite in the matrix, preventing the oxidation of carbon. In addition, the degree of direct bonding of crystals is high, which can avoid the fusion caused by the liquid phase generated at the boundary of grains at high temperature and prevent the penetration of slag. Due to the high price of high quality fused magnesium sand, so according to the magnesium carbon bricks in the converter on the different parts of the use, with sintered magnesium sand organisation production. That is, for the vulnerable parts, to use high-quality fused magnesium sand, for the damage is not too serious parts, to use sintered magnesium sand.
2.Improve the purity of graphite graphite is the highest known melting point of the monomers, up to 350 0 ℃, its coefficient of thermal expansion is small, good chemical stability, graphite purity of magnesium-carbon bricks have a greater impact on the use of performance. With the improvement of graphite purity, magnesium carbon brick erosion index decreased sharply, high temperature flexural strength index increased significantly, generally use carbon content greater than 95%, preferably greater than 98% of the graphite. Because, the higher the purity of graphite, the less ash, contains less SiO2, and SiO2 at high temperatures, can make the brick in the oxidation of carbon, resulting in increased porosity, loose structure, but also with MgO, Fe2 O3, etc. to form a low fusion, accelerate the destruction of magnesium carbon brick. In addition, carbon thermal conductivity, expansion coefficient is small, the slag is not easy to wet, therefore, can improve the products of thermal shock resistance, to prevent the slag through the pores to the internal erosion of the brick body.
3.There are two main weaknesses of magnesium-carbon bricks with metal antioxidants.
Poor antioxidant property and low strength at high temperature. In order to overcome these two weaknesses, adding appropriate amount of metal antioxidant is one of the effective ways. This can not only improve the antioxidant property of the products, but also can effectively improve the high temperature strength of the products.
At present, the commonly used metal antioxidants are metal Al powder and Si powder. Metal Al powder melting point of 659 ℃, and the affinity of oxygen than carbon, which can inhibit the oxidation of carbon. It is used in the process, with the increase of temperature, gradually generated AI4C3, Al2O3, MgO-Al2O3. its reaction formula is as follows.
AI4C3 is the high-temperature phase, connecting magnesium sand and graphite particles, which can improve the high-temperature strength of the products; the generation of AI2O3 is accompanied by a certain volume expansion, resulting in the enhancement of the matrix density of the products, and the strengthening of the antioxidant property; the generation of magnesium-aluminium spinel Al203-MgO increases the high-temperature phase of the products, which improves the high-temperature performance of the products. Therefore, adding metal aluminium powder can improve the antioxidant property of magnesium-carbon bricks.The affinity of Si powder with oxygen is larger than that of carbon, in the process of using, Si reacts with C to generate Si C, and reacts with MgO to generate 2 MgO-SiO2 with high melting point, accompanied by a certain amount of volume expansion, which inhibits the oxidation of carbon. The reaction formula is as follows.
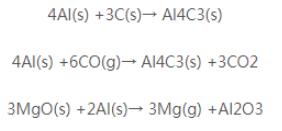
AI4C3 is the high-temperature phase, connecting magnesium sand and graphite particles, which can improve the high-temperature strength of the products; the generation of AI2O3 is accompanied by a certain volume expansion, resulting in the enhancement of the matrix density of the products, and the strengthening of the antioxidant property; the generation of magnesium-aluminium spinel Al203-MgO increases the high-temperature phase of the products, which improves the high-temperature performance of the products. Therefore, adding metal aluminium powder can improve the antioxidant property of magnesium-carbon bricks.The affinity of Si powder with oxygen is larger than that of carbon, in the process of using, Si reacts with C to generate Si C, and reacts with MgO to generate 2 MgO-SiO2 with high melting point, accompanied by a certain amount of volume expansion, which inhibits the oxidation of carbon. The reaction formula is as follows.
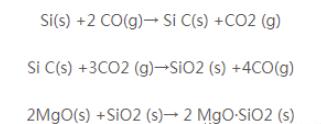
The generation of these reaction products, on the one hand, often block the channel or fill the pores to prevent the transfer of CO and CO2 to the brick to protect the carbon in the brick less oxidised or not oxidised; on the other hand, the formation of a new high-temperature phase of the material, which not only improves the density and strength of the brick, but also builds up the antioxidant and erosion resistant to a new layer of protection to inhibit the oxidation of carbon, and improves the resistance to erosion of the brick.
4.Selection of thermosetting phenolic resins as binding agents
For magnesium-carbon bricks, the selection of good binding agent is very critical. Due to the poor wettability of carbon materials, it is difficult to form a high-strength composite material with magnesium sand, while the phenolic resin has high fixed carbon content, good wettability, can be uniformly distributed in the MgO particles and graphite on the surface, firmly connecting the magnesium sand with the graphite particles, coupled with its ability to form a continuous network structure of carbon at high temperatures, so it greatly improves the magnesium-carbon bricks’ strength, and enhances the products’ anti-erosion ability.
3.Conclusion
(1) Magnesium carbon brick damage, first of all, due to the oxidation of carbon, the formation of decarburisation layer, resulting in loose product structure. Plus high temperature, slag erosion, mechanical scouring and other roles, resulting in brick layer by layer fall off, resulting in magnesium carbon brick damage.
(2) The use of high-quality fused magnesium sand and carbon content of more than 98% of the graphite as raw materials, add an appropriate amount of metal aluminium powder and silicon powder for the antioxidant, the choice of thermosetting phenolic resin as a binding agent for the manufacture of magnesium-carbon bricks.
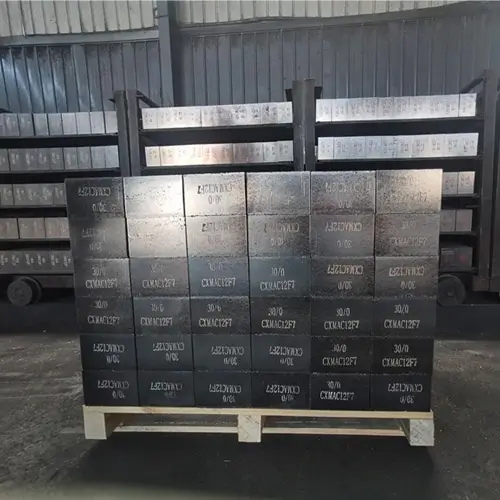
More details about Magnesium carbon brick
What are magnesia carbon bricks used for?
Magnesia carbon refractory bricks are widely used in steel industry, the primary consumer of refractory linings, such as basic oxygen furnaces, electric arc furnaces, and ladle furnaces.
What are the properties of MgO-C bricks?
MgO-C bricks are composed of magnesia clinker, flake graphite, antioxidants, resin components, etc., and have high resistance to corrosion, spalling, and slag penetration thanks to the characteristics of their constituents.
How do you make magnesia carbon bricks?
The raw materials are prepared in a predetermined proportion and mixed in a strong sand mixer. The order of feeding is magnesia aggregate – Binder – graphite – fine powder and additives, and the mixing time is 15 – 45 minutes. In order to mix evenly, phenolic resin is usually heated to 35-45 C before mixing.