Some of the problems that occur during the use of tundish refractory materials are the quality of the material itself, and some are related to the on-site construction and need to be carefully observed and analyzed.
Dry material has no strength
Before the tundish is put into use, the dry material of the working layer needs to have a certain low temperature strength, which is mainly obtained by vibration and baking. After the dry material is demolded by vibration and baking, there will often be local lack of strength or low strength, which is very easy to cause collapse and affect the production of continuous casting cases.
After long-term observation and analysis, the main reasons for the lack of strength or low strength of the dry material are:
①Baking problem: The tundish baking device used in the steel plant is a gas baking device, which will cause a large number of pipelines to focus after long-term use. The tar or the burner is damaged, causing the partial baking effect to be poor and leading to no strength or low strength.
②The dry material is damp: The dry material is composed of 70% particles and 30% fine powder. The fine powder contains magnesia and binder. Because of its high specific surface area, the fine powder is easy to absorb water and become damp. The magnesia and the binder absorb water after they absorb water. Chemical deterioration causes the bonding agent to fail and cannot produce bonding strength during baking;
③Uneven mixing of binder: When producing dry materials, various particles, fine powders and binders need to be put together and mixed uniformly. Sometimes, the mixing is uneven due to human factors or mixing equipment. Some dry materials do not have binder or the content of bonding agent is rarely resulting in partial loss of strength after baking and demoulding.
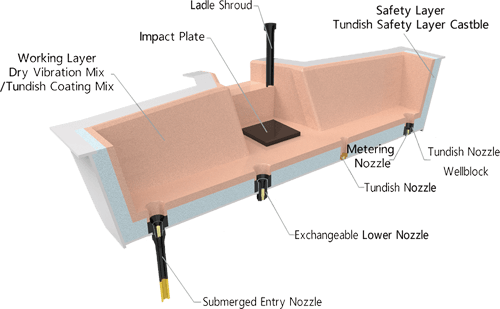
Solution:
First of all, it is necessary to ensure the baking effect of the roaster, regularly purge the gas pipe, remove tar and dust, and replace the damaged burner in time.
Secondly, it is necessary to ensure that the dry material is dry and mixed evenly.
Thirdly, Nozzle cracking steel infiltrating the tundish nozzle with zirconium core in the pouring process is easy to crack and lead to steel infiltration, often forcing continuous casting to block production or abnormal shutdown. The analysis believes that the nozzle cracking is mainly due to the poor thermal shock resistance of the zirconium core.
Solution: The bulk density of the zirconium core should not be too high. The higher the bulk density, the worse the thermal shock resistance. Appropriately thickening the nozzle body can prevent molten steel from seeping out.
Ladle casing fracture. The ladle casing is located between the ladle nozzle and the tundish. Its metallurgical function is to prevent the molten steel from splashing and being oxidized during the process of the molten steel flowing from the ladle into the tundish. The most common problem in the use of large-clad casing is fracture. There are two reasons for the fracture. One is the poor thermal shock resistance of the large-clad casing, and the other is that the large-clad casing and the steel ladle need to be replaced when replacing the ladle. The nozzle is separated. When the casing and the ladle nozzle are tightly adhered, the steelworker applies an external force to the ladle casing, causing the casing to break.
Solution:
First, use materials with small thermal expansion coefficient and elastic mold to produce the casing to improve thermal shock resistance;
Second, when the casing and the water outlet cannot be shared, no external force can be applied to the lower part of the casing, and the upper part of the casing can be steel External force is applied to the shell to separate it.
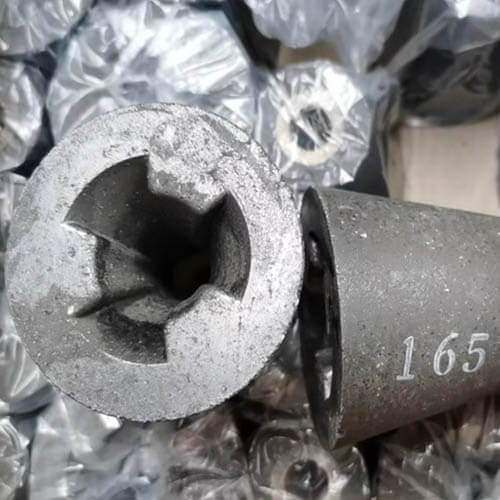