The middle bag is an important production equipment in the continuous casting process of steel, the bag age, life length directly affects the yield of continuous casting billet as well as the continuity and stability of the production organization. Extend the service life of continuous casting intermediate package, not only can shorten the operation time of intermediate package replacement, reduce the consumption of gas for baking package and site workers masonry construction labor intensity, but also conducive to reduce the continuous casting billet reattachment scrap, improve billet qualification rate, as well as effectively reduce the intermediate package single package with refractory material consumption per ton of steel to improve the purity of molten steel. Through a machine first-class and two machine two-stream slab continuous casting intermediate packages with refractory materials for process adjustment and optimization, and after a number of industrial field application practice results show that after adjustment and optimization of the intermediate packages with refractory products are able to meet the continuous casting production process of the lifting of life and use of the requirements, help to achieve the goal of reducing costs and increasing efficiency.
Iron and steel industry is an important basic industry of national economy, and has a very important strategic position in the process of national economic development. With the transfer of international industries and the rapid development of China’s national economy, China’s iron and steel industry has made remarkable progress, especially the continuous optimization and development of the continuous casting process, which has played an important role in promoting the development of the iron and steel industry.
The intermediate package is one of the main equipment of continuous casting production process, with the role of stabilizing and diverting the flow, which plays a very important role in the continuous casting operation and ensuring the quality of molten steel. Stable pouring of the intermediate package is conducive to prolonging the residence time of steel in the intermediate package, which is conducive to homogenizing the temperature and composition of molten steel.
At present, the domestic continuous casting production process has made great progress, especially billet continuous casting, the intermediate package continuous pouring service life continues to improve, but how to further improve the slab continuous casting intermediate package age, and to achieve the same level with the billet intermediate package, is still the direction of the industry’s efforts.
1.Technical measures
1.1 Enhancement of dry material in the slag line
Slag line dry material is one of the most important factors restricting the lifespan improvement of continuous casting intermediate ladle. In the field process conditions, masonry form a certain situation, the refractory life of intermediate ladle mainly depends on the intermediate ladle working lining steel chemical erosion, high temperature melt damage and mechanical scouring [2], therefore, to improve the slag line part of the dry material of the slag erosion and scouring resistance has become the main task of adjusting the dry material of the slag line.
Sampling and analyzing the intermediate package slag of the covering agent in use at the continuous casting site, and comparing the chemical composition with the slag samples of another manufacturer’s covering agent previously applied in the laboratory, the key factors affecting the erosion rate of the dry feed were found, and at the same time, a review test was conducted in the laboratory to verify the validity of the test. The review test is based on the intermediate package slag samples of covering agents from the former and the latter two manufacturers, and the crucible erosion resistance test of six different programs of dry materials is carried out.
The test program to sintered magnesium sand and electrofused magnesium sand, etc. as the main raw materials, the maximum critical particle size selection for the 5mm, the combined addition of the above raw materials for the mass of the total 90% ~ 95%, powdered heatset phenolic resin for the mass of the total amount of 3% ~ 5%, the addition of other powders for the mass of the total amount of 1% ~ 3%, and the rest of the additives for the total amount of mass of the total amount of 0.2% ~ 1.0%.
The crucible was molded according to 100mm×100mm×100mm mold, baked at 250℃×3h, cooled and demolded, and then a certain amount of intermediate packet slag samples were added and calcined at high temperature.
In order to improve the slag line dry material in a long time under the application of slag and molten steel and other erosion and scouring ability, reduce the rate of erosion, the production of different continuous casting intermediate packet site for the needs of the process situation, improve the main raw material used in magnesium sand grade.
1.2 Retrofitting of impact zone guards
Intermediate ladle impact area parts due to the static pressure and impact of molten steel, compared with other parts of the working environment is more severe, especially in the working liner structure thickness and service life requirements are higher, easy in the slag line parts of the molten steel through the packet accident, in the middle of the packet in the field of the lifting life of the process of a greater security risks, so for the middle of the packet impact area parts of the scour erosion of the serious situation in the design of the working liner. Work lining, the use of guard plate and dry material composite structure, the guard plate mounted on the inside of the dry material, in the middle of the packet does not change the current working capacity on the basis of the guard plate to improve the anti-injection flow overturning scouring ability, increase the overall service life of the intermediate packet work lining.
Combined with the specific conditions of continuous casting process, the thickness of the impact zone guard plate is designed as 50mm, and the rest of the design size is determined according to the shape of the impact zone. The production of the guard plate mainly adopts magnesium casting material for one-piece casting molding, the material to sintered magnesium sand and electrofused magnesium sand as the main raw material, the maximum critical particle size selection for 8mm, the use of ultra-micron technology for the combination, and add a certain proportion of fused quartz and spinel powder, so that the material in the flexural strength, compressive strength has been effectively improved at the same time, but also significantly enhance the resistance to infiltration, the site combination of the installation and then use, the impact zone working layer can play a good role. The working layer in the impact zone can play a good protective role.
1.3 Improvement of slag wall and dam materials and structures
The main role of the intermediate package slag wall is to change the trajectory of the steel in the package, so as to achieve the following functions: reduce the flow rate of steel, reduce the scouring of steel on the refractory materials in the package; prolong the residence time of the steel in the package, so that the inclusions in the steel have enough time to fully collision, aggregation, uplift, in order to purify the steel; uniform distribution of the steel to the basic time to reach the various streams of the flow port, so that the streams of the Temperature to maintain the same, reduce the pull leakage and knot plug phenomenon; change the distribution of the flow field in the package, so that the hydrodynamic state of steel water to achieve the best; reduce the stagnation area to increase the laminar flow area.
The improvement of the slag wall is mainly based on material adjustment, the original design structure is not changed. Slag wall material design selection were used in the slag line parts of aluminum and magnesium, the body parts of high alumina, production process design for the use of two kinds of casting material for composite casting one-piece molding. Slag line part of the material program to aluminum and magnesium raw materials as the main raw material, according to Andreessen close stacking theory, selected q = 0.27, raw materials, the largest particle size selection for the Dmax = 15mm, aggregates are mainly used in the high alumina raw materials, the addition of 70% of the total amount of mass ~ 75%, fused magnesium-aluminum spinel powder or fused magnesium sand powder for the total amount of mass of 8% ~ 12%, and with the composite micropowder technology, and the combination. At the same time, the addition of stainless steel fiber for the total mass of 0.6% ~ 0.8%, in addition, through the rational use of new dispersants to significantly reduce the prefabricated parts molding the amount of water must be added, so that the castables in the molding of the minimum amount of water required to obtain the highest degree of mobility, so that it can achieve the most tightly stacked with a high bulk density and ambient strength, low apparent porosity, as well as excellent resistance to slag erosion and permeation resistance. The body part material scheme is based on high alumina raw material as the main raw material, and the addition of electrofused magnesia-alumina spinel powder or electrofused magnesia sand powder is eliminated on the basis of the slag line part material scheme.
Compared with the magnesium or magnesium-silica material program, the improved slag retaining wall material program has been substantially improved in terms of flexural and compressive strength, as well as scouring and penetration resistance.
The main function of the intermediate ladle dam is to improve the flow field of molten steel, which is conducive to the uplifting of inclusions in the steel and the improvement of the internal quality of the molten steel. Aiming at the use of the intermediate package dam requirements, in order to avoid the lifting of life in the application of intolerance of scouring, fracture, floating and other issues, the original magnesium or magnesium-silicon material program has been adjusted, mainly based on the above slag retaining wall body part of the aluminum castables program, and combined with the actual production process of continuous casting of the situation to do the corresponding adjustments.
In addition, for the application of the intermediate package block dam of the second-flow slab of the second machine, the structure of the flow steel hole is adjusted, the original overall structure is not changed, and the adjusted flow steel hole situation is shown in Figure 1

1.4 Optimizing the design of the bottom structure of the flow stabilizer
The main role of the intermediate ladle flow stabilizer is to avoid the direct impact of high-temperature molten steel on the bottom of the intermediate ladle, to equalize the residence time of molten steel in the intermediate ladle, to ensure the stability of the liquid level of the intermediate ladle, and to effectively prolong the service life of the materials in the ladle.
For the current application status quo of the intermediate ladle flow stabilizer, without changing the overall design structure of the current flow stabilizer, the original bottom single-layer prefabricated cast structure is changed into a composite structure, i.e., one or more pieces of aluminum-magnesium-carbon impact plates are buried in the casting material in the center part of the impact area at the bottom of the flow stabilizer. The improved flow stabilizer made by the above technical measures can greatly improve the bottom scour resistance, and the specific composite structure can be seen in Figure 2.
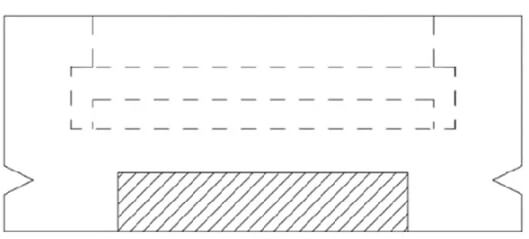
1.5 Material and design of adjusting plugs and spouts
Slab continuous casting intermediate package is mainly used to plug the rod and the mouth of the matching flow control, with the increase in the number of continuous casting furnace, plug the rod in the use of the main problems that are prone to occur is the slag line resistance to erosion, the rod head is not resistant to scrubbing, easy to form the shape of the tip, the tip of the low strength of the steel impact by the brush off, resulting in the whole plug the rod becomes shorter than the continuation of the effective control of the flow, constraints on continuous casting of the life of the improvement.
For the needs of slab continuous casting process, respectively, the slag line structure of the plug rod and the head material for technical adjustment, mainly:
(1) in the plug rod slag line part of the outer layer of 20 ~ 30mm thickness of Zr O2-C ring, in order to enhance the anti-erosion performance;
(2) plug rod head using magnesium-aluminum-carbon, the raw material is mainly used in the selection of electrofused magnesium-aluminum spinel and electrofused magnesium sand of the large crystals, in the improvement of the magnesium oxide content, at the same time, the proper Reduce the carbon content, reduce the chance of reaction between steel and rod head material, in order to increase the resistance to scouring and erosion resistance, adjusted plug rod example can be seen in Figure 4.
At the same time, a series of technical measures have been adjusted for the water spout, mainly:
(1) using composite double-layer zirconium structure with magnesium oxide-stabilized zirconium oxide bowl (Zr O2≥94%) to improve the scour resistance and erosion resistance of the water spout;
(2) optimization of the water spout sliding plate surface material scheme to improve the wear-resistant performance to meet the requirements of multiple replacement of the submerged water spout;
(3) Improving the upper spout from a smooth profile to a grooved profile effectively solves the problem of steel entrapment between the spout seat bricks.
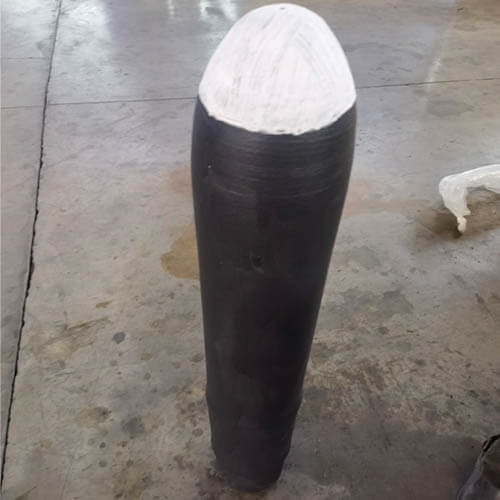
2.Application results
After the completion of the long-life refractories for intermediate packages technology improvement, respectively in a machine first-class, two machine two-stream large slab continuous casting site for a number of long-life continuous casting test applications, have reached the expected results.
A machine first-class slab continuous casting site organization carried out 150h continuous casting test application, the actual maximum continuous casting time reached 156h25min, steel type for 45, 50 high carbon steel mixed pouring, a total of 240 packets of cast steel, casting section for 280mm × 1800mm, the average pulling speed of 0.75m/min, over the amount of 27664t, the casting billet total length of 7009m. Test package continuous casting process during the arrangement of personnel throughout the temperature measurement without exception, statistics off the line and turn over the package after the measurement data results can be seen, the improved material can meet the site 150h continuous casting service life requirements, especially the impact zone guard plate and slag wall slag line parts, the average erosion is only 30 ~ 35mm, according to the erosion rate, can still continue to be used.
Second machine two stream slab continuous casting site organization for 50h continuous casting test application, the actual maximum continuous casting time reached 50h30min, steel grade for Q355B, a total of 86 packets of steel pouring, casting section of 200mm × 1600mm, the average pulling speed of 0.95 ~ 1.0m/min, the total amount of steel over 14789t. Test package throughout the use of no abnormality, and did not do to reduce the liquid surface Processing, statistics off the line and turn over the package after the measurement data found that the improved materials are able to meet the needs of the site 50h continuous casting service life.
The results of industrial application practice shows that by adjusting and improving the long-life technology of refractories for slab intermediate package, it can effectively improve the overall anti-erosion and anti-penetration performance of refractories, make the service life of the first-class slab intermediate package of one machine to 150h and the service life of the second-class slab intermediate package of the second machine to more than 50h become a reality, and shorten the gap with the highest service life of the intermediate package of the square billet continuous casting. It is conducive to reducing the cost consumption of refractory materials per ton of steel, improving the operational efficiency of continuous casting production, and safeguarding the quality of finished steel products, which is of extraordinary significance for carbon emission reduction in the iron and steel industry.
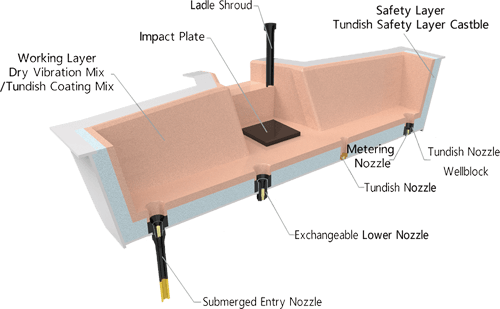