Configuration of refractories for converters
In the dismantling of the furnace lining after use, it was found that the damage was caused by the inability to use individual parts of the severe erosion, while many other parts could be used, but had to be discarded in order to build a new lining. Therefore, people put forward a comprehensive masonry, balanced lining concept, that is, for different parts of the lining of the erosion state to choose a different quality of the lining brick.
Furnace mouth part of the temperature change is intense, by the slag and high temperature exhaust gas wash is more serious, so the refractory bricks used for the mouth of the furnace must have a high thermal shock resistance and slag resistance.
Furnace cap area is mainly subject to the furnace gas scouring and blowing slag spatter, but also by the impact of rapid changes in temperature and dusty exhaust gas scouring, it should be used to slag resistance and good thermal shock resistance of magnesium-carbon bricks.
The lining bricks in the furnace wall area, especially the lining bricks on the charging side, are subject to the scouring of molten steel and slag, and are required to have high high-temperature strength.
Slag line, trunnion area is the converter furnace lining in the most demanding conditions of use of the parts, by the liquid steel and slag scouring and erosion and gas scouring of the furnace, requiring the use of the best erosion-resistant brick masonry.
In the converter furnace lining, the outlet brick is another brick with special significance. Large converter outlet due to the large amount of steel, by the liquid steel scouring, the use of very harsh conditions, the general life is relatively short, far less than the life of the furnace lining, so it is necessary to frequently replace the outlet brick. From the style of the outlet brick can be divided into a whole and segmented assembly type. At present, it is believed that the overall magnesium-carbon steel outlet is more effective, long life, easy to replace.
In the smelting process due to the different working conditions of each part, the working layer of each part of the erosion is not the same, the company takes a comprehensive masonry way, in order to achieve a balanced erosion of the overall furnace lining. Comprehensive masonry, should be based on the specific conditions of different manufacturers, choose 3-6 different grades of brick type, respectively, masonry in the slag line, trunnion, furnace wall, melting pool and other parts of the slag line, in order to obtain the best economic benefits.
According to the above requirements, the configuration scheme of refractory materials for 180t converter in a steel plant is shown in Fig. 1 and Fig. 2.
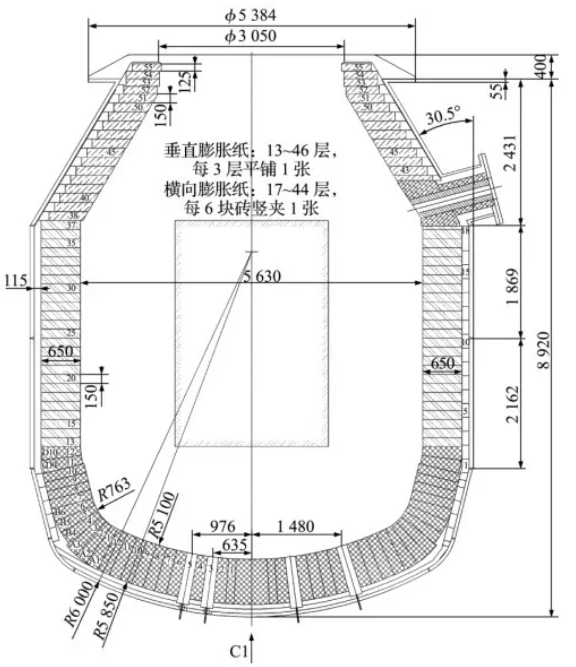
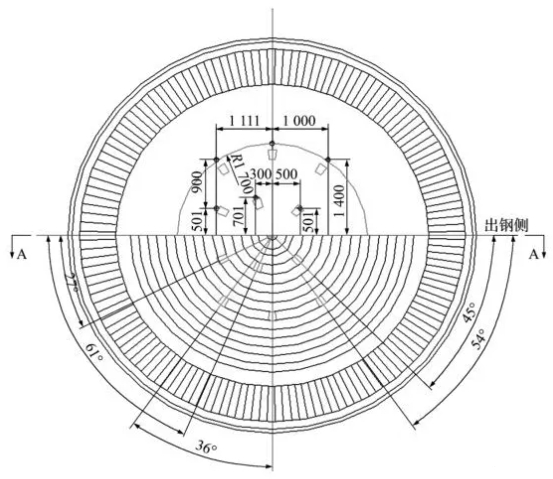
It can be seen from Fig. 1:
① Furnace opening and cap: permanent layer of non-standard brick masonry, working layer of 500-650mm thick magnesium-carbon brick masonry, the use of casting material between the furnace opening and the furnace shell;
② Furnace body: 1 layer of 115mm thick sintered magnesium bricks on the permanent floor and 650mm thick magnesium carbon bricks on the working floor.
③ Melting pool: permanent layer of 1 layer of 115mm thick sintered magnesium bricks, working layer of 700-750mm thick magnesium carbon bricks.
④ Furnace bottom: permanent layer of 2 layers of 75mm thick sintered magnesium bricks, working layer of 750mm thick magnesium carbon bricks.
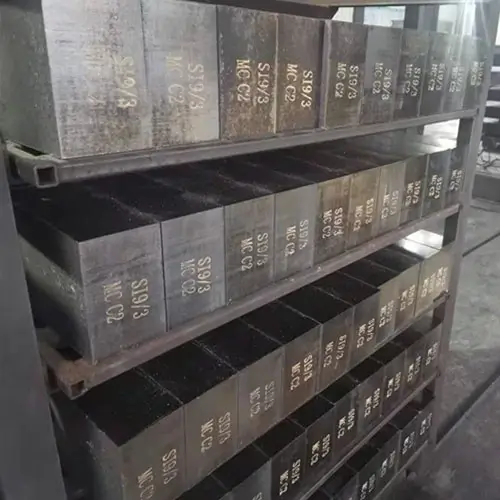